1946(昭和21)年に個人会社として創業して以来、義肢装具に用いる部品類や、それに関わる機械工具類などの開発や製造・供給を事業として展開してきた株式会社小原工業(以下、小原工業)。今日では、義肢装具総合メーカーとして、海外からも高く評価されている。
義肢装具に用いる部品類は量産に適さないものも多い。全国にある義肢製作所からの依頼に応じて、個別性の高い部品類を製作する小原工業では、より生産性を高めるために金属3Dプリンターの活用は必須であった。
しかし、金属3Dプリンターの導入にあたって、クリアすべき条件もあり、簡単に導入できるものではなかった。そんな中で出合ったのが、丸紅情報システムズ株式会社(以下、MSYS)が扱っているDesktop Metal社製の金属3Dプリンター「Studioシステム2」である。
複数の金属3Dプリンターを比較検討して「Studioシステム2」を選定するに至った経緯や導入後の活用シーン、その効果について、小原工業の取締役 最高執行責任者 秋山重幸氏に話を聞いた。
- 形状試作だけでなく、実用可能なパーツの製造を実現したい
- 量産に向かない多種多様な義肢装具のパーツや、義肢製作所で使用する機械工具の部品などにも対応したい
■金属3Dプリンター導入の背景
1. 個別性の高い義肢パーツや、義肢製作のための機械工具の部品などが主要製品
小原工業の創業者である小原正次郎氏が、厚生労働省(当時の厚生省)の研究機関から要請を受けて義足の部品を製作したことを契機に、義肢装具総合メーカーとしての小原工業がスタートした。
その後、事業は成長・発展し、今日では、全国に数百社ともいわれる義肢製作所に、義肢装具関連の部品を供給することに加えて、義肢の製作に必要な機械工具の部品も依頼に応じて製造、提供している。
義肢製作所では、義肢装具士という国家資格をもつ専門家が、義肢装具の採型・製作・調整などを行っている。義肢装具という製品の特性上、使用者のニーズに応じたオーダーメイドの義肢も多く、金型による量産が適さない部品も多々ある。 「本当に多種多様なパーツがあります。それぞれの義肢製作所から、“こういう部品がほしい”という要請を受けて当社で製作します。要請の中には、義肢装具に共通するようなパーツではない、個別性の高いものが多くあります。そのため、まずは樹脂の3Dプリンターで試作品をつくり、形状やパーツによっては他のパーツとの嵌合具合なども確認して、問題ない段階で、実製品を製造するというプロセスを踏んでいました。