光造形3Dプリンターとは
光造形方式とは、液状の光硬化性樹脂に光(紫外線)を当てて固化させ、それを何層にも重ねて造形物を作る方法です。数ある3Dプリンターの造形方式の中でも、熱溶融積層(FDM)方式と並ぶ代表的な造形方式といえます。
光造形方式の特徴は、他の造形法に比べて比較的大きな造形物ができることです。また、造形物の表面は比較的滑らかであるため、美しい形状を得やすく、寸法精度も比較的高いです。一般に光造形方式は、曲面や複雑な形状の造形において、他の方法よりも優れています。
光造形3Dプリンターの歴史
光造形方式を用いた3Dプリンターは、3Dプリンターの中でも最も歴史が古い造形方式です。この方式のベースとなる原理は、1980年に日本の小玉秀男氏によって発明されたものでした。
その後、この原理を用いて、1986年に世界ではじめて光造形方式の3Dプリンターを製品化したのが、アメリカの3D Systems社です。この技術の特許は3D Systems社の創業者が取得していましたが、2006年に基本特許が失効してからは、多くのメーカーが光造形方式の3Dプリンターを開発・製造するようになり、現在に至っています。
光造形3Dプリンターの出力種類の違い(SLA方式とDLP方式、LCD方式)
光造形方式には、出力方式の違いなどによっていくつかの種類があります。主な方式としてはSLA方式、DLP方式、LCD方式の3種類が代表的です。
SLA方式の特徴
SLA(Stereo Lithography Apparatus)方式は、光源にレーザーを使用し、固めたい箇所にレーザーを当てて樹脂を硬化させ、それを積層していくという方式です。
バスタブのような容器に液体状の光硬化樹脂を貯め、その液面に対して、ガルバノミラーを使って光の反射角度を制御しながらレーザーを当てていくことで、必要な箇所だけを固め、それを積層させていくことで造形物を造ります。
SLA方式は比較的大きな造形物を造れるという特徴があり、また、近年では比較的耐熱性の高い材料を使用することができるので、強度のある造形物を造れるということも特徴として挙げられます。
ただし、造形後にUVライトによる2次硬化が必要で、「未硬化樹脂の洗浄→2次硬化」といった複数のプロセスが必要となります。また、バスタブのような大きな容器を使うため、大量の材料(液体状の光硬化樹脂)が必要となり、材料を頻繁に変えにくいというデメリットがあります。基本的な運用としては、1年、2年といった長期間にわたり同一の材料を使うことが多くなります。
一方でSLA方式の3Dプリンターも小型化が進んでおり、小型のものであれば、材料費は節約でき、材料交換も手軽に行えます。しかし、造形サイズは小さくなってしまうというデメリットもあります。
DLP方式の特徴
