これまで、さまざまな方式の金属3Dプリンターが市場に投入されてきたが、試作品の造形という用途が主流だった。しかし、バインダージェット方式の登場によって、今日では実用品の多品種少量生産も可能になっている。
本稿では、金属3Dプリンター普及の背景や、バインダージェット方式により実現する、高精度な実用品の多品種少量生産について、実際に造形サービスを展開する名古屋特殊鋼株式会社の事例を交え解説する。また、曲面形状や複雑形状の造形物を生産できるが故に必要となる、より精密な検査を実現する3Dスキャナの活用などについても解説する。
AM2.0時代といわれる現代において、バインダージェット方式の金属3Dプリンターの活用や、造形物の検査などの実態について、丸紅情報システムズ株式会社 製造ソリューション事業本部 デジタル マニュファクチャリング部 営業二課 藤井 健太(3Dプリンター営業担当)と、同社 計測製造ソリューション部 前田 成博(3Dスキャナ営業担当)、そして名古屋特殊鋼株式会社 小川原 幹雄氏に話を聞いた。
従来工法では難しかった多品種少量生産に対応できる金属3Dプリンター
――昨今、金属3Dプリンターが注目されている背景について教えてください。
藤井 金属3Dプリンターが注目されるようになった背景には、いくつかの要因があります。従来の機械加工や鋳造、粉末冶金といった工法では、製造できる形状に制約が多く、また金型や治具が必要になるなど、生産効率やリードタイム、コストの面からも多品種少量生産に向かないといった課題がありました。そうした課題の解決策として、製造できる形状の自由度が高く、生産性の高さから多品種少量生産にも向いているバインダージェット方式の金属3Dプリンターが注目を集めています。
