グローバル化が進む時代にあって、日本のものづくりはどこへ向かっているのだろう。
世界経済の不透明感が増す中、答えはなかなか見えてこないが、それでも製造現場は動き続けている。
トヨタやホンダの大半の重要保安部品で金型を製造している名古屋特殊鋼。
特殊鋼商社のノウハウと、金型メーカーとしての技術力の融合により、
他社が容易に追随できない付加価値を創造し成長を続けてきた。
その1つが、リバースエンジニアリングの活用だ。
国内金型メーカーの中でもいち早く導入し、金型製造のデジタル化を実現。
人手に依存しない生産体制を確立することで、
コスト、効率化、品質などあらゆる面で競争力の向上を図っている。
現在、同社がめざしているのは、プラスマイナス0.01mmの再現精度だ。
名古屋特殊鋼 生産技術課 野村学司氏に、金型製造におけるリバースエンジニアリングの最前線を訊いた。
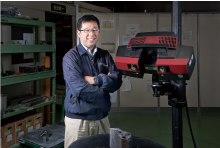
米国の日系大手自動車メーカーの要望に応える
2000年初頭、米国で現地生産を進める日系大手自動車メーカーでは、工場への部品供給が頭の痛い問題となっていた。日本で生産した部品を輸送していては、コストも時間も掛かり、為替変動の影響も大きく受けてしまう。しかし、現地での部品調達も日本でやるようには上手くいかなかった。苦境の中、日系自動車メーカーは米国で事業を展開していた日本の金型メーカー、名古屋特殊鋼に声をかけた。
名古屋特殊鋼の鍛造用金型は、トヨタやホンダの大半の車種で安全走行に欠かせない重要保安部品の製造に利用されている。またCVTミッションに欠かせない精密金型を製造するなど鍛造用金型の技術は国内トップレベルである。米国に進出したのは1999年。2003年には現地に金型製造工場も建設した。
しかし、日系自動車メーカーが要望したのは、同社が主力としていた鍛造用金型ではなく板金プレス用金型だった。鍛造は金型を使って圧縮成形する。板金プレスでは、曲げ成形を中心にして自動車のボディなど金属の板(板金)に圧力をかけて伸ばすように成形していくのが特長だ。同社は日系自動車メーカーの協力を得ながら、2004年に米国で板金プレス用金型事業をスタートさせた。1998年4月に入社した生産技術課の野村学司氏も新事業の立ち上げに携わった。担当したのはリバースエンジニアリング。実際に業務で取り組むのはそのときが初めてだった。
リバースエンジニアリングとは、デジタイザと呼ばれる3次元測定機を使って製品の先行モデルとしてつくられたクレイモデルや既存製品などの形状を測定しCADデータを作成すること。なぜ板金プレスでリバースエンジニアリングが必要なのか。野村氏はこう答える。「板金プレスの金型は複数回利用するうちに摩耗してきます。そこで二代目の金型にバトンタッチされるわけですが、問題なのは基本的に板金プレスの場合、設計してつくった金型をそのまま使うことがほとんどないということです」。
板金プレスでは高い圧力をかけるため、スプリングバックといって、金型からはずしたときにもとの形状に戻ろうとする力が働き、少し開いてしまう現象が起きる。試し打ちをして、スプリングバック量を見込んだ金型になるよう手で調整する必要があるのだ。この調整後の金型の形状を3次元データで取り込みCADデータ化しておけば、二代目の金型をつくるときには調整作業が不要となる。金型のリバースエンジニアリングによって、業務の効率化やリードタイムの短縮が図れ、グローバルな品質の均一化も実現できる。
2006年、野村氏は帰国する。日本の金型製造業では、まだリバースエンジニアリングがほとんど利用されていなかった。
リバースエンジニアリングで競争優位に立つ
