巨大な建造物に心が惹かれるのはなぜだろう。
例えば船だ。
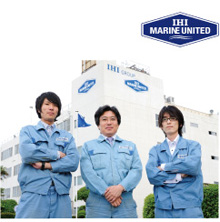
全長200mを超える巨大な船が、海の上を進んでいく姿は壮観の一言だが、ふと疑問がわく。
一体どうやってつくっているのか。
世界の造船所で採用しているグローバルスタンダードがブロック建造方式だ。
船全体を複数のブロックに分けて製造し、ミリ単位の精度で数百メートルに渡って組み上げていく。
船の大型化、多機能化が進む中、設計や製造の効率化、品質向上を実現する新たな仕組みが求められている。
150年以上に渡り、日本の近代化、産業の発展を支え、世界の造船業を牽引してきたアイ・エイチ・アイ マリンユナイテッド。同社の横浜工場を訪ね、巨大な船のつくり方とともに、船の建造プロセスを革新する3次元CADや仮想化技術の活用について取材した。
150年以上、日本の産業の発展を支え、世界の造船業を牽引
資源の少ない日本が、ここまで成長できた原動力は、高度な技術力に基づく“ものづくり”にあることに異論はないだろう。暮らしやビジネスに新たな価値をもたらす高品質な製品が、日本の港から世界中の消費者のもとへと運ばれていく。輸出の一方で、海外から多くの資源を輸入することで日本の社会が成り立っているのも事実だ。輸出入を合わせた日本の貿易量は、世界の海上貿易量の約1/6を占めている。世界とともに生きる、まさに貿易立国だ。その輸送の実に99.7%を担っているのが船である。
横浜港の南、根岸湾に面した臨海工業地帯に、日本を代表する造船会社の1つ、アイ・エイチ・アイ マリンユナイテッド(以下、IHIMU)の横浜工場がある。IHIMUの歴史は、1853年(嘉永6年)に徳川幕府によって開設された石川島造船所にまで遡る。以来150年以上、日本の近代化、産業の発展を支え、開発型造船会社として世界の造船業を牽引してきた。世界で最初に大型原油タンカー(載貨重量20万トンから30万トンまで)を建造し、タンカー大型化の流れに先鞭をつけ、環境負荷の少ない新型船の開発や船の一生をサポートするライフサイクル事業といった、環境を重視したテーマにも積極的に取り組んでいる。
今回の取材は、横浜工場内の設計事務所で行われた。船をつくる工場だけに敷地も広大だ。IHI横浜事業所の正門近くから取材場所までシャトルバスで向かった。この事業所には2,000人以上のスタッフが働いていて、朝と夕方のシャトルバスはとても混雑するそうだ。目的地で降りると、すぐそこには根岸湾。造船ドックでは、船の建造が行われていた。実際に船を目にすると、まずその大きさに目を奪われる。この巨大な建造物が海の上を動くというのは、大人になったいまでも心を惹かれてしまう。
IHIMU生産・システム技術統括部 横浜システムグループ 主査 溝川秀和氏も胸の内をこう語る。「ロケットや飛行機、船とか。とにかく大きくて動くものをつくりたいというのが入社した動機です。いまから20年前くらいになりますか。全体を組み立てて、ひとつの巨大な建造物に仕上げていく。文字通り、大きな仕事ですね。そこに、やりがいを感じています」
IHIMUでは、コンテナ船、客船・旅客カーフェリーなどの商船と、護衛艦をはじめとする艦艇の両方を建造している。船は大型化の傾向にあり、ほとんどが全長200m以上。超高層ビル並みの大きさの船をいったいどうやってつくっているのだろう。しかも、同時に複数の船が建造されている。
ブロックをミリ単位の精度で数百メートルに渡って組み上げていく
その方法は、多くの人にとって馴染み深いものだった。「船の全体設計の後、いくつかのブロックに分けて詳細設計を行い、ブロック単位で製造し1隻の船に組み上げていきます」と溝川氏。子供のときのブロック遊びを思い出してほしい。ブロックを組み合わせて形をつくる。考え方は同じだ。ブロック建造方式は世界中の造船所でグローバルスタンダードとなっている。
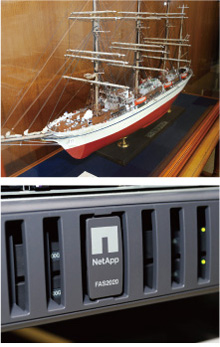