また、自動車や航空機、産業用ロボットをはじめとする製造業において、カーボンニュートラルの必要性を背景に、部品などを軽量化することでエネルギー消費を軽減することが重要課題になっています。それを実現するため、トポロジー最適化やジェネレーティブデザインの最適化設計をそのまま再現できるという特徴があることも、金属3Dプリンターが注目される背景となっています。さらには、従来は複数の部品をそれぞれ手配・製造・検査し組み合わせて作り上げていたものを、3Dプリンターであれば部品統合して一体造形できる点も大きなメリットとして評価されています。
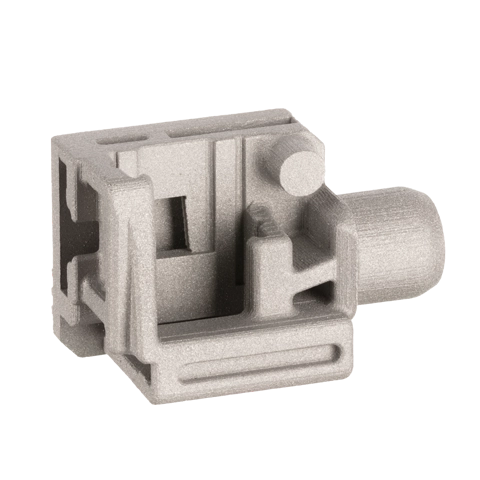
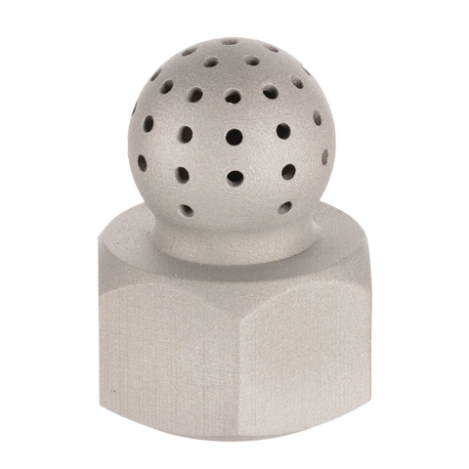
――それほどのメリットがある金属3Dプリンターですが、導入のハードルは何かありますか。
藤井 ひとつには、コストの問題があると思います。3Dプリンターには、樹脂を扱うものと、金属を扱うものの、大きく2種類がありますが、一般的な価格で比較すると、金属3Dプリンターは、樹脂3Dプリンターと比べて10倍ほどのイニシャルコストがかかります。そのため、導入に慎重になる企業が少なくありません。
また、イニシャルコストの問題をクリアできたとしても、金属3Dプリンターを設置し運用する環境の整備も、企業にとっては難しい問題になるケースがあるようです。金属粉末を扱う金属3Dプリンターだと、ある程度の環境整備が必須になるのです。
金属加工の可能性を広げる金属3Dプリンターによる造形サービス
――金属3Dプリンターのメリットは理解していながらも、さまざまな理由で導入できていない企業などに対して、名古屋特殊鋼様では金属3Dプリンターによる造形サービスを展開していますが、どのようなサービスなのかお教えください。
