モデルベース開発(MBD)とは?
モデルベース開発(MBD=Model Based Development)とは、シミュレーション技術を活用したソフトウェアや組込みシステムの開発手法の一つです。コンピュータ上の計算式などを含む「モデル」、すなわち“動く仕様書”を用いて、複雑な制御システムなどの動作をシミュレーションし、コンピュータ上で妥当性の検証までを行うことで、効率的にシステムを開発するのを支援する手法です。
モデルベース開発(MBD)の普及
もともとモデルベース開発(MBD)は、家電製品や産業機器などの機械を制御するソフトウェアを開発するための手法を指すものでした。しかし、現在ではソフトウェア開発だけでなく、制御対象そのものの開発、すなわち機械・電気分野の設計・開発にもその手法が取り入れられています。
自動車業界でのモデルベース開発(MBD)の活用
特に自動車業界では、既に車両制御システムの開発などにおいてモデルベース開発(MBD)が活用されています。たとえば、車両の動力学モデルや燃費モデル、ブレーキシステムのモデルなどを構築し、これらのモデルを用いて制御システムの開発や評価に利用されています。
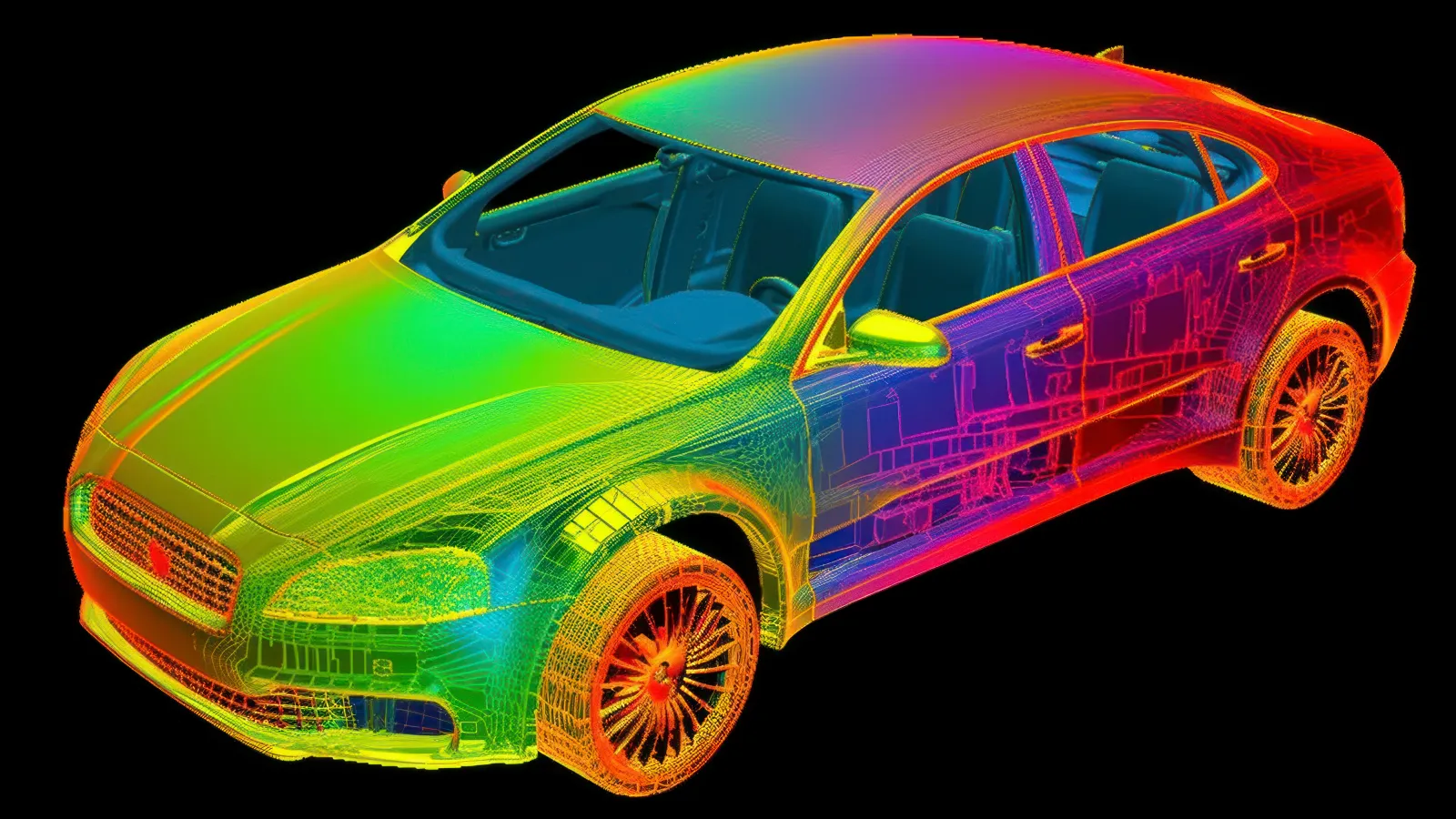
モデルベース開発(MBD)を用いることで、設計段階でも現物の動作をコンピュータ上で模擬して把握することができ、試作と実験のプロセスを削減することで開発期間の短縮と開発コストの削減を実現することができます。
モデルベース開発(MBD)が注目される背景
モデルベース開発(MBD)が注目される背景について2つの視点からみていきましょう。
短くなる製品ライフサイクルと多様化する市場ニーズ
近年、製品のライフサイクルが短くなっており、その結果、製品開発に費やす時間も短縮せざるを得なくなっています。たとえば、自動車業界では、製品の差別化戦略の一環として、マイナーチェンジを含めたモデルチェンジが頻繁に行われるようになっています。一方でエンジン制御や排出ガス規制への対応、ADAS(先進運転支援システム)など、時代を追うごとにシステムは大規模化・複雑化しており、多様化する市場ニーズにも迅速に応えることが求められています。そのため、モデルベース開発(MBD)は複雑化する制御システムだけでなく、制御対象そのものの開発にも活用されるようになり、適用範囲が広がっています。
開発の上流工程でモデルの妥当性を検証できる
