医療・介護用ベッドを製造・販売するシーホネンス株式会社。ベッドをつくり続けて半世紀以上、医療・介護用ベッド製造の歴史は36年を数える。「我々がつくるベッドは、一般のベッドと違って中に多くのメカニックな部品が入って複雑な構造をしております。安全性など国のガイドラインなどの影響も受け、時々刻々と対応していかなければなりません」(中野美喜男課長)
シーホネンスは次々と出てくる課題をどうクリアしていっているのだろうか。知られざる医療・介護用ベッドの世界を取材した。
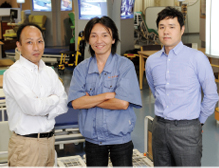
3つの機能がある医療・介護用ベッド
大阪市の東部に位置する東成区。周囲に工場が立ち並ぶ場所にシーホネンス本社があり、徒歩数分の場所にはショールームがある。そこに同社自慢の商品がズラリと並ぶ。そのほとんどが医療・介護用ベッドである。医療・介護用ベッドが一般ベッドともっとも異なっている点、それは『背上げ』『膝上げ』『床の高さ調整』などの機能が付いていることだ。
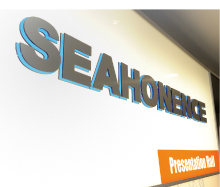
病気になったり年齢を重ねて身体が弱くなると、起き上がるのが困難になることがある。すると、食事を摂るのもままならず、咳などで呼吸が苦しいときも、上体を起こせないので呼吸困難になってしまう。人の手で起き上がらせるとなると、被介護者、介護者ともに負担が大きい。
そこで、被介護者、介護者の双方の負担を少しでも軽減しようと開発されたものが『医療・介護用ベッド』である。
手元にあるボタン1つで背上げによって起き上がることができるだけでなく、ベッドの高さも簡単に調節できる。車椅子などへの移乗もスムーズになり、介護される側、する側とも楽になる。また、膝上げ機能があることで足のむくみを軽減でき、背上げと膝上げを交互に行えば圧迫感を軽くすることもできる。
「医療・介護用ベッドは、病院や老人ホームなどの施設で使われる『医療用』と、在宅向けの『介護用』に分かれます。医療用は移動させたり複数の患者さんが使うため、堅牢性が求められます。一方介護用は、家の中に入れやすいように組み立て式になっているのが特徴です。ちなみに医療用は病院などの施設に直接卸しますが、介護用は福祉用具のレンタル会社に卸し、利用者はそこからレンタルして使うのが一般的です」(中野課長)
医療・介護用ベッドに求められるもの
シーホネンスは全国に支店や営業所があり、各地の様ざまな病院や介護施設に医療・介護用ベッドを提供している。「総合病院、大学病院、専門病院、救命救急などによって医療環境は様ざまです。当然、それぞれの環境に応じた機能や使いやすいベッドの仕様が求められます。また、部屋の雰囲気に合ったベッドにしてほしいといった要望も多く、カスタマイズは欠かせません」(中野課長)
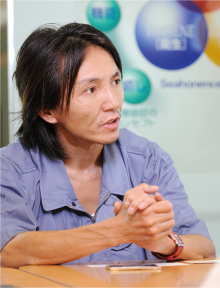
規格品も豊富に用意しているものの、今もって20~30%ほどがオーダーメイドというからその比率は高い。「ベッドに求められるものは『安全・安心』です」(中野課長)
シーホネンスが早くから取り組んでいたのが「安全性対策」だ。医療・介護用ベッドには転落防止のために柵があるが、ベッドを背上げする際、柵のすき間に手や足が入っているとはさまれて非常に危険な状態になる。それを防ぐには、柵とベッドが追従して一緒に動くようにすればいい。日本ではまだまだ認知度が低いものの諸外国では古くから一般的に普及しているものである。
国内でもすき間に対する製品安全を見直すべく2009年にJIS規格が改訂されたが、シーホネンスでは改訂以前からこの追従型を商品のラインナップに加えていたという。介護保険法が施行された2000年以降、医療・介護用ベッドの年間生産台数は34万台前後と「高いレベル」で推移。業界全体が活況を呈する。
ところが、2006年の介護保険法改正により、すべてが一変する──。
介護保険法改正で市場が半分に縮小
介護保険法改正。医療・介護用ベッド業界にとって致命的だったのは、「起き上がりや寝返りがまったくできない場合」にのみ自己負担額1割が適用され、手すりにつかまればなんとか起き上がれるような、やや症状の軽い人の場合は一切介護保険が適用されなくなったことだ。
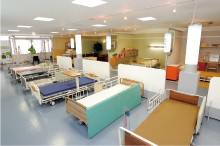