小川原氏 当社(名古屋特殊鋼)は、金属加工をメイン業務としていますので、金属3Dプリンターによる造形サービスといっても、単に依頼された部品などを造形するだけでなく、それにプラスアルファして切削や磨きといった加工も加えながら、より精度の高い実用品の製造・提供に取り組んでいます。
――なぜ、金属3Dプリンターを導入しようと思ったのですか。
小川原氏 メインの金属加工業務を、今後どのように発展させていくのか、ということは当社としてもずっと課題になっていました。そこで、同業他社との差別化や、当社自体の技術向上を図る上で、金属3Dプリンターに着目しました。そして、現有の切削加工に金属造形を加えることで、新しいものづくりが出来るのではと考えたからです。実はかなり以前から金属3Dプリンターの導入は検討していたのですが、どの方式がいいのかで迷っていました。そんな折に丸紅情報システムズさんからバインダージェット方式の金属3Dプリンターが発売されたのを知って、いろいろと相談させていただく中で、従来の方式に比べても、バインダージェット方式が何かとメリットがあるということで、バインタージェット方式に決めました。
バインダージェット方式の金属3Dプリンター導入を決めてからは、複数のメーカーの製品を比較検討しました。その上で、丸紅情報システムズさんが扱っているShopシステムにしました。
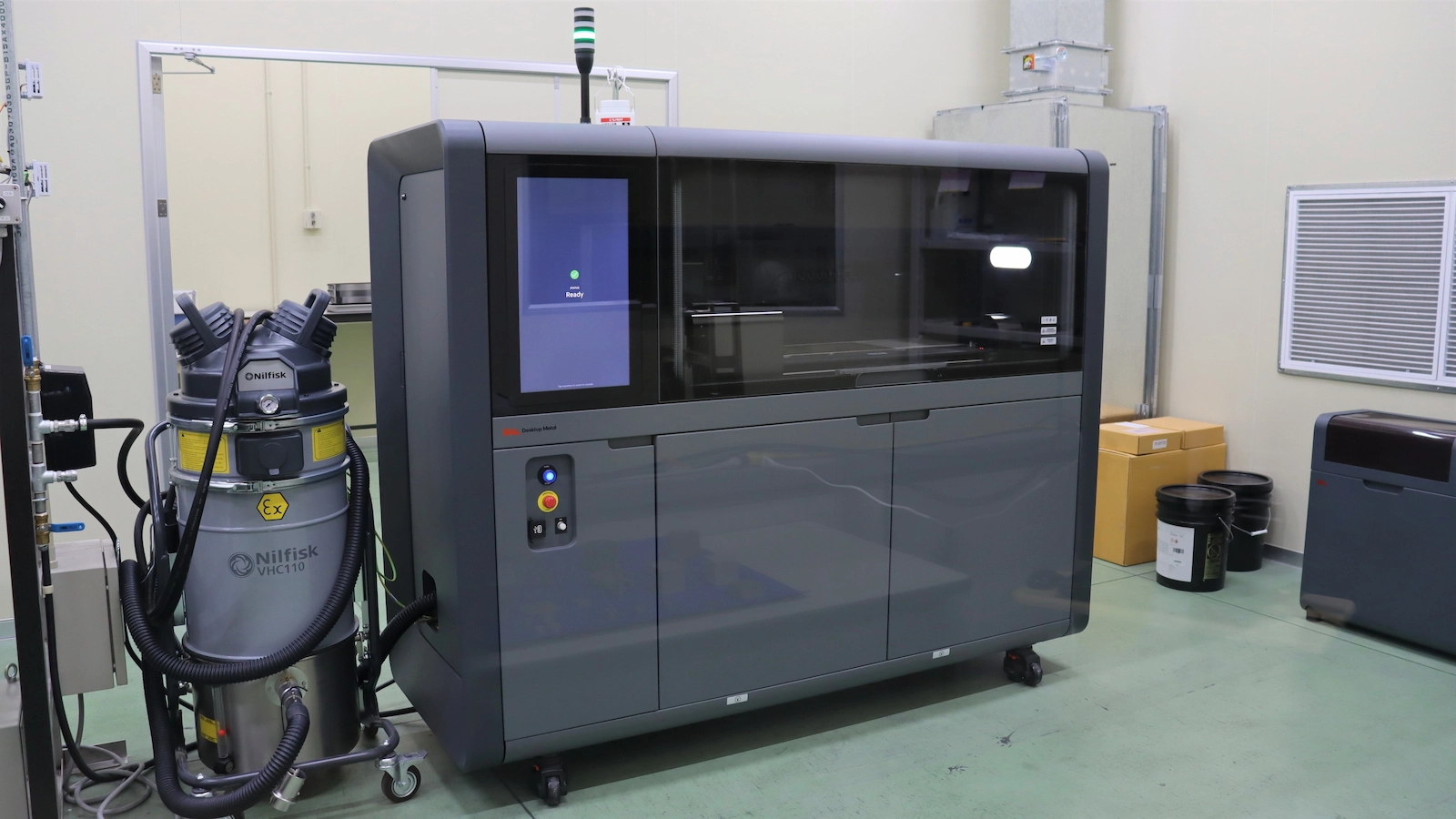
Shopシステム導入の決め手としては、造形から焼結までの一連のプロセスに必要な装置がシステムとして完成された形になっていて、導入がしやすかったということがひとつあります。他のメーカーのものだと、焼結炉は別メーカーのものを用意しなければならないこともあり、そうした点は導入のネックになります。
さらに、他のメーカーのものに比べて造形エリアが広く、さまざまな種類の造形物に対応できそうだという点も決め手になりました。