船のブロックは、切断、曲げ、溶接など、鋼板や鋼材を加工してつくられる。その中身は複雑だ。商船では配管やダクトなどが数千本単位、護衛艦になると数万本単位になるという。通常、ブロックに設備をとりつける作業も地上で行われるため、設備が多い護衛艦では1つのブロックが重くなる。ブロックの重さは、その大きさにも影響する。ブロックの大きさは、吊り上げるクレーン設備の能力に依存するからだ。
「造船所や船の種類によってブロックのサイズは変わってきます。横浜工場では、商船が数十ブロック、艦艇がその5倍から10倍くらいのブロック数です。ブロックはミリ単位の精度で数百メートルに渡って組み上げていきます。船の製造は、その大きさや精度などの要件から自動化を図ることが難しく、職人の技を求められる部分も多くあります」(溝川氏)
詳細設計が終わったブロックから製造し、どんどん組み上げていくスタイルも特徴的だ。自動車のように製造ラインで何百台も生産するのとは異なり、基本的にオーダーメイドとなる船では、個別受注生産における効率性の追求が重要になる。ブロック建造方式なら設計しながらつくることによる製造期間の短縮だけでなく、例えば鋼板や鋼材の加工でも、これはAの船、次はBの船と、複数の船のブロックを一緒につくることが可能だ。
横浜工場では1隻建造するのに、商船が約2年、護衛艦が約5年を要する。「船の大型化、高度化が進む中、時間はいくらあっても足りません。設計や製造工程の効率化、品質向上には常に取り組んでいますが、船の建造ではプロトタイプをつくることができないこともあって、後工程で実際に現物を目にすることで初めて見えてくる課題も多く、作業のやり直しが発生するなどの非効率な側面があります。さらに効率や品質を高めるためには、設計段階で、できるだけ具現化して、関係者が設計の仕様や内容について確認できる仕組みが必要でした」(溝川氏)
現実に船のプロトタイプをつくるのは不可能だが、バーチャルな世界なら可能になる。3次元CADを活用した3次元モデルが船のつくり方を変えようとしている。
設計情報を具現化した3次元モデルをプロトタイプとして活用
2004年、横浜工場は3次元CADを導入した。そのきっかけとなったのが護衛艦「ひゅうが」の建造である。「ひゅうが」は日本で初めてつくる新型の船で、前例のないことばかりだった。例えば、その大きさ。これまでの護衛艦は、全長150m前後、基準排水量7,000トンくらいが最大サイズだったが、「ひゅうが」は全長197m、基準排水量13,950トン。構造も通常は左右対称だが、甲板上に設けられた指揮所となる艦橋が右舷に寄せられて非対称となっている。ヘリコプターの離着陸時に艦首から艦尾まですべてを利用可能にするためだ。護衛艦の目的に加え、災害派遣などの人道支援任務の役割も担い、緊急の災害対策本部として使用できる大型会議室などの設備もある。
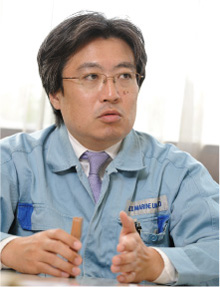
「前例がないにも関わらず、納期は通常の護衛艦と同じ5年です。納期を守るためにはお客様のご要望をできるだけ設計段階で反映させておく必要がありました。3次元CADの導入は、使うことが第一ではなく、設計情報を具現化した3次元モデルというプロトタイプをつくることによって設計品質を高めていくことが目的でした」と溝川氏は説明する。
防衛省との打ち合わせでは3次元モデルの真価が遺憾なく発揮された。例えば、3次元モデルの中を人が歩いて進んでいるかのように、歩く人の視点でシミュレーションを行い、その結果をスクリーンに投影。見るべき表示板が見えるかどうか、見え方はどうかなどを確認した。物を運ぶ商船の乗員は数十人、護衛艦の場合は数百人、居住性も重視されるためだ。