DLP(Digital Light Processing)方式は、光源にプロジェクターを使用する方式です。SLA方式がレーザーを使って一筆書きの要領で材料を固めていくのに対して、DLP方式は面で照射することができるため、造形スピードが速いという特徴があります。SLA方式は古くから大型装置として使われてきましたが、DLP方式は光造形方式の中でも、比較的筐体がコンパクトである点も特徴です。
DLP方式の3Dプリンターは、試作品の製作や、非常に細かくて小さなものを造形するのに優れており、宝飾関連の造形に使われることも多くあります。
なお、DLP方式には、波長が385㎚のものと、405㎚のものがあり、波長が強い385㎚の方が、2次硬化前の造形物についてはより強い強度が得られるという利点があります。この違いにより、サポート材が多く必要か、少なくて済むのかが違ってきます。385㎚で造形すると強度があるので、サポート材は少なくて済みますが、405㎚で造形すると、385㎚の場合よりも多くのサポート材で支える必要が生じます。
たとえば、吊り下げ式のDLP方式の3Dプリンターの場合、材料の入った容器の下から紫外線を照射し、一層ずつ積層していき、プラットフォームと呼ばれる土台がそれを引き上げていきます。この時、強度が弱いと造形物が落ちてしまうことがあります。そのため、強度を強くするか、造形物が落ちないようにサポート材を多くつけることが必要になります。
LCD方式の特徴
LCD(Liquid Crystal Display)方式は、光源として液晶ディスプレイを使用する方式です。液晶パネルを発光させて液体状の光硬化樹脂に照射し、必要な部分を固めて積層していくというものです。DLP方式と同様の仕組みで、光源だけが異なっているというものです。造形できるものについても、LCD方式はDLP方式とほぼ同じです。
液晶ディスプレイは、光源となるLCD方式が比較的安価であるという特徴があります。ただし、液晶ディスプレイは定期的に交換する必要があることと、DLP方式の385㎚のような強い波長を出すことができないため、強度が求められる造形物の製作には向いていないというデメリットがあります。
光造形3Dプリンターの材料
光造形方式の3Dプリンターでは、ベースとなる材料がエポキシ系もしくはアクリル系が中心で、そのため特殊な材料を除けば、最終製品としての造形にはあまり向いていないといわれていました。
しかし最近では、DLP方式の光造形方式の3Dプリンターが完成品として使用できる製品を製造できるようになってきており、一概に光造形方式が完成品製造に不向きとはいえなくなってきています。
使用可能な材料についても、耐熱性の高いもの、靭性の高いもの、また透明な材料なども使えるようになっており、バリエーションは増えています。たとえば透明な材料を使うことで、ある造形物の内部構造などを評価する筐体試作に活用されたり、内部に水や空気が流れる状態を確認するといったことも可能になります。