名古屋特殊鋼の誕生は1965年まで遡る。創業当時は特殊鋼の商社だった。特殊鋼とは、鉄に炭素及びさまざまな合金元素を加えた鋼のこと。添加する元素によって、硬度、強度などの特性が増す。自動車の金型に使われるのは、硬度や耐摩耗性に優れた工具鋼と呼ばれる特殊鋼の一種だ。当初、世界有数の特殊鋼メーカーの総合代理店として日本の自動車関連メーカーに工具鋼を販売し、やがてさまざまな特殊鋼メーカーの素材を扱うようになった。しかし工具鋼の販売だけでは成長に限界があった。
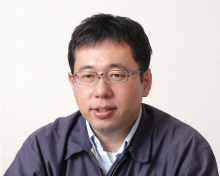
1980年代に入り、同社は第2の経営の柱とするべく金型製造事業に着手した。素材を知り尽くした上で金型の設計、加工ができる強みを活かし着実に実績を重ねた。ターニングポイントとなったのは1995年、他社に先駆けたCAD/CAMの導入だ。
金型製造では後発だった同社では常に熟練者が不足していた。CAD/CAMを最大限に活用した生産システムを構築することで、熟練者の技に頼らなくても一定の水準で金型が製造できるようになった。その後のIT化の波に上手く乗ることができたメリットも大きい。また、さらなる生産性向上のためにマシンオペレータの多能工化も進めた。野村氏も2年間、生産現場を担当した後、現在の生産技術課に異動になったという。
ITの活用と技術力の両輪により、金型製造をはじめた当時は売上げの7割が材料販売、3割が金型製造だったが、現在は8割が金型製造、2割が材料販売と完全に逆転した。野村氏が帰国した2006年からは主力の鍛造用金型に加え、国内でも板金プレス用金型事業を開始。米国で同社に仕事を依頼した日系自動車メーカーが、日本国内でも同様のサービスを求めたことがきっかけとなった。折しも環境負荷の小さいエコカーブームと重なったこともあって同社の板金プレス用金型事業の業績は急速に拡大。他社がまだ取り組んでいなかったリバースエンジニアリングが、競争優位の大きなポイントとなった。
リバースエンジニアリングの精度とスピードを支える「ATOS」
金型製造におけるリバースエンジニアリングとはどのようなものなのだろう。野村氏は、次のようなプロセスを説明してくれた。デジタイザで金型の形状を測定→測定データをもとに穴の場所など簡単な加工図面を作成→測定したデータは点群データのため、それをもとに面データを作成し3次元CADデータを生成→機械加工のためのNCプログラムをつくり型加工(形状加工)→表面処理→デジタイザで形状を測定→型加工(基準面加工)→出荷検査。リバースエンジニアリングにより測定から加工まで一貫して金型製造のデジタル化を実現している。
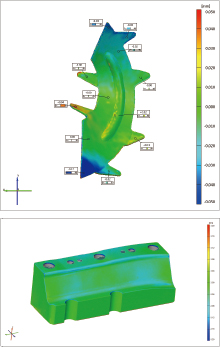
同社のリバースエンジニアリングの特長は表面処理の後工程にある。型寿命を高めるために行われる表面処理によって金型の形状は微妙に変化する。通常、金型を実際に使ってみて良し悪しを判断し、部品メーカー側で調整している。同社は、表面処理後の金型の形状を測定し、そのデータをもとに再度加工することでより精度の高い金型を提供している。
「難しいのは表面処理で生じたひずみに対し、何を基準にして最適とするかということです。データがあれば、それをもとに基準をつくることができます。当社の金型ならそのまま使っていただければ良品となります。またデータとして残りますから、次回からはお客様が望んでいる金型を迅速に提供できます。金型の改造に関してもデータ化されているため容易です」。
リバースエンジニアリングのベースとなるデジタイザは、米国で同社が利用していた設備を使っていない。米国では接触型のデジタイザを利用していたが、多くの測定時間を要したため、国内での導入では近年登場した非接触型の採用を決めていた。少なくとも1/10の時間短縮が見込まれたという。