医療・介護用ベッドの利用者は大幅に減り、福祉用具レンタル会社の倉庫には使われなくなったベッドが山積みされていく。年間生産台数をみるとその激変ぶりがわかる。2005年、33.6万台だったものが、介護保険法が改正された2006年は21.9万台、2007年はさらに落ち込んで17.5万台と、2005年と比べると半分にまで縮小してしまう。他社に先駆けて高機能商品を提供してきたシーホネンスも、この市況の激変にはなす術がなかった。中野課長は当時を振り返る。
「まさに大打撃でした」
2008年19.5万台、2009年19.8万台とわずかに回復したものの、介護保険法改正前の60%にも満たない。2010年、シーホネンスはある改革を図る。
膨大だった外注費を一気にゼロへ
着手したのは、試作の外注費の削減だった。
「ベッドの構造は鉄パイプでできていますが、構造に関係ない箇所はプラスティックが使われることが多く、その部分の試作は削り出しで対応していました」(近本係長)
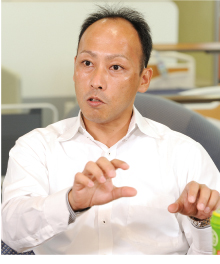
なかでも大きな割合を占めていたのがベッドの前後にあるヘッドフットボードと呼ばれる板状の部品だ。幅約1m、高さ約40cmほどもあるため、まず縮小サイズで試作モデルをつくって検討していき、ある程度の形ができ上がった時点で原寸大のモデルをつくる。その大きさゆえにコストがかさんでいたのだ。
「スピーディな商品開発が要求される中で時間もかかっていました。外注先に先約の仕事があると1、2週間経っても仕上がってこない。発注側からすると『なんでそんなにかかるのか』と思うこともたびたびでした」(中野課長)
毎年のように出ていく相当額の外注費。当然社員には次の思いが湧き出てくる。
『試作モデルを内製化できないだろうか』──。
中野課長の頭にあったのは3Dプリンター。資料を取り寄せ各メーカーの製品を比較。そのなかで選んだのは、ABS樹脂が使えて強度の高いモデルをつくることができる『Dimension(ディメンジョン)』だった。開発設計課のスタッフは使ってみてすぐに手ごたえを感じる。
「1、2週間かかっていたのが、翌日に3Dプリンターの扉を開けるとすでに完成している。センセーショナルでした」(中野課長)
導入後、試作にかかる外注費はゼロ。ランニングコストは電気代とカートリッジ代のみとなった。
「当初、初期投資をかけて元がとれるのかと思っていましたが、十分すぎるくらい元がとれていくのが実感できています」(中野課長)
近本係長が驚いたのは煩わしさが減ったことだ。
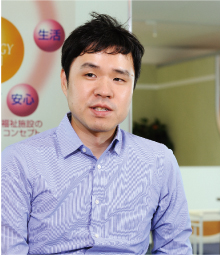
「外注に出していたころは、外注先に3Dデータを送るといった手間がかかっていましたが、それが一切なくなった。本当に楽になりました」また、「低床ベッド」の設計でも3Dプリンターで造形した機構部品のモックアップを使い、配置や組み付け方法を検討することで、被介護者にやさしい低床ベッド作りに役立てようともしている。
プレゼンツールで売上拡大もめざす
「今、3Dプリンターを使って売上拡大が図れないかと考えています」(中嶋健次氏)そのために開発設計課がめざしたのは「プレゼンツール」の製作だった。
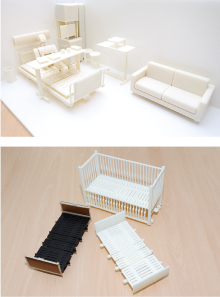
「ベッドだけでなく周辺のキャビネットなども製造し、部屋全体をセットで提案してみようと思っています。その際に、カタログだけではどうしてもイメージが伝わり切らずインパクトも弱い。そこでミニチュア版のベッドやキャビネットなどを3Dプリンターで造形し、それを簡易的につくったミニチュアの部屋に配置すれば、より具体的なイメージが湧いてお客様の心象もよくなるはずです。将来的にはこれらをセットにして、営業マン全員に渡すことを考えています」(中嶋氏)
前述のヘッドフットボードは様ざまな色や形があるため、それを1つずつ3Dプリンターで造形し、訪問した病院などで1つひとつ付けて見せることも考えているという。
ベッドだけでなく周辺商品の製造も視野に入れるなど、次々とアイデアが生まれているシーホネンス。10年後、20年後、そんな驚くような変身を遂げているかもしれない。
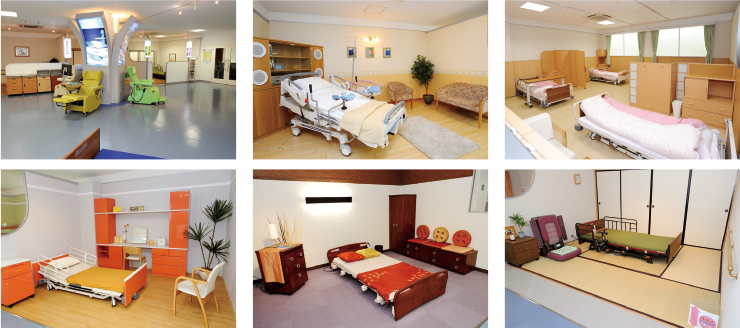