多様な用途で利用されるシーンが増えている金属3Dプリンター。導入したいと考える企業は増えていますが、その一方で、導入にかかるコストが、導入によって得られる利益できちんと回収できるかどうかが分からず、導入をためらうケースも少なくありません。
本稿では、海外の先進的な金属3Dプリンタの事例を通して、金属3Dプリンタの導入効果について紹介します。また、導入のしやすさに定評のあるDesktop Metal社製の金属3Dプリンタの特徴についても紹介します。
Desktop Metal社製 金属3Dプリンターの特徴
丸紅情報システムズが取り扱っているアメリカのDesktop Metal社の金属3Dプリンターは、2つの造形方式を採用しています。
導入・運用がしやすいBMD方式の「Studioシステム2」
ひとつはBMD方式です。導入しやすく、運用しやすいといった特徴があります。製品は「Studioシステム2」で、造形、焼結の2ステップで金属部品をつくることができ、対応材料についてもステンレス鋼や工具鋼、ニッケル合金が使えるなど幅広いという点も特徴のひとつです。
より生産性が高いバインダージェット方式の「Shopシステム」や「Xシリーズ」、「Productionシステム」
もうひとつの造形方式であるバインダージェット方式は、金属粉末をローラーで敷き詰め、そこにバインダーと呼ばれる結合剤をインクジェットで出力して積層造形していくというもので、生産性の高さに特徴があります。造形したモデルをまとめて焼結して金属部品が完成します。
この造形方式の製品としては「Shopシステム」と「Xシリーズ」、「Productionシステム」などが代表的です。「Shopシステム」は使用できる金属材料ごとにパラメータを調整済みなので、ユーザー側でパラメータを調整したり、試行錯誤したりする手間が不要です。また、前後工程も含めて設備が一式セットになっているので、導入後すぐに利用することができます。一方で「Xシリーズ」や「Productionシステム」は、オープン材料設計となっており、ユーザー側が独自の材料で造形することも可能となります。
このように、用途に応じた多種多様な製品をラインナップしており、さまざまなニーズに対応できる製品バリエーションの豊富さも特徴のひとつです。なお、高額で危険なレーザーを使用しないという点が全機種共通の特徴となっています。
最新の海外導入事例紹介
Desktop Metal社の金属3Dプリンターは、世界中で、さまざまな企業で導入・活用されています。ここでは、いくつかの導入事例を紹介します。
土木業界における導入事例
アメリカで土木建機を開発・製造しているC.J. Moyna & Sons社では、新型コロナの世界的規模のパンデミックによって、部品調達のサプライチェーンに支障が生じ、必要な部品の一部が入手困難になる経験をしました。それを契機に金属3Dプリンターの導入が検討され、「R&D試作の高速化」「製品改善」「古い部品の復刻生産」の3つの目的において、金属3Dプリンターが有効であろうと判断し、導入を決定しました。