自動車業界では、開発した制御システムを実車でテスト・検証しますが、これは実車が用意できる開発の下流工程までできません。そのため、その段階で制御システム自体にミスや欠陥が見つかれば手戻りが発生し、開発工程を上流までからやり直さなければなりませんでした。従来の開発手法では、1台の車両を開発するのに5年以上かかるといわれ、状況によっては試作車両を何度も作り直す必要があり、多くの時間とコストがかかっていました。
しかし、モデルベース開発(MBD)では、開発の上流工程でモデルの妥当性を検証できるため、実車テストに至ってから手戻りが発生するリスクが軽減されます。
また、近年は自動運転のレベルが高度化し、システムが運転操作を判断するようになってきています。そのため、さまざまなトラブル発生や運転シーンなど、膨大なシミュレーションが欠かせません。しかし、その膨大なシミュレーションをすべて実車で検証するのは、時間的にもコスト的にも難しいといえます。モデルベース開発(MBD)では、コンピュータ上で多くのシミュレーションを行うことができるため、実機検証を削減し開発プロセス全体の効率が向上します。
こうした背景から、モデルベース開発(MBD)は1990年代から自動車産業で導入が進み、近年では航空機産業や宇宙産業でも積極的に活用されはじめています。
モデルベース開発(MBD)のメリット・デメリット
モデルベース開発(MBD)のメリットとデメリットについてみていきましょう。
モデルベース開発(MBD)のメリット
モデルベース開発(MBD)導入の最大のメリットは、開発の上流工程である設計段階でバリデーション(妥当性検証)を実施できることです。従来の開発プロセスでは、開発する制御システムが完成するまでバリデーションを行えませんでした。しかし、モデルベース開発(MBD)では、設計段階でバリデーションを行うことができます。
たとえば自動車のエンジンや制御装置の場合、温度などの環境変化による動作の変化を実車で検証するのは手間がかかります。低温から高温まで温度設定を用意する必要があるなど、条件設定が難しいからです。
しかし、モデルベース開発(MBD)では、モデルに基づいてシミュレーションを行うため、環境条件の設定はソフトウェア上で変更するだけです。そのため、条件設定などの準備にかかる時間や工数が不要になります。
さらに、一度作成したモデルは、必要に応じて再利用・改良することができます。そのため、モデルそのものをライブラリ化すれば、精度の高いモデルを関係者間で共有することができます。