しかし、試作段階で問題がなく、実生産したものの、微妙に嵌合部分に不具合が生じて、つくり直すということもありました。そこで、最初から実用部品として使えるように、金属3Dプリンターで対応したいと考えるようになりました」と秋山氏は、樹脂の3Dプリンターを使用していた当時の大変さを振り返る。
2. 金属3Dプリンター導入のための条件
以前から、金属3Dプリンターの導入は検討していたものの、実際の導入には、いくつかクリアすべき条件もあり、簡単に決定できるものではなかったという。
「パウダーベッド方式の金属3Dプリンターを検討したこともありました。しかし、当社で使うには規模が大きくなり過ぎるため断念しました。また、FDM(Fused Deposition Modeling=熱溶解積層方式)方式も検討しました。しかし、こちらはバインダーを除去するために有機溶剤を使用する脱脂装置が必要になるため、そうした環境を工場内に用意するのが難しく、導入できませんでした。 こうした検討を続けている時に、MSYSが提案するDesktop Metal社の『Studioシステム2』に出合いました」とのことだった。
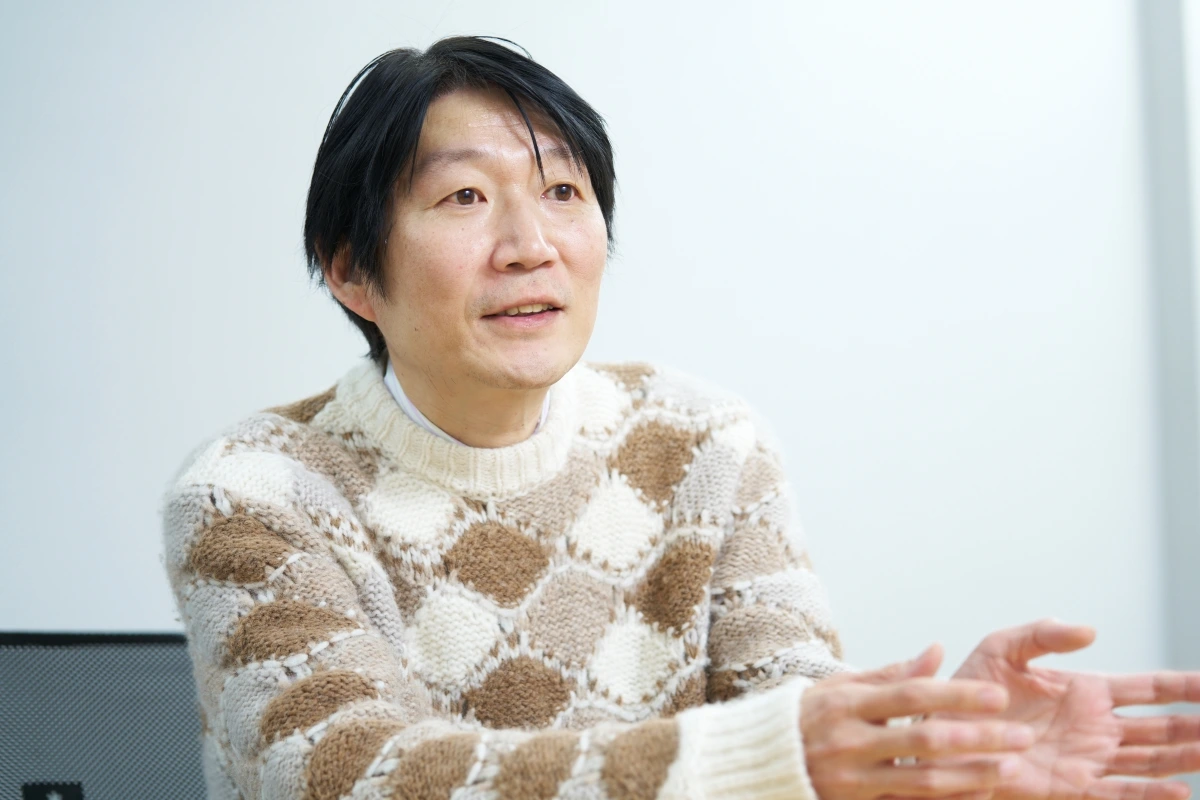
■金属3Dプリンターの導入プロセスと、その後の活用
3. 複数の金属3Dプリンターを比較検討して、Desktop Metal社の「Studioシステム2」を選択
「Studioシステム2」の導入を決定する前段階では、他社のレーザレーザ方式の金属3Dプリンターも検討したという。ただ、レーザ方式金属3Dプリンターの場合は、造形後に土台と造形物を切り離すためのワイヤーカットという後加工の工程が必要になり、そのための機材がない小原工業では、外注が必要になってしまう。
「後加工の工程が必要になると使い勝手は悪くなります。また、実際のデータを使って試作も行ったのですが、レーザ方式の場合、『Studioシステム2』に比べると表面の仕上がりが少し粗いという点も気になりました。こうした検討を経て、最終的に『Studioシステム2』を選定しました」と、決定までの経緯を説明してくれた。
4. 樹脂の3Dプリンターを活用してきた経験を活かし、円滑な活用が実現
「Studioシステム2」を導入するにあたっては、ちょっとした問題も発生したという。