複数社をリストアップし、最終的に光学式3次元デジタイザ「ATOS(エイトス)」が採用された。その理由について「まず精度と省スペースの観点から機械を絞りこみました。「ATOS」で特に高く評価した点は、カメラとソフトウェアの連動です。カメラとソフトウェアを別々に購入していては、覚える手間も多くなります。障害が起きた場合のメンテナンスも面倒です。三角測量の測定原理に基づいているという点もわかりやすかったですね」と野村氏は説明する。
2007年に「ATOS」を導入、仕事の依頼が増大するのに伴い、効率化を図るために2010年にはCAD/CAMシステム「Tebis(テビス)」の採用を決断。「基本的に「ATOS」の測定データの3次元モデル化、CADの役割として利用しています。以前のソフトよりも3次元形状の構成が図面から作成したCADモデルに非常に近い。精度が高いですね。その一方で、精度をそれほど必要としない部分に関してはスピードを優先するといった使い方もできるなど応用がききます。「ATOS」と「Tebis」の組み合わせにより、以前のソフトを使っていたプロセスと比較して1/3から1/5ほどの時間短縮を実現できました」
めざすのは再現精度プラスマイナス0.01mm
リバースエンジニアリングによる3次元CADモデルは、お客様への提案にも活かされているという。「金型の摩耗について、測定データと設計データをもとに比較し、摩耗している部位や程度を視覚的にわかりやすく3次元CADモデルを使ってお客様にご提案しています。そろそろ新しい金型を使うべき時期です、とデータで示すことができるのはお客様の信頼や安心感にもつながります」
リバースエンジニアリング以外に検査道具としても「ATOS」は活躍中だ。鍛造用金型では、目視でわからない曲面部分に関して「ATOS」で測定した数値を検査表に記入しているという。板金プレスでは、見た目が同じ2つの金型の3次元CADモデルを重ねてみることで差異を視覚化し、良品、不良品の判断に役立てているそうだ。
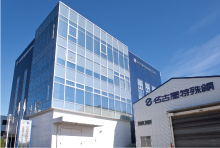
2011年2月には、最新の「ATOS Triple Scan(エイトス トリプル スキャン)」とローテーションテーブルを導入した。その効果について野村氏はこう話す。「青色LEDとトリプルスキャン技術の採用で測定性能が大幅に向上したため、反射抑制剤やマーカシールの利用も少なくなりました。また従来、測定する人と準備する人と2人がかりで1日20型の測定が限界でしたが、いまは1.5人で倍の型数が測定でき、測定のミスやモレも軽減できました」
既存の「ATOS」は米国の工場に提供することで日本の工場との連携もより密になった。日本でモデル化して、米国で加工するといったデータのやりとりも行われている。時差を利用することでリードタイムの短縮も図れるが、この点はこれからの課題になるという。
同社のリバースエンジニアリングはさらなる高みに向かっていた。同社が提示している再現形状精度はプラスマイナス0.05mm。お客様からはプラスマイナス0.01mmを求められているという。そこまで精度を高めることができれば、冷間鍛造用金型にもリバースエンジニアリングを適用できる。常温で成形される冷間鍛造では金型で加工した部品がほぼそのまま車に取り付けられる。そのため板金プレス用金型よりも高い精度と品質が必要になる。
金型業界もグローバル化が進む中、同社も2012年には東南アジアに進出を予定している。現地生産でコスト削減、リードタイム短縮といった顧客のニーズに対応するためだ。日本のものづくりはどこへ向かっているのだろう。野村氏の言葉が心に残る。「他社が追随できない技術で国内外での競争力を保っていく。リバースエンジニアリングでは0.01mmの高精度がいまの目標ですが、ミクロンレベル(0.001mm)まで視野に入れています」。答えは現場にあるのかもしれない。