このように、何度も試作を繰り返したのちに製品化するような製品や、実機検証では網羅しきれない多数のケースが想定されるシステムには、網羅的に検証できるモデルベース開発(MBD)の手法の親和性は高いといえます。したがって今後は自動車の他にも、航空宇宙、鉄道やロボット、物流機器、医療機器などの分野でも採用が進むことが見込まれます。
モデルベース開発(MBD)のデメリット
モデルベース開発(MBD)のデメリットは、従来の開発手法に比べて設計段階の工数が増えることです。設計段階でシミュレーションを行ってモデルを検証し、その検証結果を開発作業に反映させるため、本来であれば開発の下流工程で行う検証作業を、設計段階で行うことになります。
もちろん、開発の下流工程である実機検証からの手戻りの発生を減らすなど、工程全体を効率化することになるため、全体の開発期間の短縮にはつながります。
しかしその反面、設計段階の工数が増えることを前提に、設計者の増員や技術習得のフォローアップの実施など、開発プロジェクトによっては体制の見直しが必要になるという側面も考慮する必要があります。このようなことから、実機による検証や制御を伴わないUI中心の事務用ソフト、スマホアプリのようなソフトウェアの開発には現在のところ採用は進んでいません。
モデルベース開発(MBD)の将来性
モデルベース開発(MBD)は、技術の進化とともにその重要性を増しています。今後、さらなる応用範囲の拡大が期待されています。
今後の技術トレンド
モデルベース開発(MBD)は、AIやIoT、5Gといった先端技術と組み合わせることで、新たな可能性を開拓しています。特に、デジタルツイン技術との連携が注目されています。
デジタルツインは、物理的な製品やプロセスを仮想空間で再現する技術であり、モデルベース開発(MBD)と親和性が高いです。この組み合わせにより、開発段階でのシミュレーション精度がさらに向上し、リアルタイムでのフィードバックを活用した開発が可能になります。
また、クラウド技術の進展により、モデルの共有や遠隔地からのコラボレーションが容易になり、グローバルな開発体制を支援します。
新しい活用分野
モデルベース開発(MBD)は、従来の自動車や航空宇宙分野だけでなく、新しい活用分野へと広がりをみせています。
