金属3Dプリンターに精度が求められる背景
近年、金属3Dプリンターの造形品は、補給部品または実際に使用する部品の量産品として利用されることが増えており、製造される造形品には高い品質(高精度)が求められるようになってきています。
たとえば、金属3Dプリンターで実部品を量産する場合、造形品はニアネットシェイプと呼ばれる、最終形状に近い仕上がりで出力され、最小限の仕上げ加工により短時間で完成させられるようになっています。金属3Dプリンターの精度が低く、形状が設計よりも膨らんでしまうと、後加工に時間がかかり、生産性が低下します。反対に、設計よりも形状が欠損してしまうと、加工で修正できず不良となってしまいます。このように、実際に使用する部品の量産用途で金属3Dプリンターを使用する場合は、高精度な造形が求められます。
最近では、金属3Dプリンターの解像度が向上し、シミュレーション技術の発達により、高精度な造形が可能になりました。その結果、実用的な製品の造形に用途が広がり、金属3Dプリンターで作られる造形品の精度に注目が集まっています。
金属3Dプリンターの精度とは
金属3Dプリンターの精度には、大きく分けて2つの要素があります。
金属3Dプリンターの精度における2つの要素
1つは「解像度」です。これはどの程度詳細な形状が再現されているかという度合いを指すものです。もう1つは「寸法誤差偏差」です。これは完成した造形物がCAD寸法からどの程度ずれるかの度合いを指すものです。誤解されやすい点ですが、解像度が高くても寸法誤差偏差が小さいとは限りませんし、1個の寸法誤差が小さいからといって、複数作った時のばらつきが小さいとも限りません。