藤井 名古屋特殊鋼様には、ShopシステムProを導入いただきました。この機種の特徴は、メーカー純正以外の材料にも拡張性があることで、より幅広い材料を使って、さまざまな造形に取り組みたいとお考えだった名古屋特殊鋼様には、非常にマッチしていると思います。
またバインダージェット方式の場合、造形の際にサポート材が不要なので、部品を高さ方向にも積み重ねて配置でき、造形後のサポート除去工程も効率化できるという点も大きなメリットとして挙げられます。
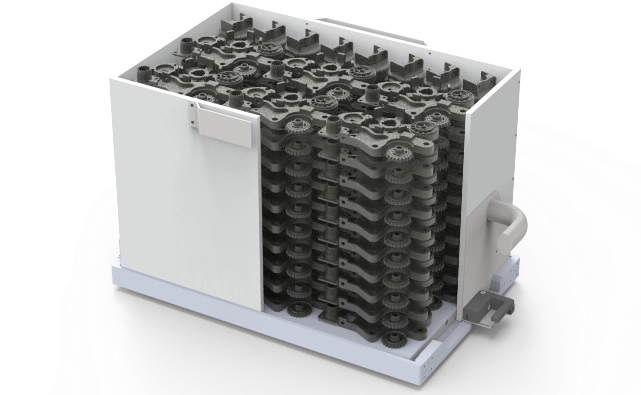
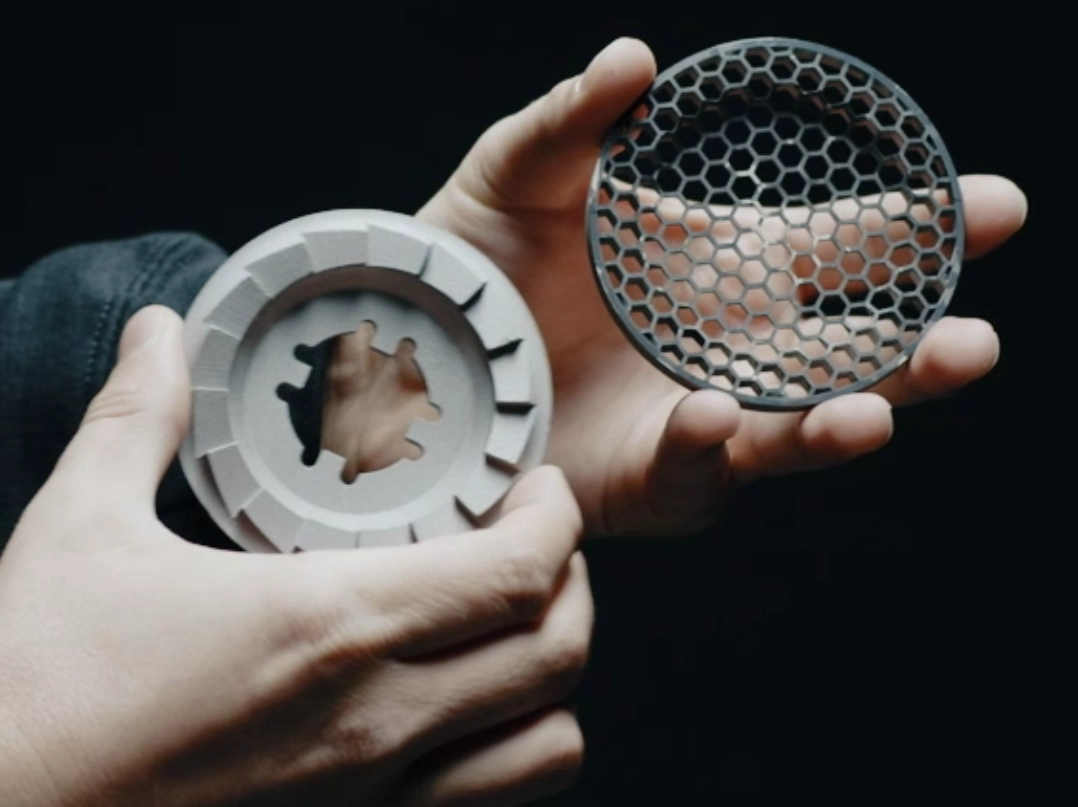
Shopシステムはその高い造形品質と生産性を活かすことで、試作品の造形にとどまらず、多品種少量生産といった実用品用途でも十分活用いただける可能性があると考えています。
複雑形状である金属造形品の検査に最適な高精度3Dスキャナ「ATOS」
――Shopシステムのようなバインダージェット方式の金属3Dプリンターであれば、実用品の製造も可能とのことですが、実用品用途では検査が必要だと思います。金属造形品にはどんな検査が適していますか。
前田 結論からいえば、3Dスキャナが適しているといえます。3Dスキャナは測定対象物をスキャニングして3Dデータ化する装置です。大量の3次元座標点をポリゴンデータとして生成し3Dデータとして取得できます。
3Dスキャナを使うことで、対象物の全体形状を測定でき、測定データとCADデータを位置合わせのうえ、比較結果をカラー表示できます。一致している箇所が緑色、ずれている箇所が赤色や青色で示されるため、全体形状の品質を素早く可視化できます。