たとえば、製造業においては、プロセスの最適化や設備のメンテナンス計画に役立ちます。シミュレーションを用いることで、実際の問題が発生する前に予測し、対策を立てることができるのです。
さらに、医療分野でもMBDの利用が進んでいます。患者データをモデル化し、個別化医療の実現に貢献するなど、多様な分野でその効果が期待されています。
モデルベース開発(MBD)の成功のためのポイント
モデルベース開発(MBD)の成功のためには特に以下の2点のポイントに留意しましょう。
モデルの精度を高める
モデルベース開発(MBD)を円滑に進める上で重要なポイントは、モデルそのものの精度です。モデルベース開発(MBD)では、実際の制御対象である製品や部品の形状や挙動を数式などでモデル化します。そのため、実際の製品や部品とその挙動をモデルがどれだけ正確に再現できるかがポイントとなります。
近年、「デジタルツイン」という言葉が注目されていますが、モデルベース開発(MBD)で使用するモデルは、デジタルツインと呼べるほど、現実世界の物理的なモノやシステムを正確にデジタルモデル化されたものであることが望ましいといえます。
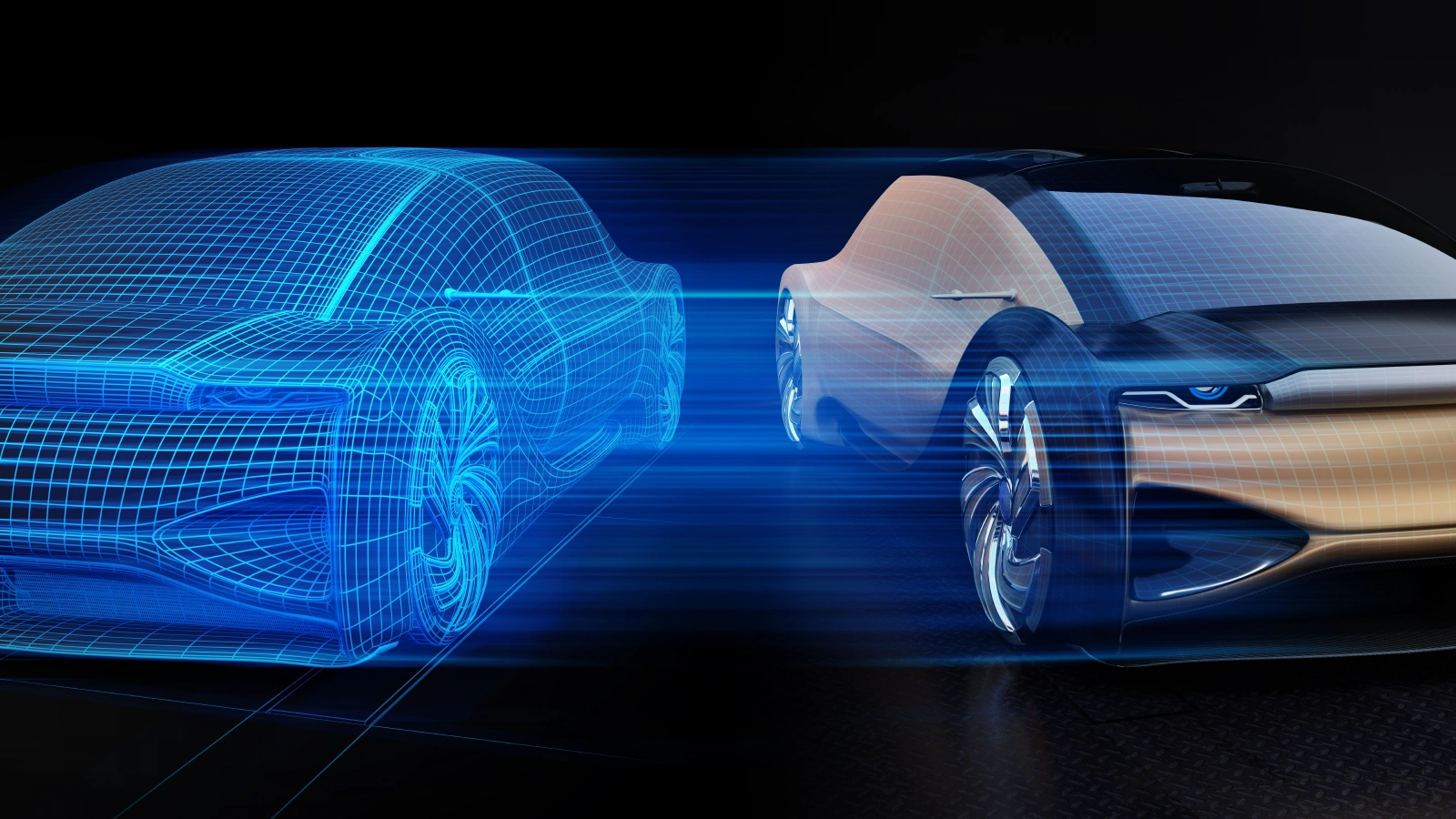
そして、デジタルツインと呼べるほど精度の高いモデルを同定し運用するためには、モデルそのものの妥当性を確認するため、徹底的な実験が欠かせません。実験で得られた実測データとモデルで予測したデータを比較し、モデルの妥当性を実機で確認します。これら二つのデータに大きな乖離があれば、モデルを改良し、より精度の高いモデルになるよう合わせ込みをしていきます。
計測データが重要
モデルベース開発(MBD)の最終目標は、「机上ですべてを予測し、開発プロセスを完了させる」ことです。しかし実際には、プロトタイプを作り、実機による検証を行うことが現状では不可欠です。このとき、実測データが不正確であったり、そもそも測定自体が不十分な手段であったりすると、検証が不十分なまま開発が進んでしまうリスクが高まります。そのため、実験に用いる計測技術は、モデルの精度を向上させる上で非常に重要となります。
モデルの精度レベルを向上させるために、実験で使用する計測技術として、3DスキャナやDIC(Digital Image Correlation=デジタル画像相関法)を活用した画像計測による3次元計測技術が有効です。特に、近年の自動車の電動化に伴い、電子部品や電池の性能や信頼性、安全性の評価のために、漏れなく全領域を迅速に計測することが求められる場面では、画像計測による3次元計測技術が非常に有効です。
