無駄のない「ものづくり」に欠かせないコンピュータシミュレーション。
20年近く前、東京農工大学工学部の桑原利彦教授は、某自動車メーカーの研究者からこう相談を受けた。
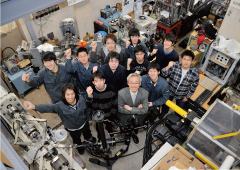
「コンピュータシミュレーションの結果と現場の実測値が合わない」
議論と熟考を重ねるうちに1つの疑問に行き当たる。
材料の変形予測を行う計算のベースとなる材料モデル(構成式)は正しいのか?
いまや国際標準化(ISO規格化)の最終段階にまで進められてきた
ものづくり革新を推進する「二軸引張試験方法」。
生み出されたのは、この疑問が始まりだった。
科学で産業に貢献したい
産業の基幹である農学と工学を中心とする東京農工大学は、早くから産学連携の重要性に着目し力を入れてきた大学だ。実学に軸を据えた研究や成果発信力に対する企業の評価も高く、外部資金比率や教員一人あたりの民間企業との共同研究件数も常に国内の大学でトップクラスを誇る。また国際的な産学連携活動にも積極的だ。
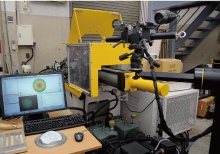
桑原教授は、ものづくりの基礎研究となる塑性力学と塑性加工学を研究している。金属は大きな力を加えて変形させると元の形に戻らない。この金属の性質が塑性だ。自動車、航空機、家電、電子機器などさまざまな工業製品は塑性を利用してつくられている。日本のものづくりはプレス成形に代表される高度な塑性加工技術で世界をリードしてきた。
桑原教授は、研究テーマを選ぶときに「幹となる研究かどうか」という観点を大切にしている。研究テーマ選びに悩んでいたときに、かつて博士課程研究の指導教員であった神馬敬教授(東京工業大学)がかけてくれた言葉をいまでもよく覚えている。「そこから枝葉が伸びるような幹となる研究をやりなさい」。その一言で開眼した桑原教授だが、当時は具体的に何をやるべきなのか、よくわからなかったという。
1995年、桑原教授は、当時日産自動車の研究者であった高橋進博士(現在日本大学教授)と頭を悩ませていた。「コンピュータシミュレーションの結果と現場の実測値が合わない。どうしてだろう?」。いろいろと議論していく中で1つの疑問に行き当たった。コンピュータシミュレーションで使用している材料モデル(構成則)に問題があるのではないか。
応力(材料に作用する単位面積当たりの力)とひずみ(材料の伸び縮みによる単位長さ当たりの変形量)の関係を数式で表現する材料モデルは、19世紀中頃にはじめて定式化されて以来、さまざまなモデルが提案されている。コンピュータシミュレーションを行う場合、材料の変形特性に合わせて材料モデルを選択するべきではあるが、数多くの材料モデルから最適なモデルを選ぶのは簡単ではない。コンピュータシミュレーションの精度を決める因子の中で、材料モデルの妥当性検証は大きなポイントになる。そう気づいたとき、「これは幹となる研究だ」と直感したという。日本のものづくり復興に向けた基礎研究としても有益だが、「さて、何から始めたらいいのか」。材料モデルの妥当性を証明するための試験方法も試験装置もなかった。
画期的な試験方法は国際標準化を推進中
従来、材料特性の試験方法としては、短冊状の試験片を使った一軸方向の引張試験が行われている。だが、それでは応力の状態はX軸上の1点とY軸上の1点しか測定できない問題がある。ものづくりの現場では二軸方向にさまざまな力を加えることで材料を加工している。材料モデルの妥当性を証明するためにはX軸方向とY軸方向の応力の比率を任意に変えたときの材料の変形特性を測定することが必要だった。「しかしどうやったら金属の薄板に対して応力の比率を自在に変えながら引張試験を行うことができるのか。これは難問でした」。試行錯誤の結果、試験片の形状は腕に7本のスリットを有する十字形状と決定した(下図)。さらに桑原教授は、学生と一緒に十字形試験片を二方向に引っ張る試験装置も設計しつくりあげた。
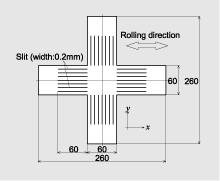
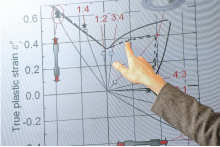
1998年、十字形試験片を用いた二軸引張試験方法に関する論文が初めてジャーナルに掲載された。そしてその後も二軸引張試験方法を用いた材料モデルに関する基礎研究を継続した。その結果、成形シミュレーションの精度を向上させるためには材料モデルの高精度化が必須であることを多くの解析事例を通して立証できた。
「シミュレーションソフトウェアがどんなに高度でも、材料モデルが適切でなければ正しい答えは得られません。二軸引張試験によって、実験値に基づく最適な材料モデルの規定が可能です。最適な材料モデルを使うことでコンピュータシミュレーションの精度が向上します。また新しい材料モデルをつくるときの基礎データの収集にも役立ちます」
2008年、十字形試験片を用いた二軸引張試験方法は、経済産業省の「輸送機器の軽量化板材の二軸引張試験方法に関する標準化事業」に採択され、さらに2011年、「輸送機器用軽量化板材の二軸引張試験方法の国際標準化に関する調査研究」に継承された。桑原教授は、米国、欧州各国、韓国などとの連携をとりながら、同試験方法の国際標準化(ISO規格化)を進めている。