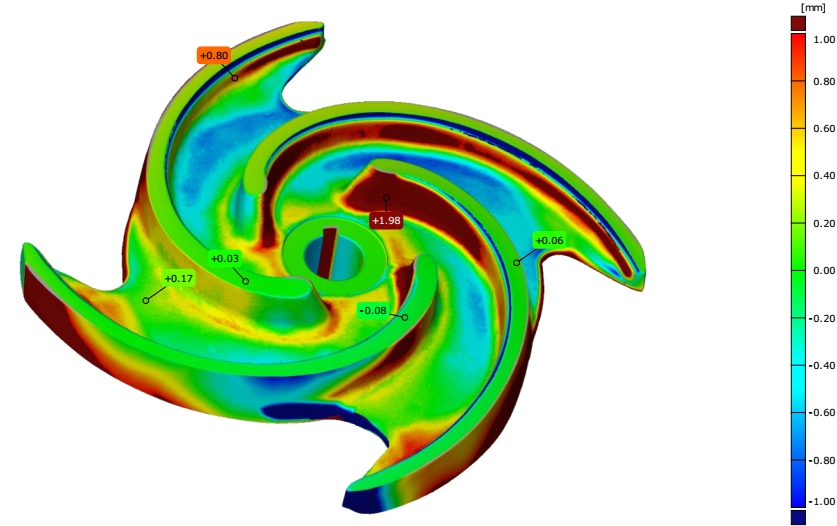
金属3Dプリンターでは従来工法では難しかった複雑形状で造形することが多く、CMMをはじめとした従来の点測定では大量の箇所を測定しなければならず時間がかかります。3Dスキャナでは素早く全体形状を検査できる為、複雑形状である金属造形品の検査は3Dスキャナが適しています。
――ATOSの特徴を教えてください。
前田 ATOSは中央のLEDプロジェクターと、その左右にある2つのカメラで構成されており、メーカー独自のトリプルスキャン測定方式により複雑形状を素早く測定することが可能です。トリプルスキャン測定方式では、左右カメラの三角測量、LEDプロジェクターと左カメラの三角測量、LEDプロジェクターと右カメラの三角測量、合計3回の三角測量を1スキャン最速0.8秒で測定します。従来死角の多い複雑形状品でも、トリプルスキャン測定方式を用いることで簡単かつ正確な測定ができます。
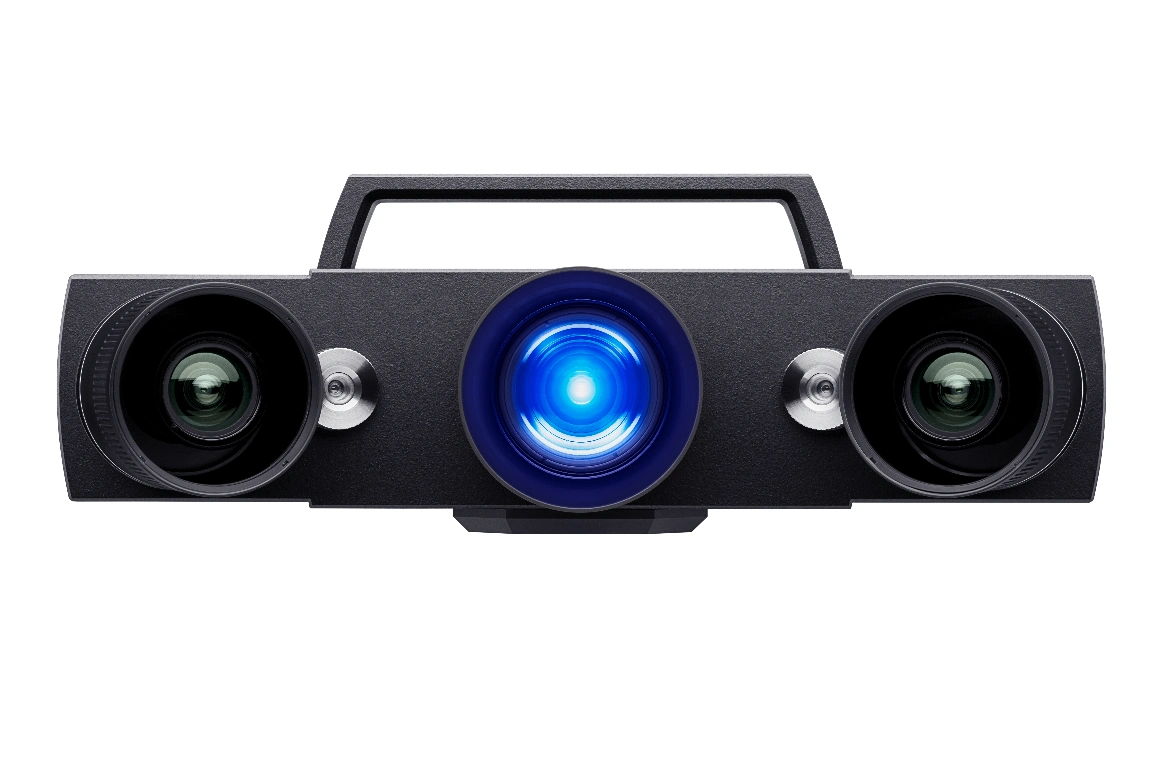
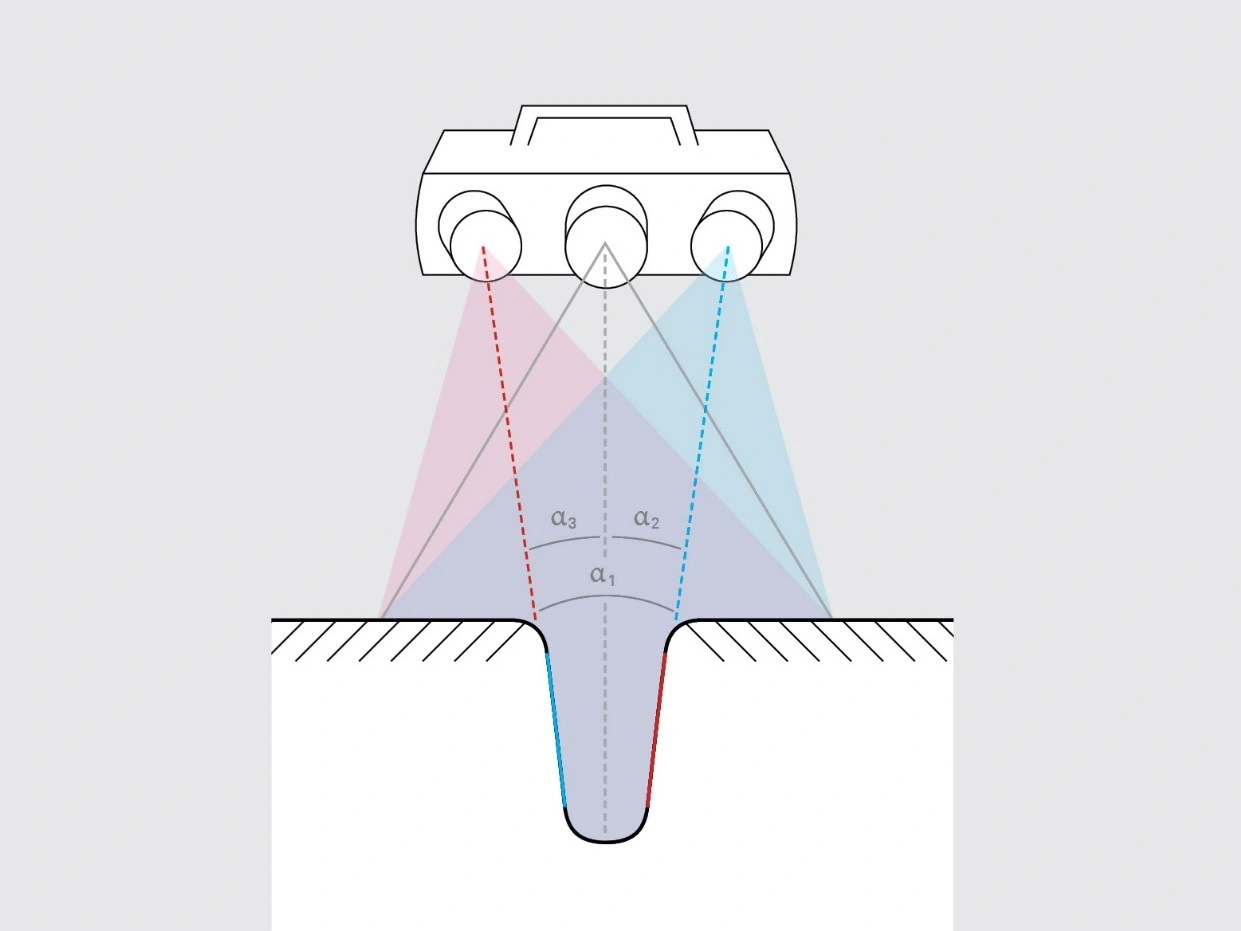
また、ATOSは1度のスキャンで最大1200万点の3次元座標を取得でき、微細形状を正確に測定できます。金属3Dプリンターでは従来工法では難しかった微細形状で造形することも多く、ATOSはこの点でも競合製品に比べて優位性があります。
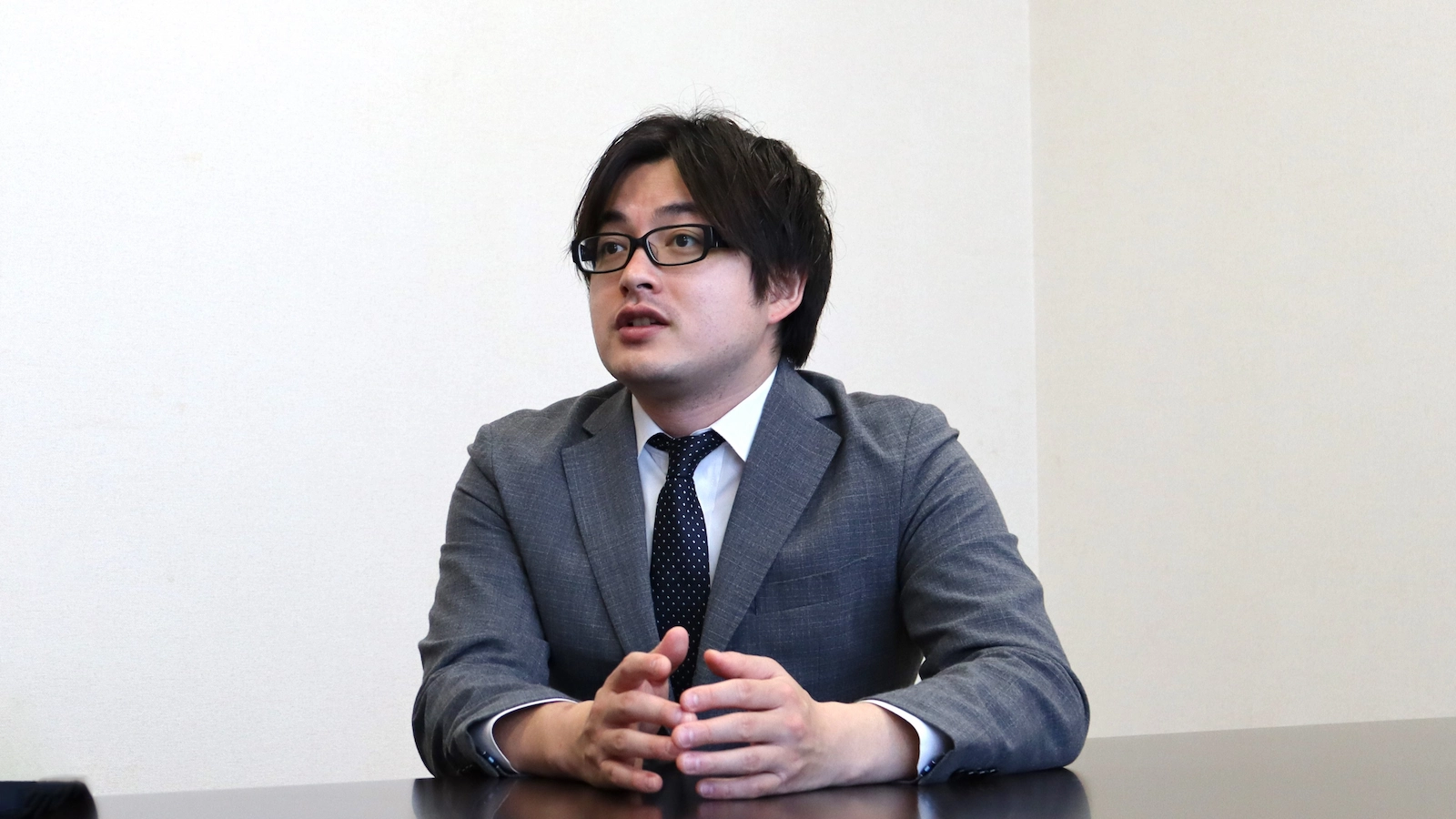
さらに昨今では現物のスキャンデータをシミュレーション(CAE)にインプットすることで、製造中におこる変形の予測精度を向上させ、高精度な造形の実現へ取り組む企業が増えてきています。スキャンデータが正確であるほど予測精度も向上しますので、ATOSで測定した正確なスキャンデータとシミュレーションの組み合わせは、高精度な造形の実現に重要な要素になります。以上の点が評価され、金属造形に携わる国内外の多くの企業でATOSを導入頂いています。