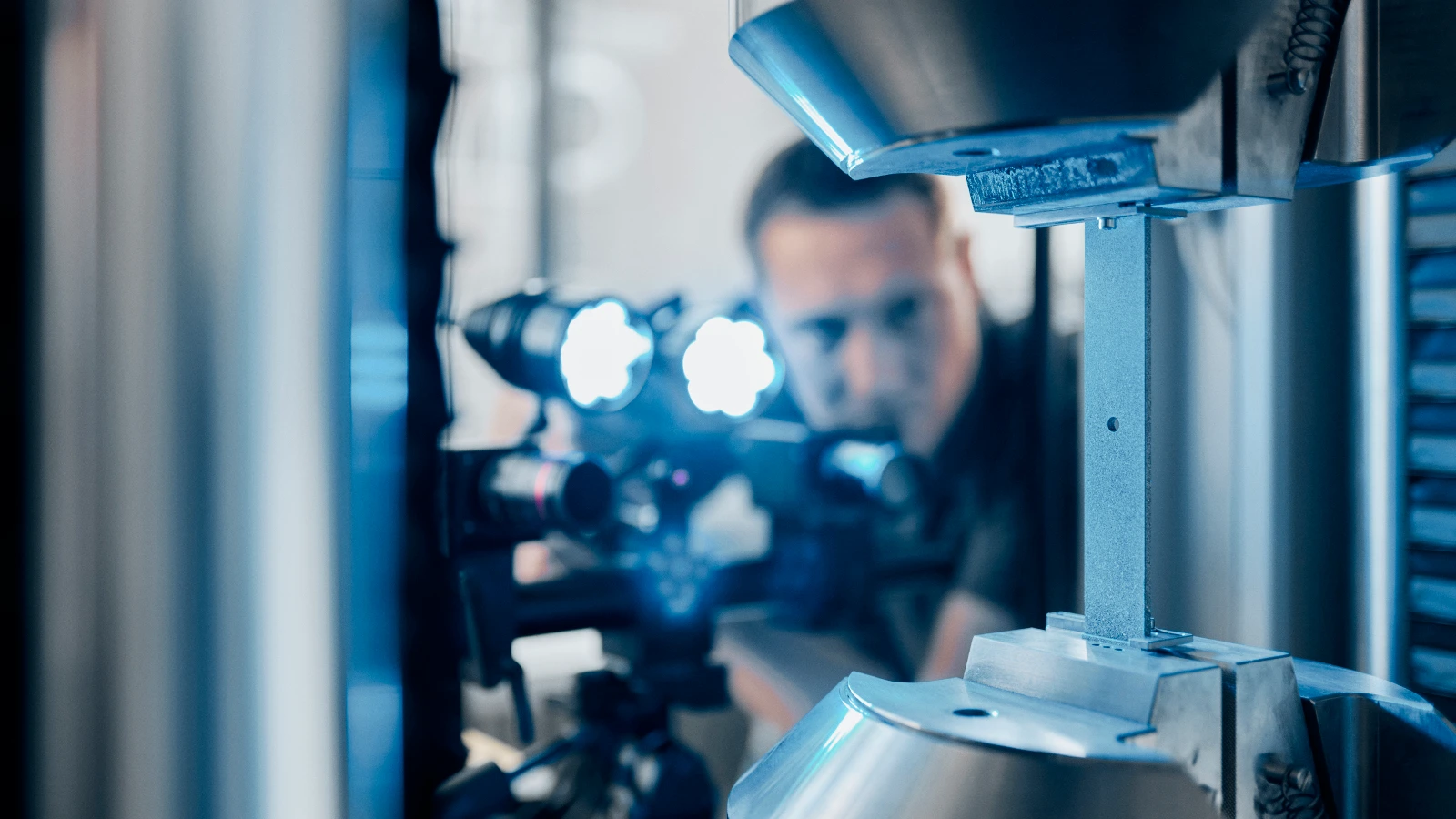
画像計測を用いた3D計測技術は、測定対象である製品や材料を非接触で計測するため、測定対象の特性に影響を与えたり、対象の温度などにより計測センサが影響を受けたりすることなく計測することができます。また、画像計測では一般的に高解像度のカメラや光学系を使用するため、精度の高い計測結果が得られるというメリットがあります。
非接触型の光学計測システム「ARAMIS」
従来の計測システムでは、対象物にセンサを1点ずつ取り付けて計測するのが一般的でした。この場合、測定されるデータは、当然センサを取り付けた部分のデータのみとなります。極端な話、センサを取り付けた位置から10mmしか離れていなくても、値が本来知りたい箇所のものと異なることもあります。しかし、従来はそのような部分的な測定データを測定結果として使用していました。
対象を全領域で可視化
これに対し、非接触光学計測システム「ARAMIS」は、対象物にセンサを取り付けず、高精度カメラで全体を画像として計測し、対象全体の変位などの挙動に加え、ひずみや応力の計測結果を対象の全領域で可視化します。
3次元的に計測・可視化
「ARAMIS」を活用することで、自動車などの製品や部品の実機を動かしたときの形状や変形を3次元的に計測し、可視化することができます。こうして得られた計測データは、机上のシミュレーションの結果と比較することで解析結果の妥当性確認にも活用できます。
たとえば、自動車のドアを開閉する際、ドアのどの部分にどれだけの力がかかるかをモデルで予測することができます。そして、「ARAMIS」が実車でドアの開閉を動画撮影し、可視化・定量化された計測結果をモデルの予測値と3Dのデータ同士で視覚的かつ定量的に比較することで、モデルの妥当性の確認をスムーズに行うことができます。
モデルベース開発(MBD)により、制御システムや制御対象の開発期間を短縮し、効率的な開発プロジェクトを実現できることはすでに触れたとおりです。このような開発プロジェクトに「ARAMIS」を導入することで、モデルの精度の向上を図ることができ、開発スピードをさらに推進して開発コスト全体を削減することができます。
本記事に関連する資料のダウンロード
3D DICシステムの資料がダウンロードいただけます