「金属3Dプリンターそのものの問題ではないのですが、『Studioシステム2』が電気炉を使用するため、消防法上の問題があるのではないかと最寄りの消防署に指摘を受けました。指摘通りとなれば、電気炉を囲う壁の設置や隔離するなどの措置が必要になってしまいます。少々慌てましたが、改めて消防庁に確認したところ、法律の趣旨に照らして問題なしと判断が下ったため、支障なく使えることになりました。
実際に導入してからは、問題なく円滑に活用できています。比較的新しい製品なので、ちょっとした不具合の発生や、ソフトウェアのバージョンアップが必要になることもあります。しかし、その都度、MSYSが迅速に対応してくれるので、問題なく活用できています」と、導入後のMSYSのサポートにも満足げだ。
「Studioシステム2」で製造した部品は、そのまま実用することができるレベルで、実際に人体につけてもらっても問題がないという。
また義肢装具の部品だけでなく、義肢製作所で使用している機械工具の部品が欠損してしまったような場合にも、「Studioシステム2」で製造し、供給している。 「義肢製作所で使用している機械工具メーカーがなくなってしまい、一部のパーツが欠損しているので、その部品を作ってほしいというオーダーも多々あります。多くの場合、摩耗が原因なので、当該のパーツを基にして、ノギスで計測するなどして3Dデータを起こします。そして、そのデータを使って『Studioシステム2』で製造します」というように、機械工具の部品製造にも「Studioシステム2」は役立っている。
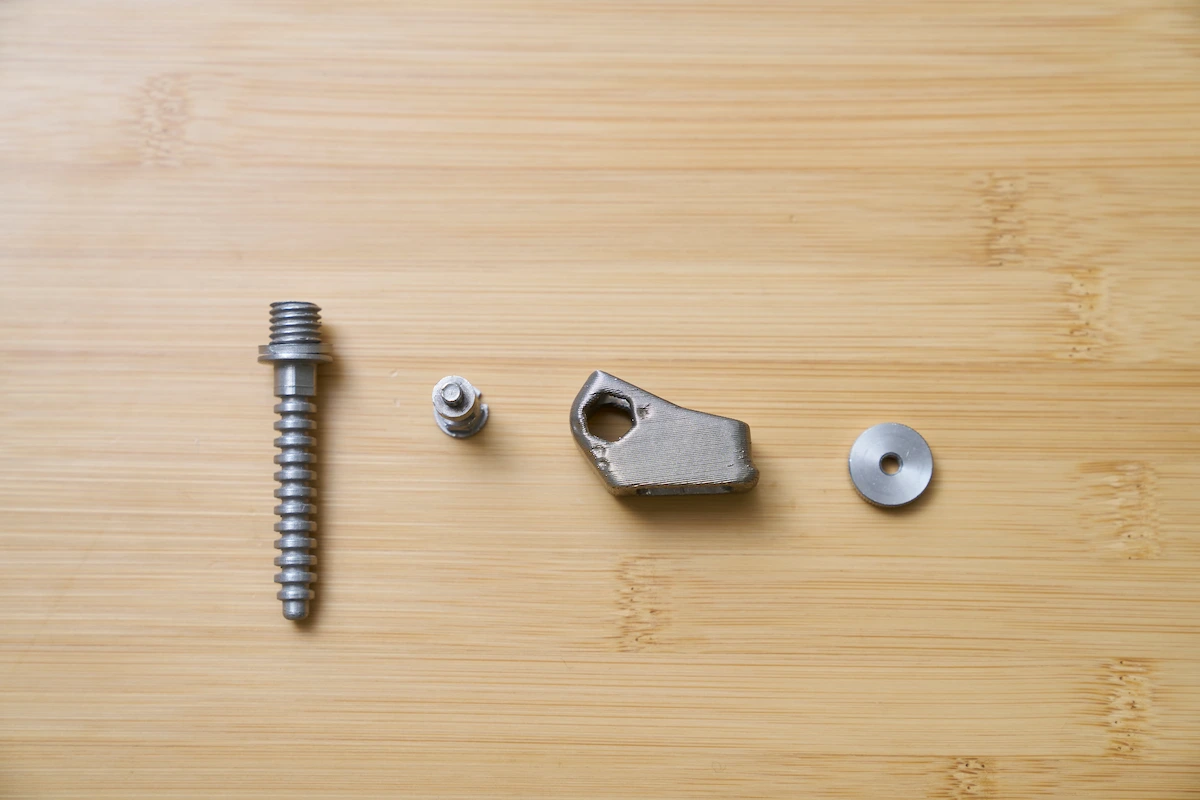
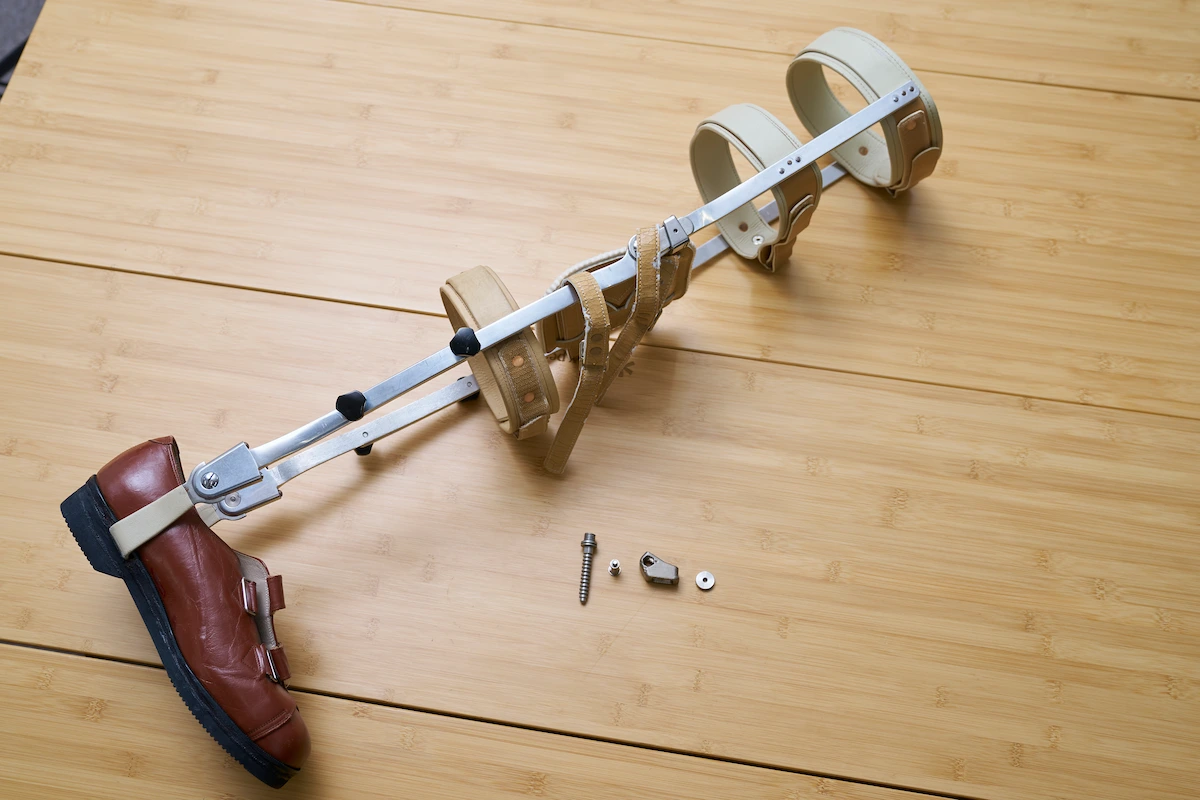
■金属3Dプリンターの導入効果と、今後のさらなる活用
5. 金型不要の金属3Dプリンター「Studioシステム2」で大幅なコスト削減を実現
樹脂の3Dプリンターを使っていた当時は、試作を行い、形状を確認してから実用部品を製造していた。当時、万が一の不具合の発生を想定して、30個必要であるところをまず10個だけつくってみるという手順を踏んでいたという。
「しかし、『Studioシステム2』は、比較的安定した品質で、安心して必要な数をつくることができます。その点はとても助かっています」と評価する。