また、単純に耐熱性や強度を求める場合にもFDM方式は使えますが、FDM方式の場合、密度を100%にすることが難しく、隙間ができてしまいます。そのため、水や空気が入るものを造形する場合は、FDM方式よりも光造形方式の方が優れており、透明な素材が使えるというメリットもあって用途が広がっています。
サポート材と後加工
FDM方式の3Dプリンターなどの場合、モデル材とは別に専用のサポート材料を使用できるものもありますが、光造形方式の場合には、同一材料によりサポート材をつけることになります。
サポート材は造形物ができ上がった時点で取り除く必要がありますが、造形物との接触部分を物理的に切り取る必要があるため、どうしても破断面ができてしまいます。そのため、どこにサポート材をつけるかを考慮する必要があります。デザイン上、破断面が残ってはいけないところにはサポート材をつけないようにするなどの配慮が不可欠です。他の方式に比べて、この点が光造形方式で、ひと手間増える部分でもあります。
また、光造形方式の場合、サポート材を取り除くといった後加工の加えて、造形物を溶剤で洗浄する処理も必要です。造形物が完成した段階では、造形物の全面に液状の光硬化性樹脂が残っています。この残った樹脂は溶剤で洗浄する必要があります。さらにその後、2次硬化(UV硬化)という後加工も必要になります。
光造形3Dプリンターのメリット・デメリット
光造形方式の3Dプリンターのメリットとデメリットについて解説します。
光造形方式のメリット
光造形方式のメリットとしては、滑らかな表面仕上げと、高い寸法精度で小さく詳細な形状を造形できることです。
また、一般的に造形スピードが早く、特にDLP方式やLCD方式なら、面単位で積層していくため、よりスピーディに造形物を造ることが可能です。
さらに、透明な材料を利用することができるため、内部構造を可視化して確認・検証するような必要がある造形物の製作に向いています。
光造形方式のデメリット
光造形方式のデメリットとしては、やはりサポート材をつける場所を予め考える必要があるという点がです。どうしても、この部分でひと工程増えてしまいます。
また、後加工も手間になりがちです。洗浄という後処理と、2次硬化が不可欠なので、この点もデメリットといえます。しかし、この後紹介する「Origin One」という3Dプリンターの場合には、超音波洗浄が可能になるなど、こうした手間を軽減できます。3Dプリンター製品によっては、こうした手間を効率的に処理できる可能性がありますので、製品選びの重要なポイントとなります。
光造形3Dプリンターの用途や活用事例