また、設計者にとっても平面では見えなかった部分も見ることができるのは大きなメリットになる。横浜工場では1隻の船に約200人の設計者が携わる。それぞれが、構造、武器関係、電機関係、操縦装置や動力機関、居住区などのグループに分かれ、なおかつブロックごとに設計を進めていく。配管やダクトなどがぴったり合うかどうか、3次元モデルなら上下左右どこからでも見ることができ、多角的に検討できる。
「ひゅうが」のプロジェクトで導入後、3次元CADの活用は積極的に進められ、現在では全面適用されている。
仮想化により2つの工場の負荷分散、リソースの有効活用を実現
2010年、3次元CADを活用した船の設計、製造プロセスの改革は新たな局面を迎えていた。テーマは、IHIMUが誇る2つの工場、横浜工場と呉工場のより密接な連携によるものづくりパワーの結集だ。具体的には、横浜工場の設計部門の作業負荷が増大した場合、呉工場で設計を行い、横浜工場で製造するといった連携が考えられていた。
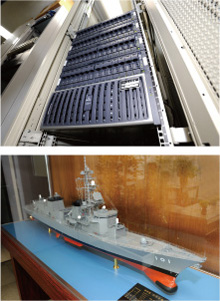
工場間でシームレスに設計データを運用できる仕組みをいかにつくるか。3次元CADの機能を活用することで3次元データの共有は実現できる。問題は、膨大な設計データの管理だった。1鑑の建造で生じるデータ量は、3次元CADデータなど、全体で約5テラバイト。設計データは保存しておく必要があり、今後もデータ量は増加傾向にあることから、両方の工場に設計データを管理する専用サーバやストレージを導入していては、コストもシステム管理の手間も増大するばかりだ。
3次元CADの導入にも携わった同部 横浜システムグループ 澤野光海氏が、こうした課題の解決策として考えたのは仮想化技術の活用だった。「仮想化を活用することで横浜工場に2つの工場の設計データの管理サーバを集約し、ストレージも共有して設計データの一元管理を実現します。データ量の増大に応じていちいちハードウェアを購入するのではなく、必要に応じてリソースの組み替えや拡張が容易に行える点も採用の大きな理由です。また基幹システムなので、仮想化の優れた冗長性もポイントになりました」と、澤野氏は語る。
変化に対して迅速かつ柔軟に対応できる点も重視された。「入力するオペレーターの人数もピーク時と平時では大きく違いますし、仕様変更などの予測がつかない事態も生じます。状況によって必要なリソースが変化する中、急にCPUやメモリを増やすといっても物理サーバでは融通がききません。仮想化を活用すれば、2つの工場の負荷分散とリソースの有効活用が容易に実現できます」と同部 横浜システムグループ 杉山靖尭氏も説明を加える。これまでの実績から仮想化ソフトウェアにはVMware、ストレージにはNetAppの採用はほぼ決まっていた。NetAppの導入は丸紅情報システムズが行っていた経緯もあって相談したところ、仮想化インフラパッケージ「MVP(MSYS Virtualization Package)」の提案があった。
MVP は、VMwareとNetApp、サーバに日本ヒューレット・パッカード社製サーバをセットで提供、仮想化のニーズにトータルで応える。事前の動作検証が不要となるため、短期間で構築が可能だ。2010年11月に導入し、2011年1月には本稼働。当初の予測よりもリソースの増強が必要となるケースも生じたが、仮想化により拡張も容易に行うことができたという。
現在、横浜システムグループでは3次元データの製造などへの活用とともに、災害対策を目的に横浜工場と呉工場で互いにデータをバックアップできる仕組みの実現にも取り組んでいる。「技術の前に全員が平等であること」を大切にする企業風土のもと、若いスタッフの自主的な提案も多いという。「造船業の情報化はまだまだこれから。やるべきことはいっぱいあります」と溝川氏は言葉に思いを込める。
横浜工場の情報化を前進させる契機となった「ひゅうが」。前例がなく、技術者が心血を注いで建造した新時代の護衛艦は、東日本大震災の際、三陸沖で災害支援活動を行った。船が運んだのは物資だけではないだろう。復興への希望、意志、そして祈り、たくさんの思いを載せて。