そして、最大の成果はコスト面だという。小原工業では、簡単な形状のものは、ワックスで模型をつくり、模型をベースに鋳型を作成して金属を流し込むロストワックスなども活用している。しかし、ロストワックスでは複雑な形状のものの製造は難しい。このようなケースでは、MIM(Metal Injection Molding=金属射出成形法)を活用することもあるという。 「MIMで製造すると、ロストワックスと比較して約10倍のコストがかかります。しかし、金属3Dプリンターを導入してからは、複雑な形状のものであっても、簡単に、そしてスピーディにつくることができます。金属3Dプリンターの導入効果は、効率的にものづくりができることもそうですが、当社の場合にはコストメリットも大きいですね。」と、コストメリットが大きいことも導入効果のひとつに挙げる。
6. 義肢装具だけではない、幅広い活用分野に期待
小原工業における金属3Dプリンター「Studioシステム2」活用の多くは、義肢装具や義肢装具製造のための機械工具の部品製造などが中心である。しかし今後は、より幅広い活用を考えているそうだ。
「義肢装具関連の用途だけでは、もったいないと考えています。『Studioシステム2』自体が非常に使い勝手がよいという利点があります。STLデータさえあれば、義肢装具関連以外のものにも活用可能です。そこで、ネットを通じて、義肢装具関連以外の試作品製作などを呼びかけたところ、さまざまな依頼がくるようになりました。
最近では、鉄道模型のパーツをつくってほしいという依頼もきています。実際に走行する鉄道模型は、モーターを動かすことで熱が発生するために、樹脂の部品では耐えられないそうです。そこで、金属3Dプリンターを使った金属製部品の製作が依頼されたわけです」と秋山氏。
樹脂を使う3Dプリンターが広く普及したことで、3Dプリンターの利用層は着実に増えている。一方で、樹脂では活用の幅に限界があり、「金属3Dプリンターでつくりたい」というニーズは、さまざまな分野に広がっていると秋山氏は考えている。
「当社のSNSのフォロワーの中にも、3Dプリンターのユーザが多数います。こうしたユーザを中心に、強度が求められるパーツなどは金属3Dプリンターで、と考える方が少なくありません。さまざまなニーズを拾い上げながら、もっと活用分野を拡大していきたいですね」と、さらなる活用領域の拡大に意欲をみせる。 義肢装具の総合メーカーとして、金属3Dプリンターを有効活用する小原工業だが、今後はより多くの可能性に向けて、さまざまな取り組みを加速していくことだろう。