桑原教授は国際標準化に取り組むにあたり、ある測定装置を導入した。2つのカメラから三角測量によって対象物の変位とひずみを非接触で三次元的に測定できるARAMIS(アラミス)だ。
「十字形試験片を用いた二軸引張試験では、ひずみゲージ※を使ってひずみを測定することも可能です。ひずみゲージはひずみ測定の手段として広い分野で使用されていますが、対象物に直接貼り付けなければならず、応力の比率を変えるたびに何回も貼り替える手間がかかります。世界の多くの技術者に標準試験法として使ってもらうためには、簡便で、なおかつ精度が高くなければなりません」
※ひずみゲージ 目に見えない微小なひずみを、電気信号に置き換えるセンサ。
4日を要した試験もARAMISなら30分
取材時、桑原教授は海外のジャーナルに投稿した論文をプロジェクターに映し出してくれた。社会人ドクターである花房泰浩氏(ユニバーサル製缶)が、十字形試験片の応力測定精度を評価するために書いた論文だという。当初は計算結果だけを記載していたが、その妥当性を証明するデータの追加を求められたそうだ。
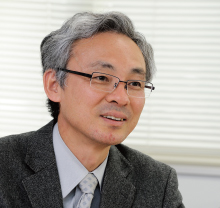
「急遽、ARAMISを使って測定し、ひずみ分布を可視化したのがこの画像です。カラーの画像が十字形試験片のひずみをARAMISで測定したもの、モノクロの画像が最適な材料モデルでシミュレーションを行った結果です。実験値と計算値がぴったり合っています。ARAMISのように高精度かつ非接触の測定装置がなければできなかった実験ですね。応力の測定誤差は2%未満であることも明らかにしました」
材料の変形特性を高精度に測定できる十字形試験片だが、応力を正確に測定するために入れたスリットの影響で腕部の強度が低下し、ひずみが数%に達したところで腕部が破断してしまうという課題があった。無駄のないものづくりのためには大きなひずみ範囲まで材料の変形挙動を予測することが必要となる。測定可能なひずみ範囲をより大きくするためにはどうしたらいいか。桑原教授が思いついたのは、金属の板を丸めて溶接した円管(パイプ)を試験片にするというアイデアだった。
「円管の両端を引っ張ることで軸方向の応力を発生させ、さらに円管内に液体を送り込み円管の内圧を高めることで円周方向の応力を発生させることができます。これらの応力を任意に変えることで、十字形試験片と同じようにX方向とY方向の応力の比率を自在に変更することが可能です。金属薄板が破断するまで、任意の応力比に対して応力-ひずみ曲線を測定できる試験方法は世界初です。液体でふくらませるだけなので摩擦の影響を考える必要もありません。この試験方法も国際標準化を進めています」
円管試験片を用いた新たな試験方法でも、当初はひずみゲージを利用していたが、10%程度のひずみではがれてしまうため、60%まで測定するには6回貼り替えなければならなかった。その結果、試験を完了するのに4日間を要したという。
「ARAMISを使えば30分で測定できる試験でした。現在、プロトタイプの段階ですが、学生を中心に円管試験片を用いた試験装置とARAMISを組み合わせたシステムを作成しました。ひずみゲージを使う必要はなく、CCDカメラを通じて測定するだけで、高張力鋼板やアルミ合金板のような軽量かつ難加工な板材を含むさまざまな材料の特性を測定することができます。非直線的な変形経路における材料の破断限界など、いままで見えなかったことが見えてくる。先進的な材料試験を行うときにARAMISは特に有効です」
創造的な発想は知的好奇心と情熱から
研究テーマと真っ直ぐに向き合い、柔軟な思考力で状況を打開する桑原教授は、学生に対してどのような指導者なのだろう。桑原教授が指導する桑原研究室は、学生の間でも研究指導が厳しいことで知られているという。だから本気で研究をやりたい学生が来てくれると桑原教授は話す。指導方針の基本は、研究目標を明確に示したうえで、あとは学生が主体的に研究を行うこと。また研究報告会での学生同士による徹底した議論も重視している。議論することで知恵を出し合うとともに、コミュニケーション能力も高められていく。また、国内の学会発表はもちろんのこと、できる限り国際会議に学生を連れて行き、海外の研究者の前で研究成果を発表する機会を与えているという。
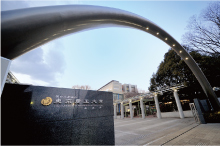
「日常英語もうまく話せなかった学生が、英語で研究発表を完璧にやりとげる。その成長した姿を見ているだけでうれしくなります。教育者冥利に尽きるというか」
研究者としての桑原教授は次の研究テーマを見据えている。「高温での多軸応力試験や金属以外の材料試験にも挑戦してみたいですね。それが次の幹となる研究テーマにつながっていくのではないかと思っています」
取材の最後にどうしても聞いてみたいことがあった。桑原教授の創造的な発想はどのようにして生まれてくるのだろう。「どうしても知りたいという強い思いがあれば、やるべきことは必然的に決まってきます」。知的好奇心と情熱が創造力の源なのだろう。
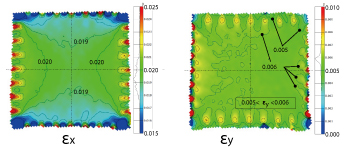
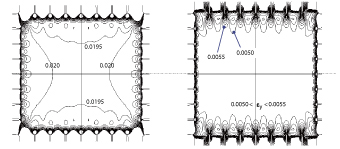