焼結中に起こる複雑な変形をシミュレーションし、変形補正形状をスピーディに自動生成するLive Sinter
――Shopシステムでは高精度な造形を実現するために、製造上でおこる変形に対して、何か対処をしていますか。
藤井 バインダージェット方式の金属3Dプリンターでは、造形後に高密度な金属組織を形成させる焼結プロセスがあります。この焼結プロセスでおこる変形をシミュレーションで予測し、高精度な造形の実現に取り組んでいます。焼結プロセスで、造形品は2割程度収縮します。その変形を予測して、造形ソフトウェアにて2割ほど大きく造形するように自動で調整されます。
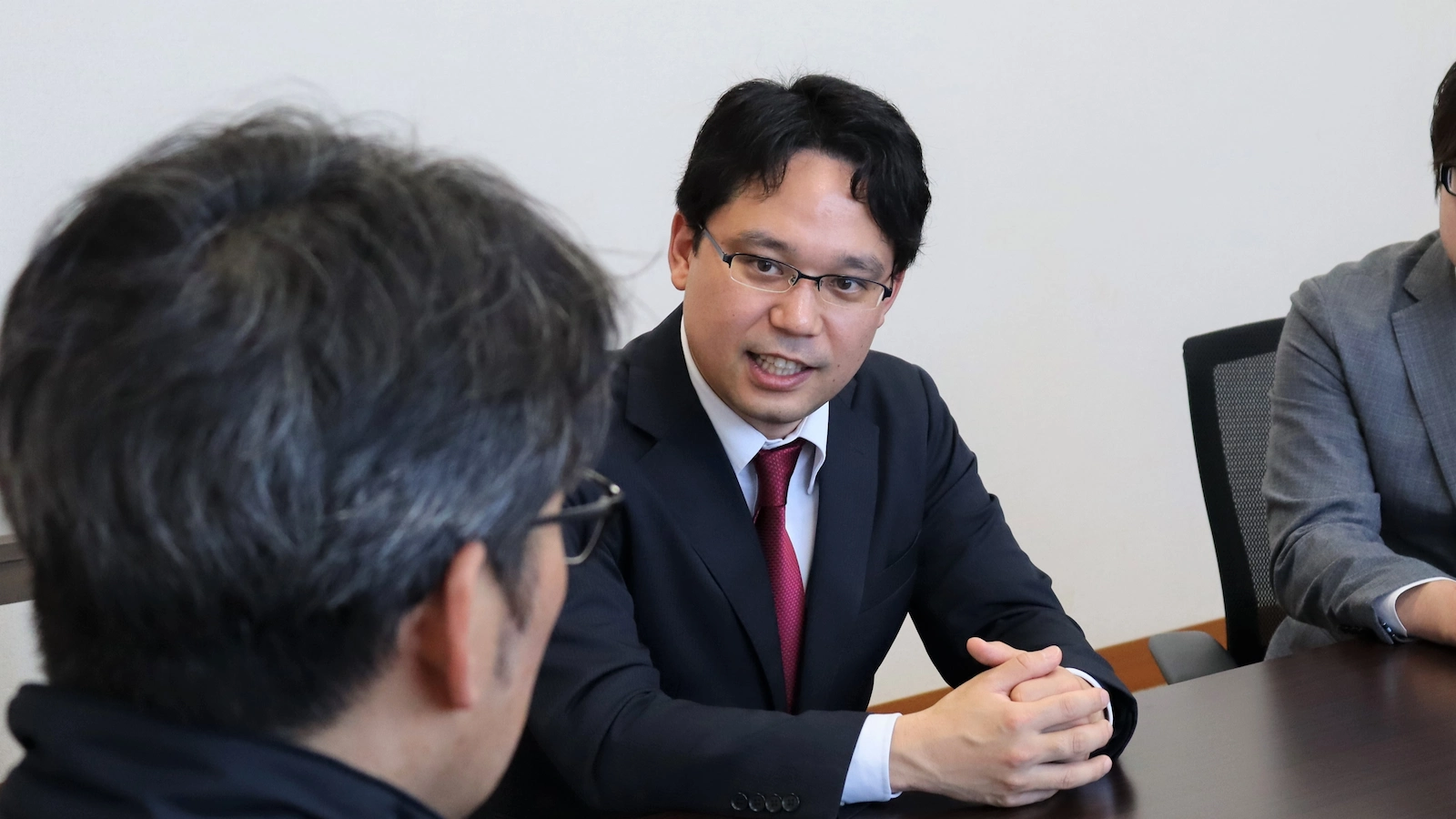
また、焼結による収縮変形以外にも、重力によるダレや、肉厚の違いによる反りといった変形要因もあります。その対策のために、セッターといわれるサポート構造を使って、変形を抑えるという手法もあります。しかし、特に小さい部品の場合に顕著ですが、造形物に対するセッターの割合が大きくなり、生産性が低下するという問題がありました。
その問題を解決できる可能性があるのが、「Live Sinter」というソフトウェアです。ShopシステムのメーカーであるDesktop Metal社が開発した純正のソフトウェアで、このLive Sinterを使うことで、焼結の際に起こる変形をシミュレーションによって解析・予測し、かつ、その予測に基づいて焼結後の変形を見越した逆補正形状を自動で生成してくれます。
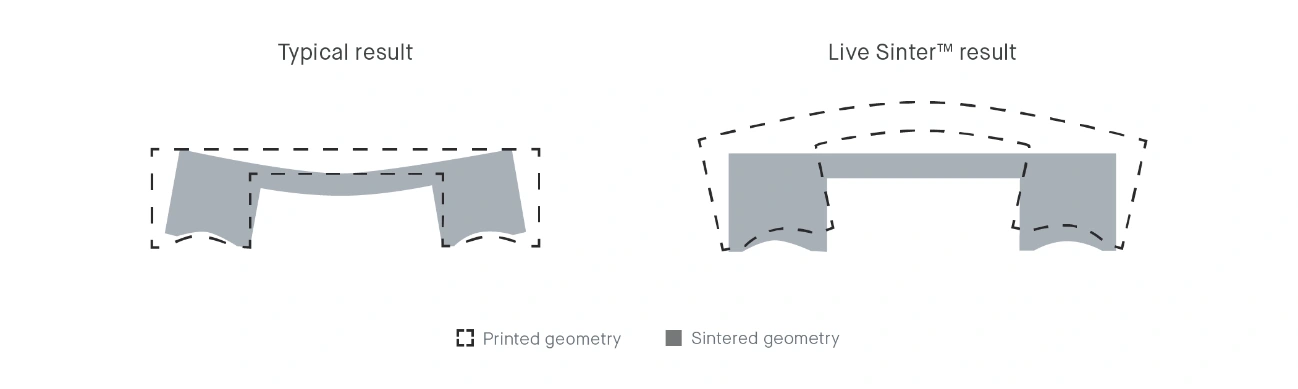