また、一概に金属3Dプリンターの精度といっても、金属3Dプリンターの方式によっても差があり、一律にどのくらいといえるものではありません。本稿では近年注目を集めている造形方式を一例に紹介していきます。
近年注目を集める造形方式の精度
1日あたり数百個の部品を造形できるという、高い生産性で近年注目されている「金属バインダージェット方式」の場合、その精度の目安は±2%と公表されています。精度は造形する物体の大きさに依存するため、数値ではなくパーセンテージで表すのが一般的です。この値は3Dデータを読み込んでそのまま造形した場合の値です。本稿の後半ではこの精度を上げる方法について詳しく解説します。
金属3Dプリンターの精度を決める4つの要素
金属3Dプリンターの精度を決定する要因(誤差を生み出す要因)は、方式により違いがありますが、大きくは次のものが挙げられます。
1.データの解像度
金属3Dプリンターに限らず、3Dプリンターは入力した3Dデータに基づいて造形をします。3Dプリンターに3D CADを読み込ませる際、解像度の低いデータを読み込ませてしまうと、造形品の精度も低下してしまうことが起こります。たとえばSTLファイルなどに変換した際に解像度が低下してしまうことも起こるため、こういった事態を防ぐためには、3D CADにおけるファイル出力時の解像度設定に注意する必要があります。
2.Z方向の解像度