「Shopシステム」を採用した決め手は、操作性の良さだったといいます。6つのメーカーの製品を比較検討したところ、「Shopシステム」はファイルの準備から造形のセットアップまでソフトウェアが順を追ってガイドしてくれるというワークフローが備わっており、そのわかりやすさが魅力でした。
また該社では、まず樹脂3Dプリンターを使ってスピーディーに形状の検討を進め、それから金属3Dプリンターで実製造するという製品改善プロセスを確立しました。設計に課題があったシートラッチにおいては、樹脂3Dプリンターで設計の検証を行い、検証が済んだ後に「Shopシステム」で最終的な改善版の製品を3Dプリントすることで、従来の製造方法で半年以上要したものが、1週間程度に短縮できたそうです。
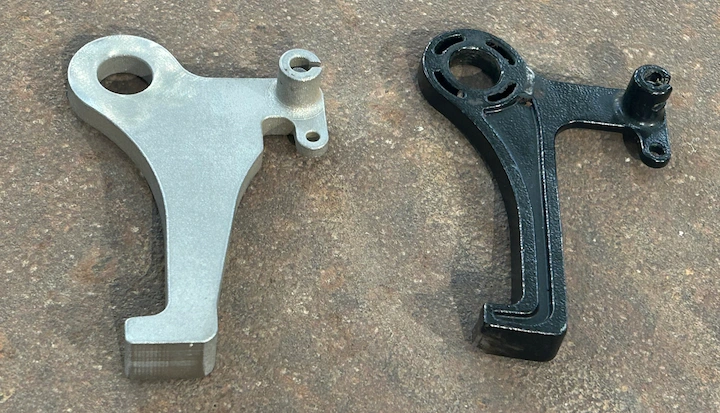
さらに古い機器の修復においては、交換部品が手に入りにくいという問題を抱えていましたが、当該の部品を3Dスキャンし、リバースエンジニアリングすることによって必要な交換部品を入手できるようになりました。
食品加工機械メーカーの導入事例
アイスランドで食品加工機械を製造・販売しているCurio社では、以前から3Dプリンターに注目しており、2010年頃にはFDM方式の樹脂3Dプリンターを導入し、試作業務に活用していました。
製品製造ということに関しては金属、特にステンレスでの3Dプリントに強い関心があり、レーザー方式の金属3Dプリンターに注目していました。しかし、レーザー方式は高価である上、後加工も面倒であるというところから導入に躊躇していました。そこで関心を寄せたのが、デスクトップメタル社の「Studioシステム2」でした。
BMD方式の「Studioシステム2」は、固形材料を使用するため、オフィス内でも使いやすいという特徴があり、該社ではまず2台導入し、運用をスタートしました。食品加工機械は小さな部品が非常に多く使われており、また耐熱・耐水性、耐久性や耐腐食性に加えて、消毒容易性などが求められます。「Studioシステム2」では、316Lというステンレス鋼が使えることから、こうした要求を満たす上で理想的であると評価されました。また、「Studioシステム2」を導入したことによって、迅速な設計の反復と最適化というメリットが享受できました。従来の型を使った部品製造では細かい設計変更が難しいという側面がありましたが、そうした部品でも「Studioシステム2」なら、型が不要であるために継続的なカスタマイズも可能で、製品の品質向上にもつながります。そして、それは最終的にはユーザー体験の向上につながると評価されています。
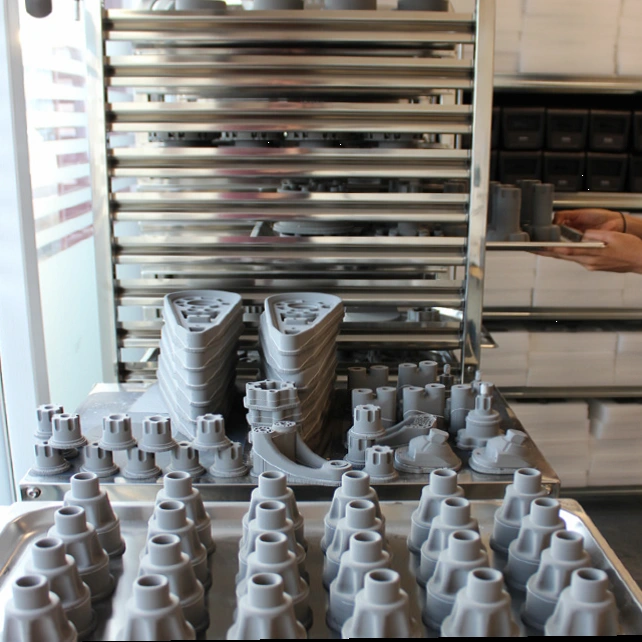
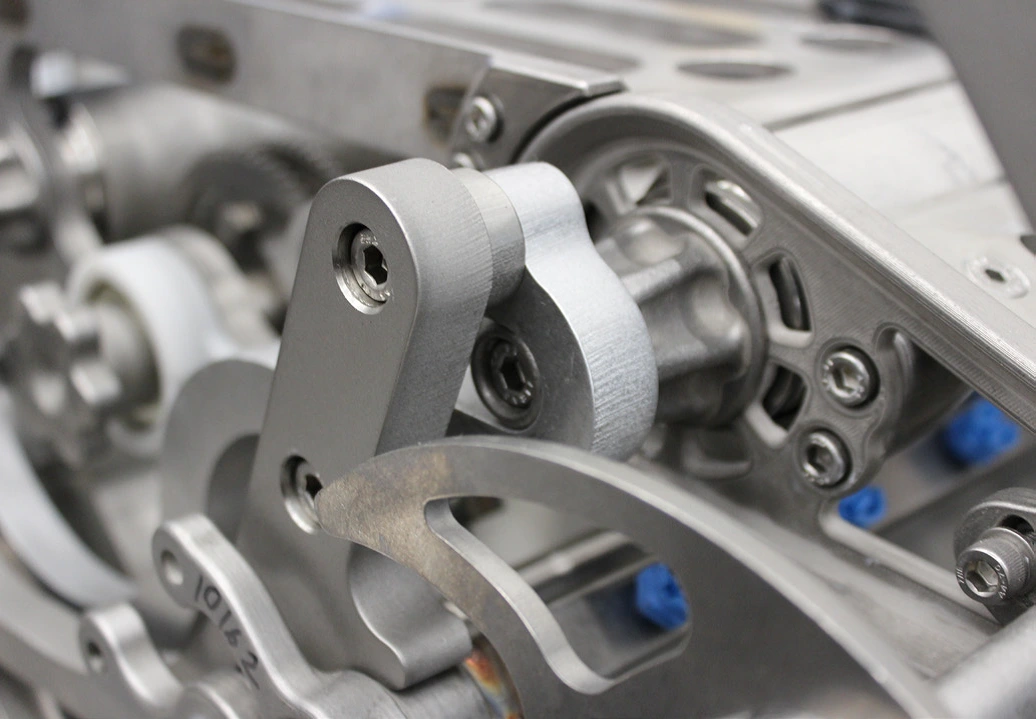
