ビジネスにはさまざまな勝負がある。価格で勝負するのか、スピードで勝負するのか、あるいはクオリティで勝負するのか。戦略は企業によってまちまちだ。
「当社はお客さまからの信頼を得られるよう、高品質で均一な製品とサービスを提供することに力を入れています」山洋電気の池田智昭部長はそう力強く語る。「簡単に壊れてしまったり本来の性能が出なかったりしたら、
信頼を得ることはできません。そうしたことを一つひとつきちんとクリアしてこそ、高い信頼性と評価につながっていくと考えています」ハイクオリティを日々追い求める山洋電気。キーワードは、「無限の可能性」だった。
我々の現在の生活になくてはならないファン
その光景を見ると、誰しもここが盆地であることを悟るだろう。周りを2000m級の山々に囲まれ広い平地が広がる。中央に悠々と流れるのは千曲川。新潟県に入ると「信濃川」と呼ばれる川だ。ここは上田盆地。長野県上田市がすっぽりと入る広大な盆地である。山洋電気グループは、日本をはじめ世界に拠点を有するグローバル企業である。上田市には製品の生産拠点のほか、研究・開発拠点であるテクノロジーセンターを構え、フィリピンにも巨大な生産拠点がある。
「当社の製品は大きく3つのカテゴリに分類されます。一つは、無瞬断で電源をバックアップする無停電電源装置(UPS)や太陽光発電システム用パワーコンディショナなどの電源システムです。もう一つは、多関節ロボットや工作機械、監視カメラなどに採用されているサーボシステムやステッピングシステム。そして、装置の冷却や空気循環など使用されるファンです。我々は、このファンの開発と設計をおこなっています」(池田氏)
私たちに身近なものでファンが使用されている機器と言えばパソコンだろう。パソコンには、発熱するCPUを冷却するためにファンが組み込まれている。もしファンがなければ、CPUはオーバーヒートを起こして機能不全に陥るか、そこまでいかなくても寿命が大幅に短くなってしまう。多くの熱を出すことで知られるサーバもしかりである。コンピューター社会を支えるパソコンやサーバに、ファンはなくてはならないものだ。山洋電気は、かつてインテルのCPUクーラーをほぼ一手に引き受けていた企業でもある。
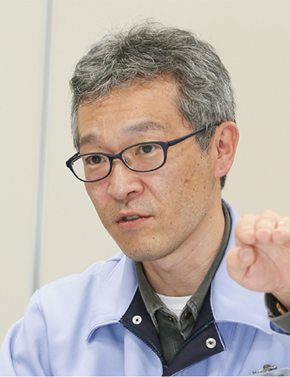
「自動販売機にもファンは多く使われています。全画面液晶パネルは電気使用量が多く発熱量も大きいので、高い冷却性能のファンが欠かせません。冷気を循環させて飲み物を冷却するためにもファンが必要です。また、両方向に送風ができるリバーシブルフローファンは、印刷機や食品用ショーケース、住宅などの用途にご使用いただいています」ファンはモーター、フレーム、羽根に大きく分かれ、山洋電気ではそのすべてをオリジナルで設計している。モーターなどは回路設計になるが、池田氏、柳沢氏、奥田氏が担当しているのは流体的な性能に関わるフレームや羽根の形を決める構造設計である。
「羽根は一見シンプルな形をしていますが、実は非常に奥深い世界なのです」(池田氏)
ずっと追い続けているもの
ファンの羽根の形は、パソコン用やサーバ用、自動販売機用などの用途によって基本の形が変わるものではない。扇風機のような羽根があり、それを回すことで風を起こすという原理は同じだ。
「基本形は変わりませんが、用途によって求められる特性がかなり変わってきます。たとえば、音響の現場で使われる製品の場合、余計な雑音が入ってはいけませんから、限りなく音が出ないように設計をしなくてはなりません。また、自動販売機用のファンであれば、多少の音がしても問題にならない一方で、屋外に設置されて外気温にさらされるため、暑さや寒さにも耐えられるよう耐久性のあるファンを設計する必要があります。このように、一見同じように見えるファンも、用途に応じて求められる性能は変わってきます。ファンの性能として主なものを挙げると、風量、静圧、消費電力、音ですね」(池田氏)