金属3Dプリンターは材料を一層ずつ積み重ねて造形品を製作するため、一層あたりのZ方向(高さ)の精度は、積層する厚みを意味する「積層ピッチ」に影響されます。積層ピッチが細かければ、より正確な寸法が出しやすくなります。ただし、その分同じサイズのものを造形する場合にたくさん積層しなくてはいけないため、造形時間は伸びて生産性が低下してしまうというトレードオフの関係にあります。
また、金属粉末材料の場合は敷き詰めて積層していくという原理上、使用している金属粉末の最大粒径以下に積層ピッチを設定することはできません。
3.XY方向の解像度
高さの精度要因であるZ方向の積層ピッチと同様に、XY方向の解像度も、正確な寸法を出すうえで重要な要素であり、寸法だけでなく微細な形状の再現性にも影響を与えます。バインダージェット方式の金属3Dプリンターの場合、バインダーを射出するプリントヘッドの解像度としてdpi(ドット・パー・インチ)などで表現されますが、この数値が高いほど高解像度での造形が可能です。
4.焼結時の熱変形およびサポート除去
バインダージェット方式の金属3Dプリンターにおいては、造形後に電気炉による焼結工程が必要となります。この焼結によって造形品の体積が収縮し、空隙を埋めることで高密度な造形品が完成します。体積が収縮することによって、焼結前と後では寸法が変化することになり、これが精度に影響を及ぼします。
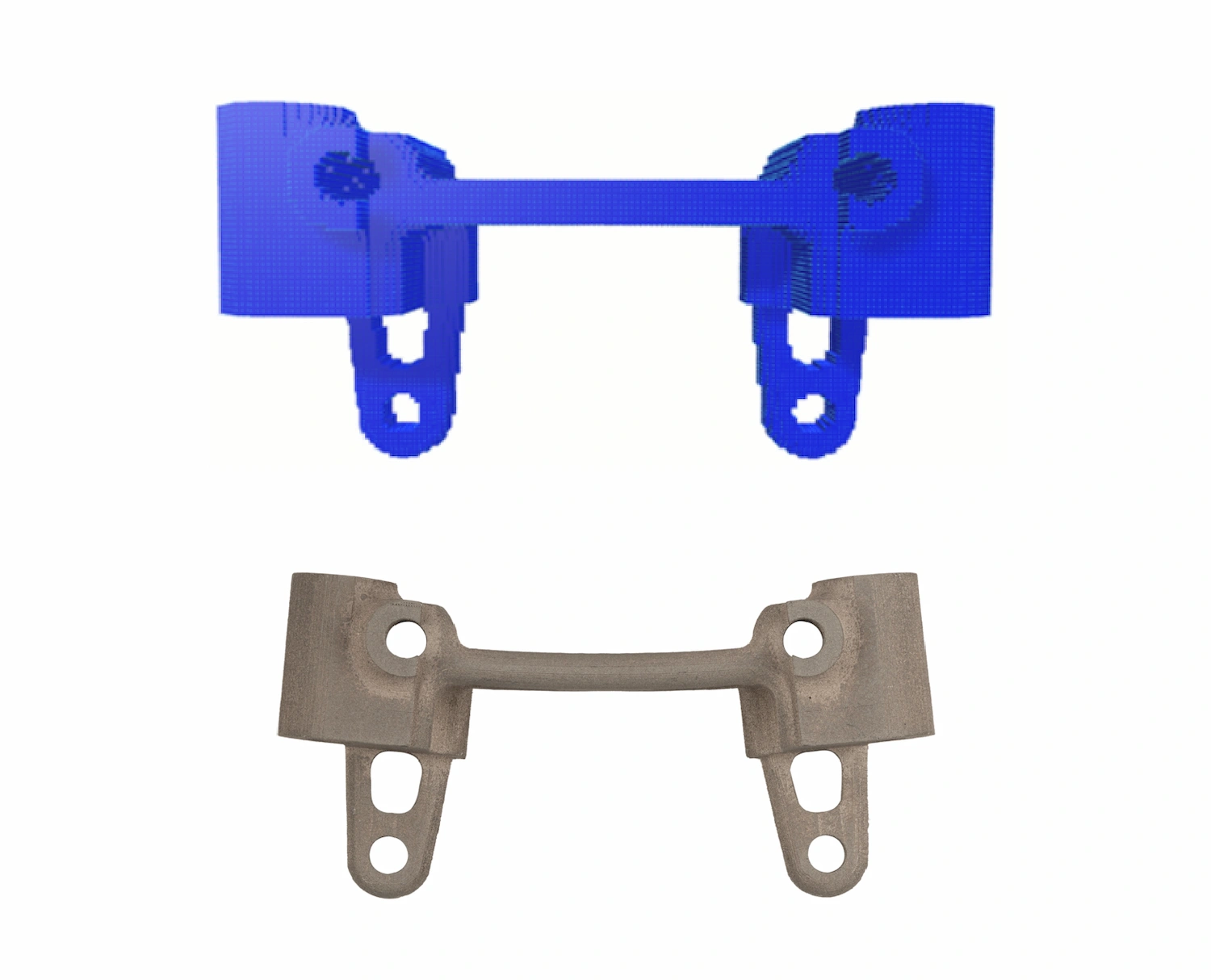