搭載された最新設備
該社ではこうした金属3Dプリンターのメリットを高く評価し、さらに2台の「Studioシステム2」を導入し、現在では24時間体制で4台の「Studioシステム2」を活用しています。これにより、製品の供給がスピーディーになり、また製品開発にかかる期間も従来に比べて1年ほども短縮できたといいます。さらに、これまで海外調達していた部品などの中には発注から納品まで1年ほどを要したものもありましたが、「Studioシステム2」の導入によって、数週間で製造することが可能となりました。
産業用燃焼機器メーカーの導入事例
John Zink Hamworthy Combustion社は、アメリカで産業用の燃焼機器を製造するメーカーです。発電所から乗用車まで、さまざまなシーンで使用される燃焼機器は、環境意識の高まりを受け、CO2排出規制の厳格化が進んでいます。その一方で、コスト抑制が求められるため、技術革新との両立が大きな課題となっています。そこで該社では、各顧客のニーズに合わせてカスタマイズすることで、この課題に対応しようと考え、金属3Dプリンター「Studioシステム2」を導入しました。
前の事例と同様に、「Studioシステム2」の特徴であるオフィスフレンドリーなデザインが評価されたことはもちろん、金属粉末や危険なレーザーを使用しないために、運用時に厳重な保護具を使うといった手間がないことも大きな評価ポイントでした。設備投資という点でも、金属粉末をレーザーで焼結させるタイプのものだと、設備本体に加えて環境整備費用などを含めて1億円超が必要になることもあります。しかし「Studioシステム2」なら、導入コストはその半分程度という点も高く評価されました。
「Studioシステム2」を活用することで設計の自由度が向上するため、排出規制などの環境基準を満たしながら、機能性も向上させることが可能になりました。たとえば、燃料アトマイザーをAM最適化設計に変更することで、バーナー内の燃料と空気の混合割合を改善でき、消費燃料の削減につながり、その分の燃料コストも削減できます。ある顧客のLNG(液化天然ガス)タンカーでは、年間の燃料費が1400~2500万円ほどの削減につながりました。またレーザー方式と比べて、製造コストは4分の1、納期は3分の1ほどに抑えることができました。
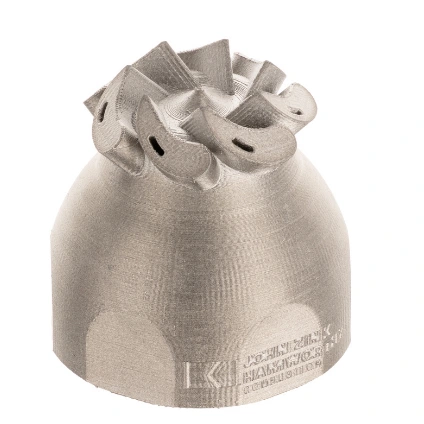
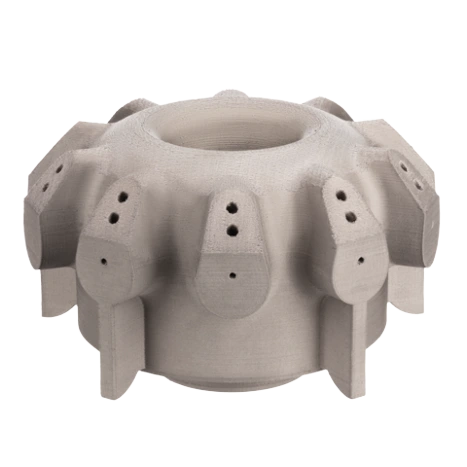
さらに、製品の中にはバーナーチップのように非常に古い部品が使われていることがあり、部品によっては金型がすでになくなっていることもあり、再製造が難しいという問題もありました。そこで、元の設計図面から3Dモデリングし、そのデータから3Dプリントすることで再製造を可能にしました。納期も大幅に短縮され、金型が不要となることからコスト面でも数百万円の削減につながりました。