たとえば音を小さくしたい場合、羽根を大型化して回転数を落としていけば音は小さくなる。だが、当然ながら限りなく羽根を大きくできるわけではなく、限られたサイズの中に収めなければならない。さらにあまりゆっくり回していたのでは風量が落ち、肝心の冷却能力も下がってしまう。こうしたさまざまな制約のなかでいかに市場が要求する性能を出せるかが、設計部の腕の見せ所となる。そして、さらに乗り越えなければならない壁がある。ファン業界は「非常に競争が激しい」(池田氏)ため、他社との競争に勝たなければならない。
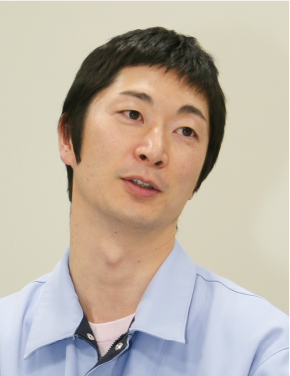
「競合企業は国内外に複数あります。こうした他社と競合したときに重要なのは“どこで勝負するのか”です。価格なのか、スピードなのか。当社がずっと追い求め続けてきたのは『山洋電気は業界トップの性能をもつ製品をつくる』という高信頼かつ高品質の製品づくりです。当社は長い間この勝負に全力を尽くしてきました」
2007年、山洋電気はハイクオリティの製品づくりをさらに強固なものにしていくため、新たな手を打つ。
ハイクオリティの源泉である試作に生まれた危機
「15年以上前に、それまでの2次元図面から3D CADを導入し切り替えました。クオリティを保つためには、目標となる数値をクリアしているのかをきちんと評価することが欠かせません。その方法の一つにシミュレーションソフトがありますが、これは100%ではなく、性能の大まかな方向性は把握できても細かな性能を正確に評価することができません。性能評価にはどうしても試作品が欠かせませんでした」
山洋電気にとって、試作品はハイクオリティの製品づくりの大きなカギとなっていたのだ。「試作品はすべて外注に頼っていました。3Dデータの無い頃の試作品は2次元図面を外注に渡し、木材の塊を切削により製作してもらっていました。3Dデータを利用するようになると、樹脂を切削加工したものや光硬化樹脂による試作品を製作してもらうようになりました」
長い間この体制が続いていたが、いくつか悩みがあった。一つは時間がかかること。依頼をして納品されるまでに3、4日から1週間、大きいものになると2週間かかることもあった。依頼先が少し遠かったこともあり輸送時間もかかる。修正が入り再度依頼するとなると、さらに時間を要してコストも膨らんだ。
「これは設計者を畏縮させることにもつながっていました。設計者は性能を出すためにさまざまなことを試したいものです。ところが、一度依頼すると5万円や10万円もかかってしまう。1個や2個ならまだしも、10個以上の試作品を製作したいとはさすがに言い出しにくいこともありました。」(池田氏)
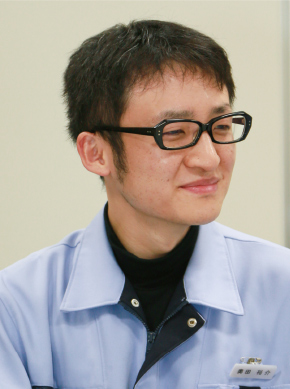
柳沢氏もこう語る。「すべてを外注することができないので、さまざまなアイデアを並べたうえで、あまり突拍子もないアイデアは外し、これであれば性能を達成できるというものだけを試作していました」
そして、転換を図る大きなきっかけとなったのが、試作のスケジュールが重なってしまうことだった。「開発する商品は一つだけではありません。さまざまな製品が一度に同時進行しているため、どうしてもスケジュールが重なってしまう。そうなるとちょっとしたマイナーチェンジの時間をとれないものが出てきてしまいます。羽根というのは本当にごくわずか形を変えるだけで性能が大きく変わるものです。常に高い性能を追い求めている当社にとって、それができないというのは致命的なことでした」