なお、造形中に焼結を行う造形方式もあり、その場合には造形中の反り返りなどによって精度に影響を及ぼす恐れがあります。そのため、モデルをベースプレートと呼ばれる土台に同じ金属によるサポート構造で接続してしっかり固定する必要性があり、後加工でこのサポート構造を除去する過程で、除去後に残留応力により変形してしまうことがあります。
造形品の精度確認方法
金属3Dプリンターでは、計測機で造形品の品質と精度を確認するケースが増えています。
造形品は複雑形状であることが多いため、ノギスや接触式三次元測定機だけでは造形品の形状精度を確認しきれず、全体形状を計測できる3Dスキャナが用いられます。また、造形品の内部形状精度を確認するためにX線CTが用いられることもあります。3DスキャナやX線CTを用いることで造形品の品質と精度をどう評価するか後述します。
3Dスキャナ
3Dスキャナを使用すると造形品の表面形状全体に対して大量の3D座標点を取得できます。設計データと造形品を3Dスキャンしたデータを重ね合わせると、表面形状全体の差異がカラーマップで表示されるので視覚的に品質を把握できます。これにより造形品の表面形状全体が設計公差内に収まっているか、また、公差に収まっていない箇所はどこなのか一目でわかります。
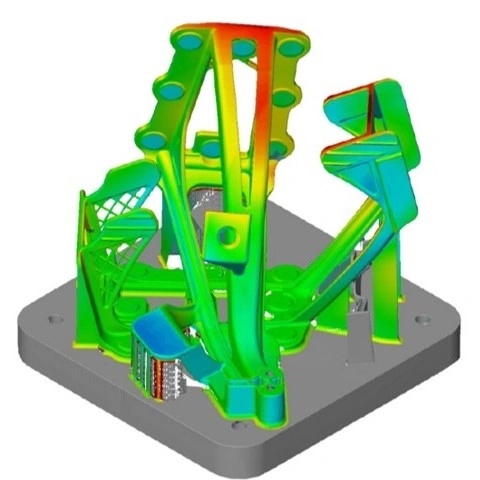
焼結による収縮は特定の箇所に発生するのではなく、形状によって全体的に不規則に収縮するため、造形品の検査は表面形状全体を測定できる3Dスキャナが一般的に用いられます。