金属3Dプリンターの導入における、越えるべきハードルについて
取り上げた事例のように、金属3Dプリンターの効果・効用は数多くあります。しかしそれでも、導入を躊躇してしまうハードルがあるのも事実です。代表的なものが「導入コスト」と「安全性」です。
導入コスト
金属3Dプリンターの導入を検討するにあたって、やはり大きなハードルのひとつは導入コストです。場合によっては1億円以上の投資が必要となる場合もあり、費用対効果について、しっかりした試算などを行い、投資に見合う効果が期待できるのかどうかは見極める必要があります。
また、コストを検討する上で注意を要するのが、単に設備本体のコストだけでなく、製品によって、それを運用するための環境整備が必要になるケースもあるという点です。これは、次のハードルである安全面とも関連しますが、導入する金属3Dプリンターの製品によっては、安全対策に必要な措置を講じるために一定の費用がかかるので、その分も加味した投資計画と、費用対効果を検討する必要があります。
安全性
金属粉末を使うこと、あるいは高出力のレーザーを使うことに起因する安全面のリスクについては、十分な対策の検討が必要であり、場合によっては有機溶剤を使用するケースもあるので、安全対策も不可欠になります。危険を伴う作業になるような場合には、専門資格の事前取得や重装備の保護具などを用意することも必要になります。
金属3Dプリンターの活用メリットは理解できても、費用対効果や安全面のリスクについて、きちんとした評価が必要になります。そうした評価は、導入の目的や使用頻度、期待効果など、各企業の事情に依存します。
ただ、金属3Dプリンターを導入した企業などから、導入前に想定した効果以上の、予想外の効果があったと評価されるケースも少なくありません。あくまでも既存の製品部品の製造用に導入したのに、新製品開発にも効果を発揮した、というような事例もあります。新しい取り組み、新しい技術の導入は、競合他社に対して一歩、ないし半歩先行するための施策になり得ます。状況が許すなら、積極的に導入するメリットはありそうです。
粉末・レーザー・溶剤レスを実現した金属3Dプリンター Studioシステム2について
当社が取り扱っているDesktop Metal社の「Studioシステム2」などは、前述のような導入のハードルになりがちなコスト面・安全面の懸念を軽減できるポテンシャルのある製品だといえます。操作性にも優れており、金属3Dプリンターを導入したいけれど、できるだけ面倒な手間はかけたくないという場合には、非常にメリットの大きい金属3Dプリンターです。造形して焼結するだけ、というシンプルな工程で使うことができます。
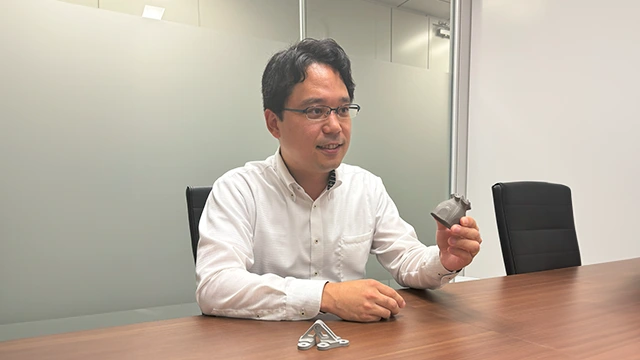