ある中古バイクショップでは、年式の古いバイクを多数扱っており、修理やメンテナンスに必要な部品・パーツなどは、すでにメーカーにも在庫がないといったものが多々ありました。そうした状況の中で着目したのが、3Dプリンターを活用して、必要なパーツを独自に復刻できないかということでした。
そのバイクショップでは、丸紅情報システムズが扱っている光造形DLP方式3Dプリンター「Origin One」を導入し、必要なパーツの復刻に活用しています。
具体的には、バイクのハーネスを取りつけるためのカプラーを「Origin One」で製作し、顧客に販売できるようにしています。バイクの部品ということもあり、一定の耐熱性や靭性が求められますが、「Origin One」なら、そうした材料が利用できるという点も選定の理由でした。
また、すでに製造されていないバイクの補給品などは、一定のニーズはあるものの、わざわざ金型を製作して量産したのでは採算が取れないという場合が多く、3Dプリンターで中量もしくは少量生産できることで、供給が可能になりました。
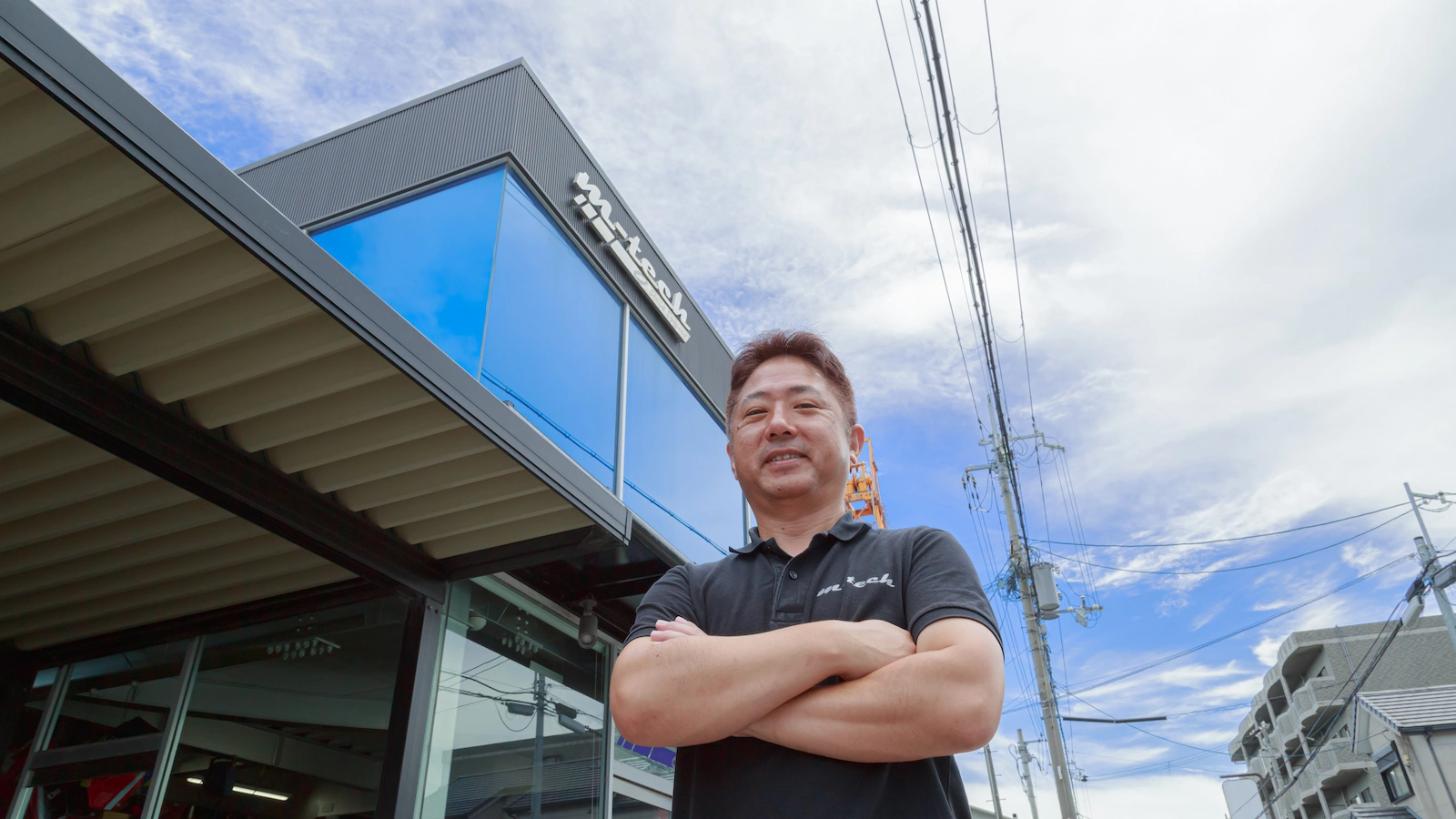
この事例のように、金型を製作して大量生産すると採算割れしてしまうが、一定のニーズが見込める部品などの分野では、光造形方式の3Dプリンターは大きなメリットをもたらします。
丸紅情報システムズ 取り扱いの光造形 3Dプリンター「Origin One」
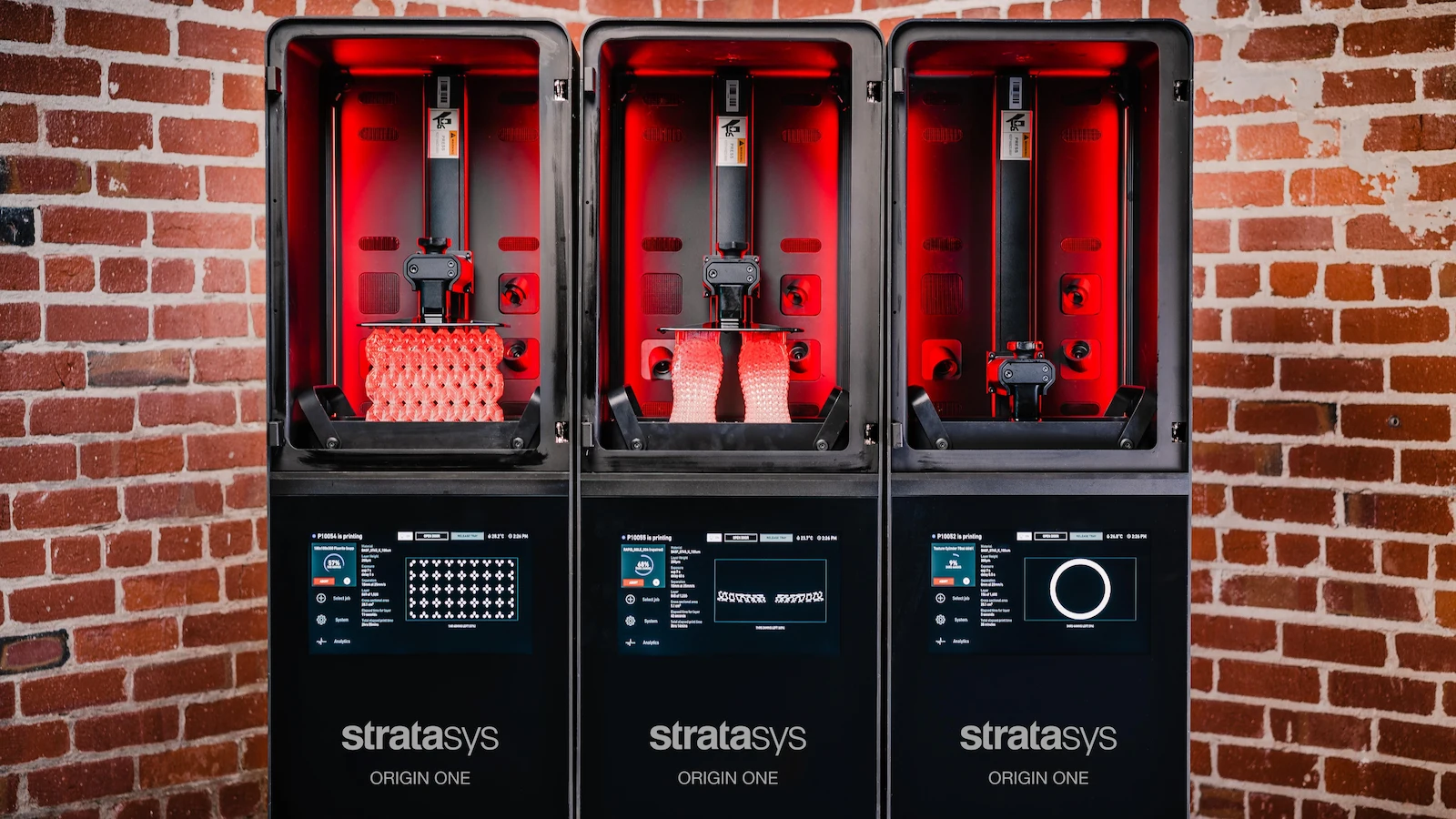
この「Origin One」には、特許技術である空圧分離メカニズムという機構が備わっています。一般的な吊り下げ式の場合、プラットフォームが硬化した樹脂を引き上げる際にトレイの底にあるメンブレン(フィルム)からしっかりとはがれる必要があります。しかし、メンブレンとその下のガラス面がうまくはがれずに造形に失敗することがあります。「Origin One」の空圧分離メカニズムでは、プラットフォームが引き上げる際にメンブレンとガラス面の間に空気を入れることでメンブレンの張力を一時的に低下させ、剥離しやすくすることで失敗を防ぐことができます。一般的にDLP方式の場合、プラットフォームに対して接触する面積をできるだけ減らすべきといわれますが、「Origin One」の空圧分離メカニズムにより、接触面積が大きくても造形がうまくいきます。
また、「Origin One」では、メーカー純正材料でなくても、プリンター側のパラメーターを適切に設定することで、多様な材料を利用できるオープンマテリアルに対応しています。
このように「Origin One」は、Origin One P3(Programmable Photo Polymerization=プログラム可能な光造形機)テクノロジーによって、3Dプリンターの可能性を高めています。
3Dプリンター 資料ダウンロード
3Dプリンターの紹介資料がダウンロードいただけます。