また、造形品を工程ごとに3Dスキャンしたデータを重ね合わせることもできるため、各工程での形状変化をカラーマップによって視覚的に把握できます。これにより設計公差内に収めるにあたり、どの工程がボトルネックでどう対策すれば良いか判断しやすくなり、より高精度な造形を実現します。
3Dスキャナはカラーマップ評価だけでなく、一般的な寸法検査や輪郭度等の幾何公差検査も可能です。
X線CT
金属3Dプリンターの工法によっては造形の過程においてボイドができる場合があります。また、軽量化や機能向上の為に中空構造で造形する際に、金属粉末が内部に残ってしまうことがあります。内部欠陥は強度や機能の低下を引き起こしたり、加工時に表面に空洞が現れ、表面欠陥により造形品が不良になったりすることがあります。このようなことから、造形品は表面形状に加えて内部欠陥を評価する必要があるといえます。
評価方法として造形品を切断して評価する方法が一般的ですが、これには時間とコストがかかるため、X線CTによる非破壊評価が近年注目されております。
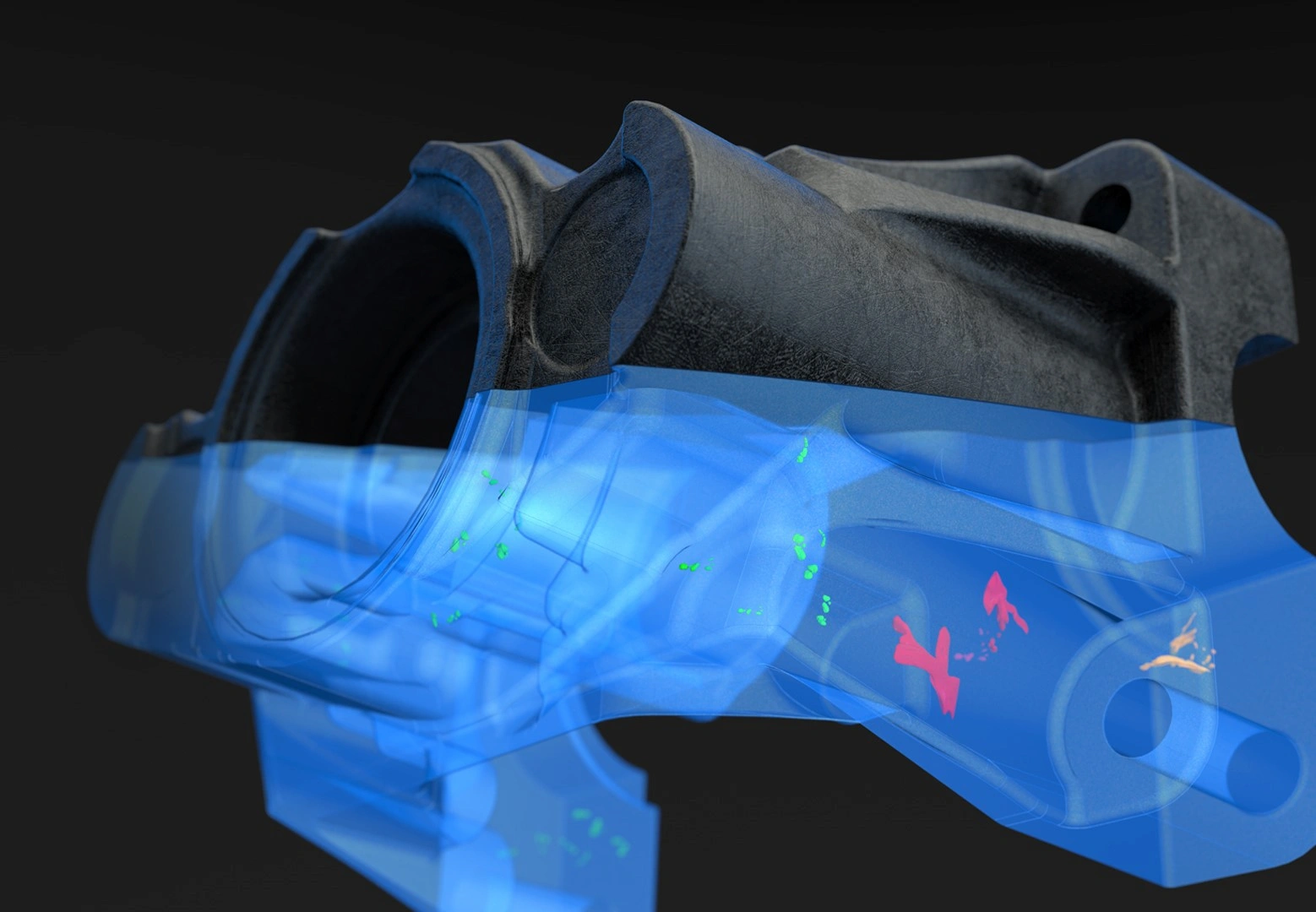
X線CTで計測した造形品の内部データからボイドを抽出し、ボイドの径や体積を評価したり、ボイドから表面の距離を求めたりすることで、加工後に表面に空洞が現れるかが判断できます。また、中空構造による内部形状において、設計データとCTデータを重ね合わせて内部形状の差異をカラーマップ表示できるので、設計通りの内部形状になっているか確認できます。
造形品の精度を向上させるには?
前項で解説したとおり、さまざまな要因により設計した3Dデータを読み込んでそのまま造形するだけでは、造形品のばらつきが大きく、治具や設備部品など精度があまり求められない用途に限られていました。