また金属粉末ではなく、スティック形状の固形材料を使うという点も手軽に使えるポイントです。使用可能な材料は9種類あり、カートリッジタイプなので、「今日はステンレス鋼を使い、明日は工具鋼を使う」というような材料の切り替えも極めて容易です。金属粉末の場合は使用後の清掃なども手間ですが、カートリッジタイプなので、そうした手間も少ないです。また固形材料を使うことによって、外側は閉じていても、内部を中空にして造形することが可能になっています。よって、形状を保ったまま軽量化することが可能です。使用する材料の量も少なく済み、材料費の削減にもつながります。
さらに、ワークフローがすべてソフトウェアで制御されているため、専門的な知識やノウハウは不要です。作りたいものの3D CADデータさえ準備すれば、予め組み込まれているメーカー開発済みのパラメータにより、簡単に造形できます。
高純度な焼結を実現する真空レトルト方式焼結炉 PureSinterファーネスについて
Desktop Metal社の3Dプリンターでは、造形後に焼結という工程があり、ファーネス(焼結炉)を使用します。ここで紹介する「PureSinter(ピュアシンター)ファーネス」は、最新型のファーネスであり、上位オプションに位置付けられています。
その名の通り、「PureSinterファーネス」は超高純度焼結を可能にしている点が大きな特徴のひとつです。高純度の焼結を可能にしている理由は、真空レトルトという画期的な構造の採用にあります。従来は炉の中全体にガスを入れて焼結していましたが、「PureSinterファーネス」は、炉内の造形物を並べるレトルトという棚にかぶせるためのドーム形状のフタがあり、それで密閉される真空レトルトの中にガスを入れて焼結します。そのため、従来、炉内やヒーター、さらには部品自体に不純物が付着することがありましたが、「PureSinterファーネス」ではそうした不純物の付着が防げます。たとえばチタンなどを焼結する場合は酸素などに反応しやすいことによる弊害がありましたが、「PureSinterファーネス」ならその懸念も軽減できます。
また、従来のファーネスでは、焼結後に自然冷却するために、取り出しまでに20時間ほど待つ必要がありました。もし急速冷却したい場合には、別途にチラーという冷却装置を用意する必要がありました。しかし「PureSinterファーネス」では、17個のファンを搭載したことで、積極的に冷却を行い、従来20時間かかっていたところを付帯設備なく4時間程度で取り出しが可能となり、大幅な短縮ができました。
「PureSinterファーネス」は、金属3Dプリンター用としてだけではなく、粉末冶金や、金属粉末の射出成型(MIM)などの焼結にも利用可能で、活用シーンの幅が広いファーネスだといえます。
金属3Dプリンターを導入したいが、どんな製品を選ぶべきか、また導入コストや費用対効果をどう考えればいいのかわからない、といったお悩みがあれば、まずは丸紅情報システムズにご相談ください。お客様の状況に応じた最適なソリューションをご提案いたします。
本記事に関連するウェビナーの視聴
金属3Dプリンターの事例紹介ウェビナーを今すぐ視聴いただけます