山洋電気は、現状の打破を試みる。
「形」にすることで見えてくる無限の可能性
2007年11月、3Dプリンターを導入する。2007年といえば、3Dプリンターは黎明期であった。
「まず圧倒的に試作期間が短くなりました。それまで試作品の評価をするまで1~2週間かかっていたのが、わずか一晩で製作できるようになり、それが今までと大きな違いでした」(奥田氏)
そして3Dプリンターの導入は、何より設計者の心に火を点けることになる。「それまでは、様々なアイデアがあっても試すことができたのはそのうち一部だけでした。それが3Dプリンター導入によって、ほとんどすべてを試すことができるようになったのです」(柳沢氏)
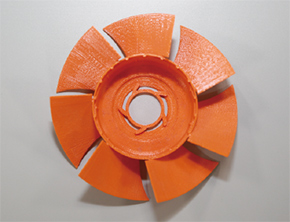
開発期間の短縮が品質の向上につながっている、と池田氏は言う。「早く開発を終わらせることもできますが、当社では常に『その時点での最高性能を出す』といった目標を掲げているため、『これですべてアイデアは出し尽くしたのか』という問いかけが必ずあります。少しでもチャレンジできることがあるなら全部やり尽くそう、とさらに改良を重ねることができるため、従来と開発期間は変わらなくても、明らかに性能が良くなりました」
また、グループ会社であるSANYO DENKI PHILIPPINES, INC.にも設計部があり、今までは手掛けた3Dデータを日本の3Dプリンターで造形、フィリピンに空輸していた。しかし、フィリピンの設計部での試作が増えたことから、2013年9月に同じ3Dプリンターを導入した。日本での購入元である丸紅情報システムズと同じ丸紅グループのMarubeni Software & Technology (Thailand)Co., Ltd.(略称:MSTT)から購入し、メンテナンスサポートも任せている。
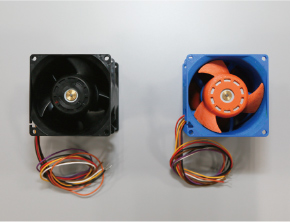
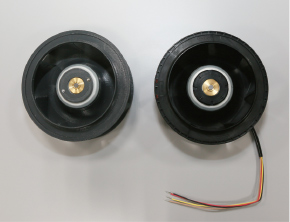
柳沢氏は3Dプリンター導入後の現場をこう語る。「これまでは、先輩たちの経験値から『こういうものはうまくいかない』とされたアイデアには、チャレンジしてきませんでした。しかし、3Dプリンター導入後は手軽に試作ができるようになったので、思いついたアイデアをみんな形にできるようになりました。多くはないですが、思いついたアイデアで製作したものが想像以上の結果を出したこともありました」
それまでのファンは5~7枚羽根が主流であったが、試しに3枚羽根にしてみたところ、狙った性能が出たという。
「3枚だと見た目は本当にスカスカです。ところが試作品を製作してみると、結果は従来品を上回ったのです。経験値だけでなく、一見突拍子もないアイデアでも挑戦してみることが重要なのだと改めて感じました」(奥田氏)
ファン業界の熾烈な競争は今もって続いており、競合他社も負けじと次々に新製品を出してくる。しかし、設計部3名の決意は固い。「一見ファンと関係ないような分野にも興味を持つなど、広い視野でさまざまヒントを探しながら、さらに高品質の製品を開発していきます」
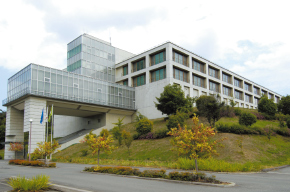
今、無限の可能性を実現している山洋電気の設計者。さらなるハイクオリティな製品を追い求め、今日も戦っている。