しかし、近年技術の進歩に伴い、次に紹介する革新的なシミュレーション技術を用いることで、より高精度な造形が実現し、補給部品としての利用や実際に使用する部品の量産に用途は拡大しつつあります。
熱変形シミュレーションによる形状補正
バインダージェット方式の金属3Dプリンターで造形・焼結した際に、どのように変形・収縮が発生するか、シミュレーションソフトウェアを活用することで、造形前に予め予測することが可能です。
設計したCADデータをソフトウェアに読み込み、焼結時の熱変形をシミュレーションすることにより、焼結中の変形・収縮を予測します。その結果に対して、焼結による変形・収縮を見込んだネガティブオフセットと呼ばれる逆補正形状を生成することで、造形品の精度を高めることが可能です。
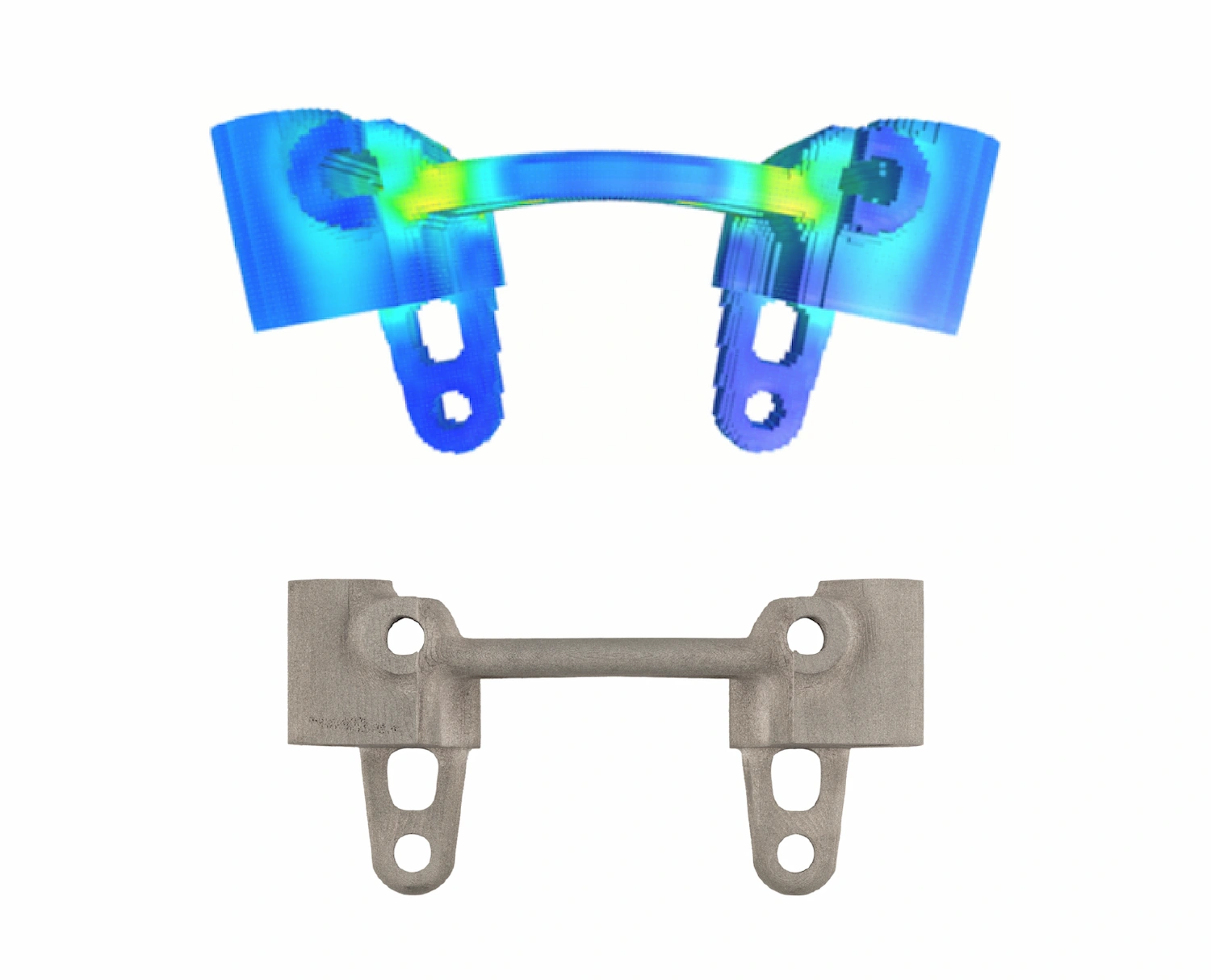
このシミュレーションを1回だけでなく、生成した逆補正形状に対して何度も繰り返すことで、さらに精度を高めることができます。たとえば、設計したCADデータでそのまま造形すると±2%程度の誤差が出ていたものが、このシミュレーションを繰り返し実施することで、±1%程度にまで誤差を抑えることが可能になります。
造形品の3Dスキャンデータを入力しシミュレーション精度を向上