以前から変形をシミュレーションするソフトウェアはありましたが、Live Sinterの優れた点は、最終的に欲しい形状に近づけられる補正形状を予測結果に基づいて自動で生成できてしまうという点にあります。
造形・焼結後に、変形によって必要な精度が得られなかったという場合には、その結果を踏まえて補正形状を設計しなければなりません。人が対応する場合、ものによっては数時間、あるいは数日間かかることもありますが、Live Sinterを活用することで、そういった作業をかなり効率化することが可能になります。
Shopシステム+ATOS & Live Sinterの組み合わせで、高精度の造形を実現
――名古屋特殊鋼様では、ShopシステムProに加えて、ATOS、Live Sinterを活用されているとのことですが、造形物の精度向上につながっていますか。
小川原氏 当社では、金属3Dプリンターを導入する以前は、焼結による変形といったことについては、まったくノウハウがありませんでしたが、Live Sinterを活用することで、1回目の造形の段階から、ほぼ欲しい形状を問題なく取り出すことができています。
そして、取り出した現物は、ATOSを使って検査・測定し、その結果をさらにLive Sinterにフィードバックすることで、さらに精度を上げるということにも取り組んでいて、成果を上げています。
――造形サービスの今後の展開などについて、お話しいただけることがあればお願いします。
小川原氏 当社が金属3Dプリンターを導入して、造形サービスを始めてから、ほぼ1年が経ちます。既存のお客様へのPRや現場の見学会なども行い、お客様と会話しながら、どのようなものに適用できるのか、場合によってはテストなどをやりながら、商談の幅を広げています。また、これまで当社とお取引のなかったお客様から、金属3Dプリンターをきっかけにお話をいただくなど、新規顧客の開拓にも好影響が出始めています。