事前シミュレーションによって、造形前に精度を高めることは可能ですが、実際の造形結果とシミュレーション結果には誤差が生じます。そこで、実際に造形した現物を3Dスキャナで測定し、そのスキャンデータをソフトウェアに読み込ませることで、さらに精度を高めることが可能になります。この工程により、シミュレーションで±1%に誤差を収めたものを更に±0.3%以内のばらつきに収めることも可能です。より高い精度が必要な部分には、加工を施すことによって造形品が実用品となることを実現できます。
丸紅情報システムズ取り扱い 金属3Dプリンター×3D計測機で高精度な造形を実現
近年、金属3Dプリンターは高い精度が要求される実用品製作用途で使用されるため、高精度な造形の実現が不可欠です。丸紅情報システムズが提供する「Shopシステム」と「ATOS」、「ZEISS METROTOM1500」を組み合わせた独自のものづくりDXを利用することで、高精度な造形品を数百個単位で安定的に製造することも実現可能になります。
バインダージェット方式金属3Dプリンター「Shopシステム」
Desktop Metal社が開発したバインダージェット方式金属3Dプリンター「Shopシステム」は、他のレーザー方式に比べて、最大10倍となる1日数百個の部品造形も可能な、生産性の高いバインダージェット方式を採用しています。
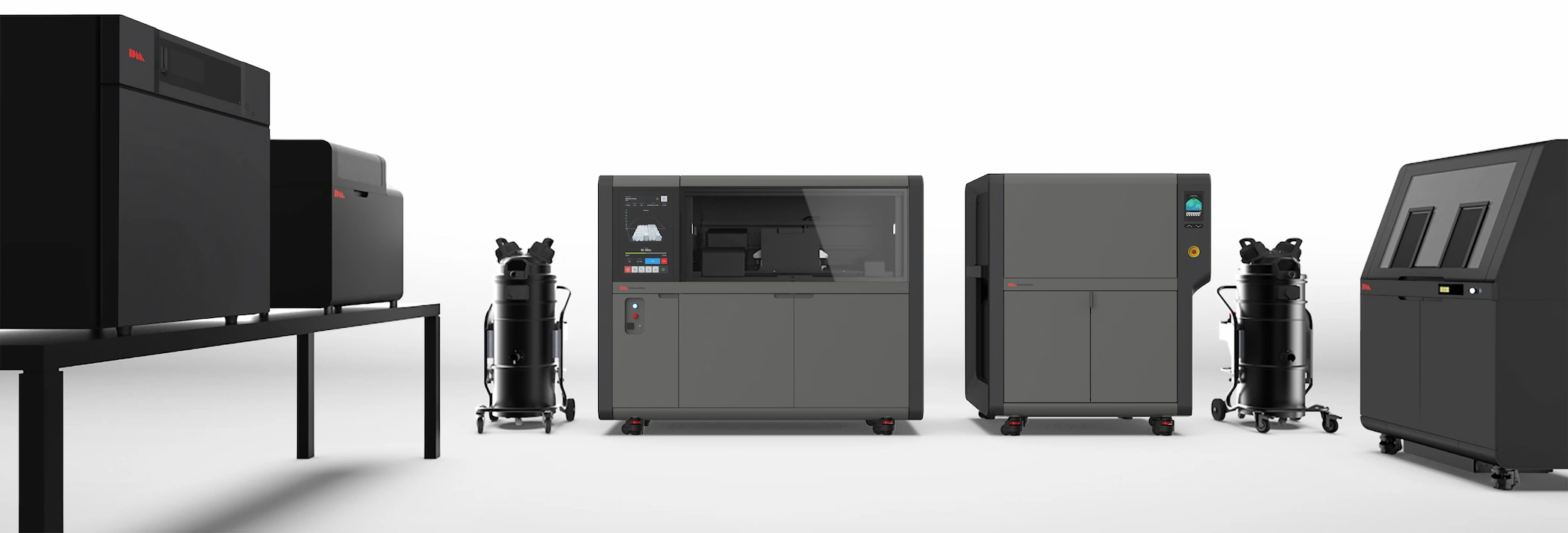
1600dpiの高い解像度のプリントヘッドを搭載し、高解像度での造形が可能です。さらに、Desktop Metal社が開発した「Live Sinter(ライブシンター)」というシミュレーションソフトウェアが付属されるため、CADデータをベースに焼結による変形・収縮をシミュレーションできます。