これからも、適用範囲を広げるなどして、造形サービスの案件をもっと拡大していきたいと考えています。そのためには使える材料の幅を広げることも重要と考え、そうした取り組みも始めています。
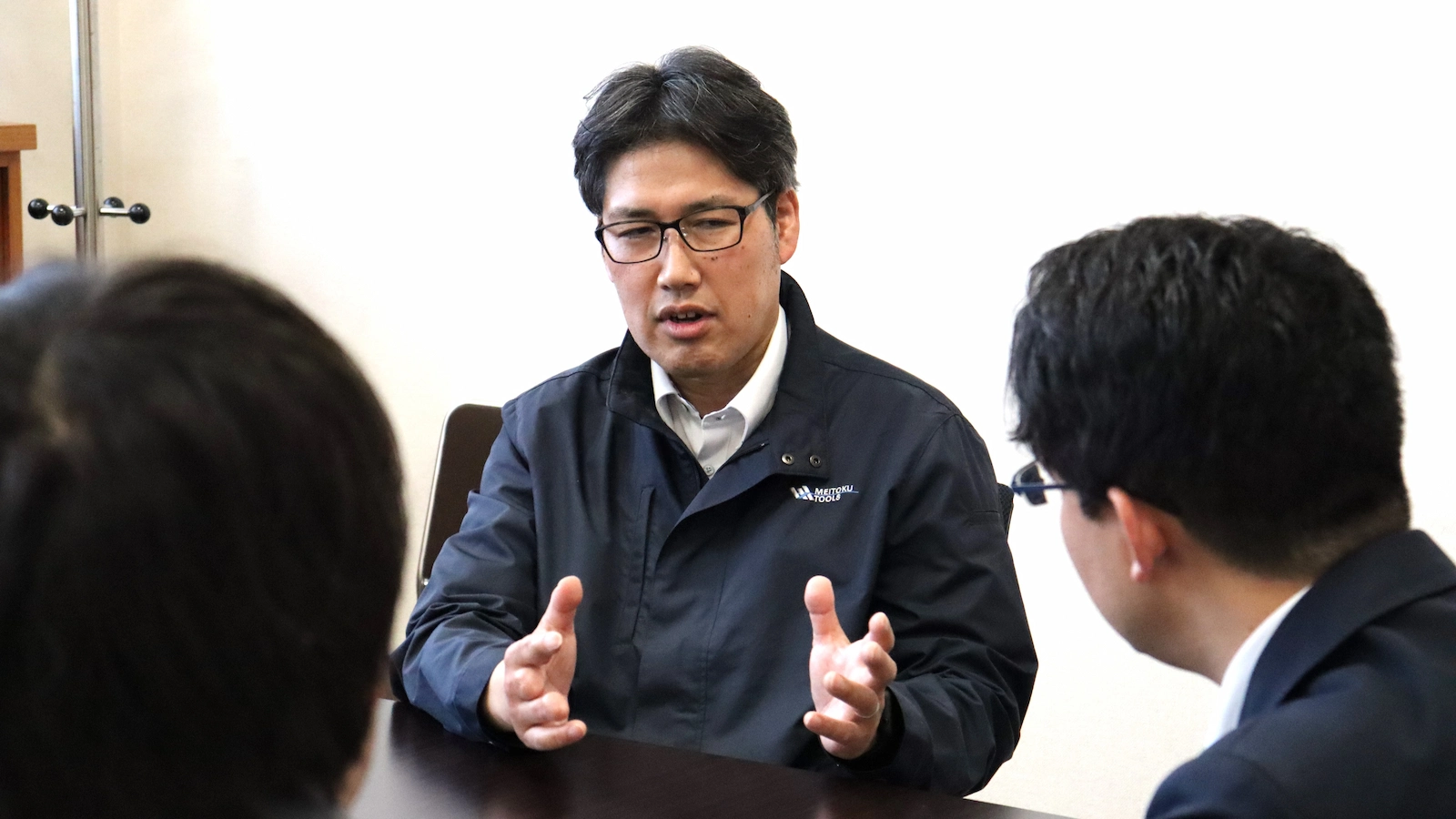
世の中的には、金属3Dプリンターの特性を生かした部品設計が進んでいないという印象があります。今後は金属3Dプリンターに適した部品の設計を提案するなど、業務の幅を広げ、お客様に提案していきたいと思っています。
さらに、金属3Dプリンターを導入後、今までのものづくりとは違う案件なども引き合いをいただくようになりました。それをどう実現するかを検討することは、大変ではありますが、パズルを解くようなワクワク感というか、新しいことにチャレンジする楽しさを感じたりしています。社内で金属3Dプリンターに興味をもつ社員も増え、今までにない手法や加工方法のアイデアを、周りの社員が出してくれるといった好影響も出ていると感じています。
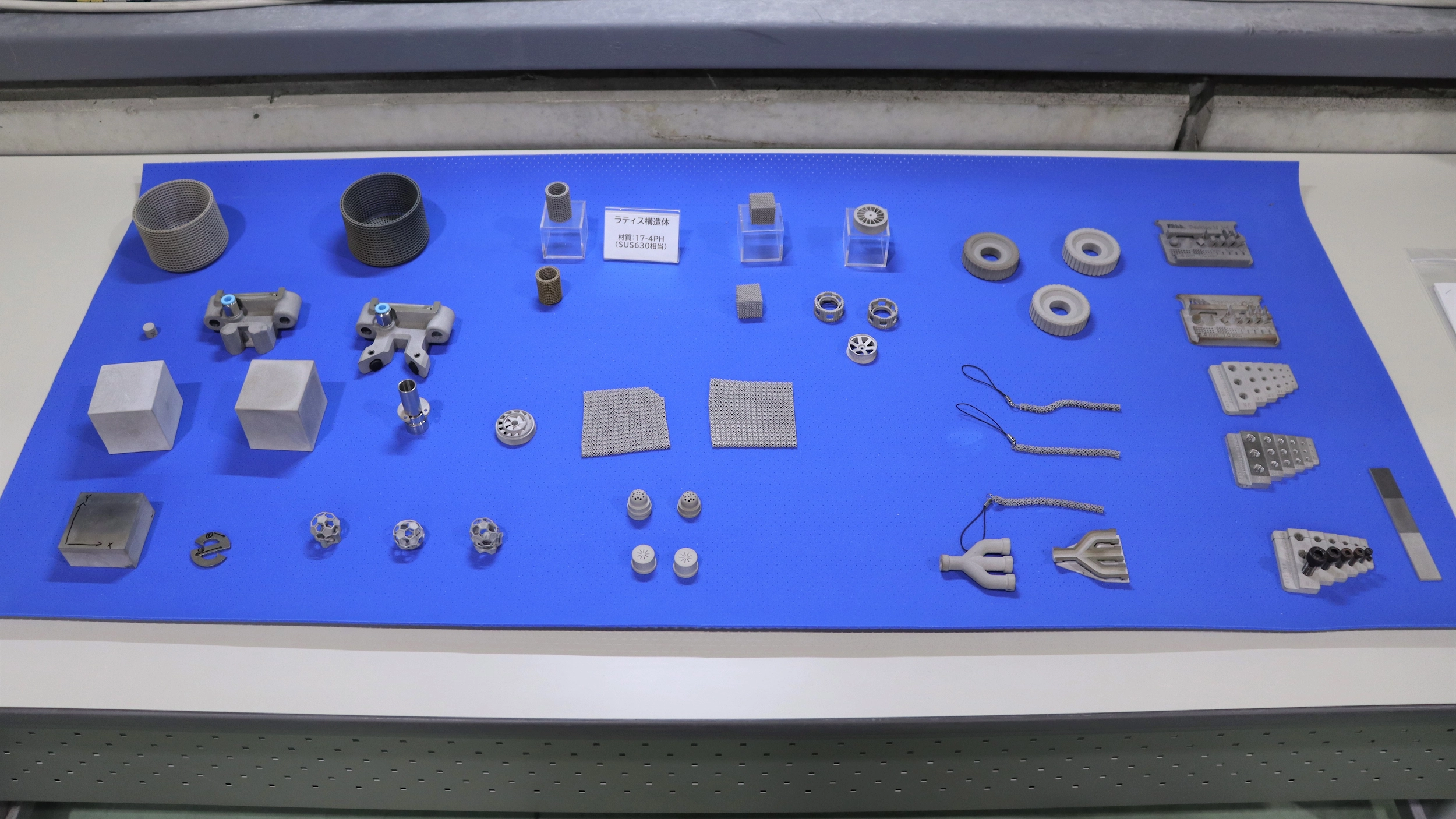
現在、金属3Dプリンターは試作品製作のためのツールではなく、実用品の生産ツールとなっている。従来なら収益構造が作りにくかった多品種少量生産を採算ベースで展開できる可能性も広がっている。自社で導入しなくても、名古屋特殊鋼のような造形サービスを提供してくれる企業との連携によって、その恩恵を受けることも可能になっている。この機会に、金属3Dプリンターをどう活用するべきかについて、検討してみることをおすすめしたい。
本記事に関連するウェビナーの視聴
金属3Dプリンターの精度、造形サービスに関する
ウェビナーを今すぐ視聴いただけます