カメラ式高精度3Dスキャナ「ATOS」
丸紅情報システムズでは、接触式三次元測定機で有名なZEISSのグループであるCarl Zeiss GOM Metrology社が開発したカメラ式高精度3Dスキャナ「ATOS」を取り扱っています。
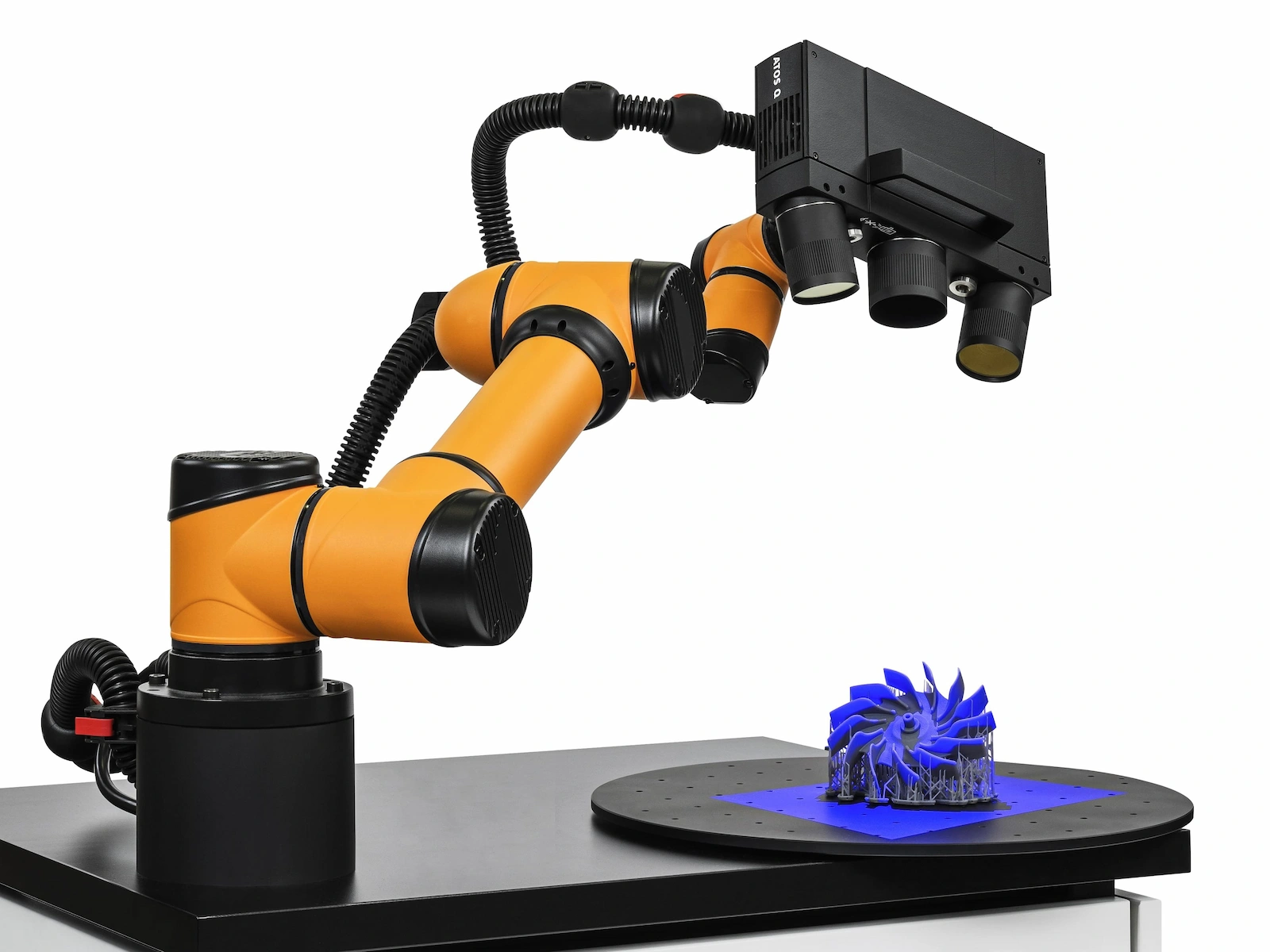
「ATOS」は左右2台のカメラと真ん中のLEDプロジェクター光源で構成され、最大1200万画素の高解像度カメラを採用しており、高精細なデータの取得が可能です。金属3Dプリンターの造形品は、主に微細かつ複雑形状のため、複雑形状を高精細にデータ化できる「ATOS」は造形品の寸法精度を確認するのに適しています。
計測用CT「ZEISS METROTOM 1500」
「ZEISS METROTOM 1500」は、国際原器とトレーサブルに繋がっている計測精度が保証された225kV X線CTです。
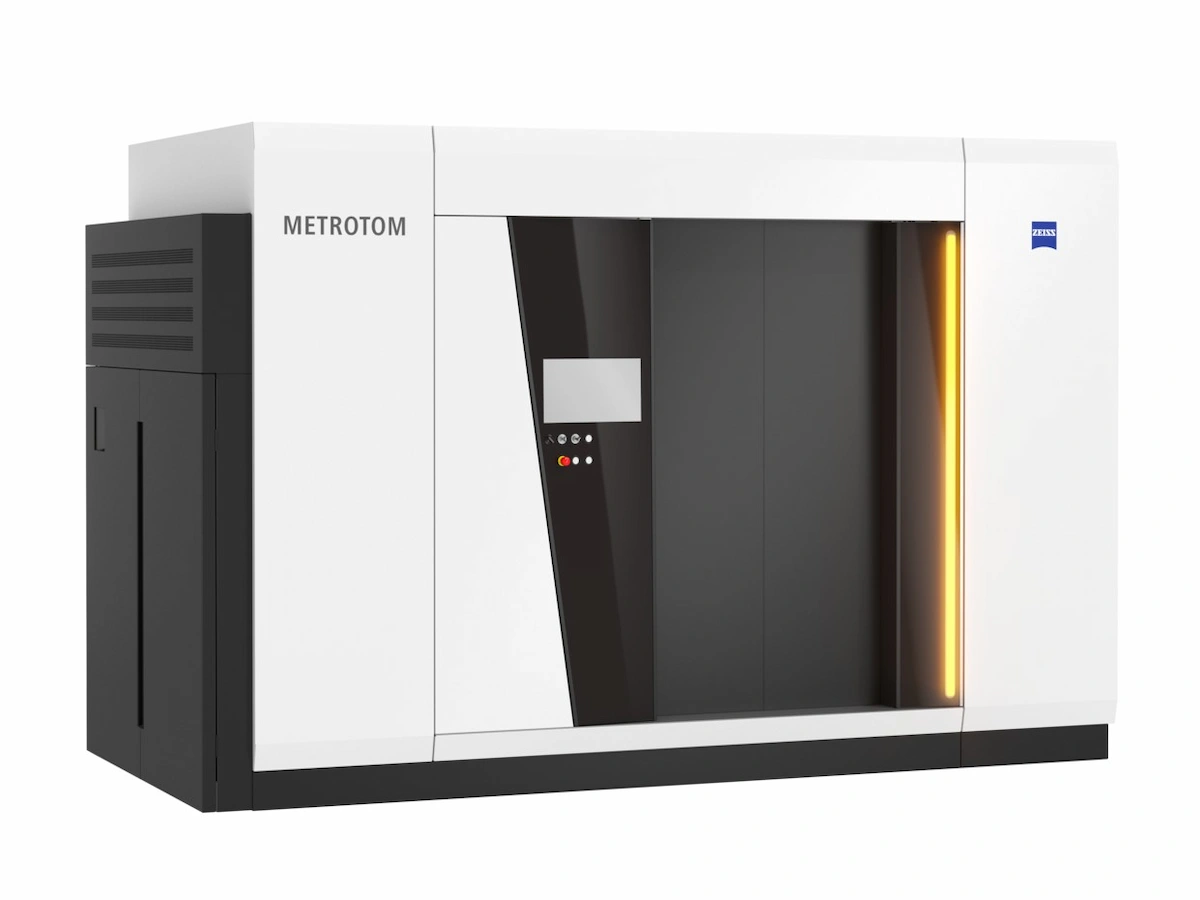
X線像の歪みと偏心を補正できるので、信頼性の高い内部評価が可能です。さらに特許取得済みの散乱線補正機構「scatterControl」を有しています。これにより225kVでありながら、一般的には450kV X線CTを使用するチタンやインコネルの様な重金属でも、内部形状や肉厚によっては透過し、内部欠陥を検出することが可能です。
金属3Dプリンターと3Dスキャナ 資料ダウンロード
本記事に関連する資料がダウンロードいただけます