SLS(粉末焼結)3Dプリンターとは
まず、SLS(粉末焼結)方式の3Dプリンターの歴史とその仕組みについて解説します。
SLS(粉末焼結)の歴史
SLS(粉末焼結)方式の3Dプリンターは、光造形方式と同様に長い歴史を持つ技術です。この3Dプリンター技術は1980年代後半にはすでに開発が始まっていました。かつてはSLS方式の3Dプリンターの中に1億円を超える高額な製品も存在しましたが、基本技術の特許失効や設備装置の小型化により、最近では企業が導入しやすい比較的安価なSLS方式の3Dプリンター製品が増加しています。
SLS(粉末焼結)3Dプリンターの仕組み
SLS(粉末焼結)方式では、ワークエリア内に粉末材料を敷き詰め、焼結させたい部分にのみレーザーを照射して固めます。一層を焼結した後、その上にさらに粉末材料を敷き、再び必要な部分にレーザーを当てて焼結するプロセスを繰り返します。このように層を積み重ねることで、立体的な造形物を作成していきます。
SLS(粉末焼結)方式は、FDM方式と同様に熱可塑性の材料を使用することができます。光造形方式などの他の方式と比較すると、SLS方式ではかなり強度の高い造形物を製作することが可能です。この特性により、SLS方式は機能的な部品や耐久性の高いプロトタイプの作成に適しています。なお、FDM方式については以下の記事で詳しく解説しています。
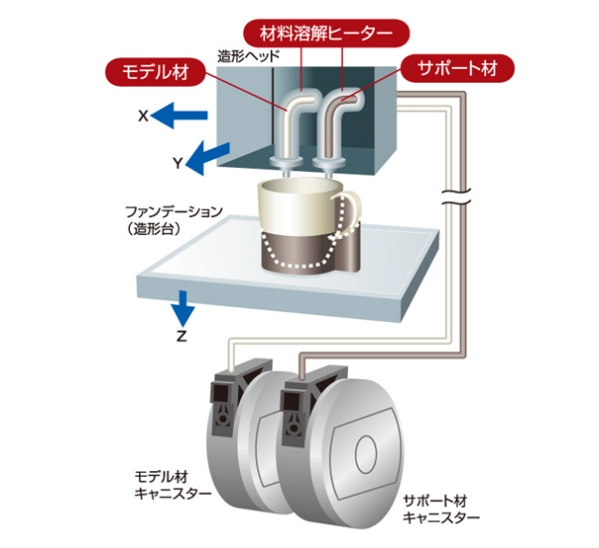
SLS(粉末焼結)の材料
SLS(粉末焼結)方式では、ポリアミド(ナイロン)素材がよく使用されます。具体的には、ポリアミド(PA)11やPA12などが主な材料です。さらに、PA12にガラスファイバーを加えることも可能です。もともと高強度の造形物を製作できるSLS方式ですが、ガラスファイバーを混合したPA素材を使用することで、PAの靭性を活かしつつ、強化繊維の追加により、より耐久性が高く破損しにくい造形物の製作が可能となりました。
ただし、SLS(粉末焼結)方式で使用できる材料には制限があります。例えば、FDM方式で一般的なABS(アクリロニトリル・ブタジエン・スチレン)やASA(アクリロニトリル・スチレン・アクリレート)などの複合材料は、各成分のガラス転移温度が異なるため、レーザー焼結時に均一に溶かすことができず使用できません。
このように、SLS(粉末焼結)方式では使用可能な材料が限定されますが、PA素材を使用できることで、靭性と高強度を兼ね備えた造形物の製作が可能です。そのため、SLS方式は、靭性と強度のバランスが求められる造形物の製作に特に適しているといえます。
SLS(粉末焼結)のメリット・デメリット
SLS(粉末焼結)方式のメリット・デメリットについて解説します。
SLS(粉末焼結)のメリット
SLS(粉末焼結)方式の3Dプリンターの主なメリットの一つは、PA材料を使用して高い靭性と強度を持つ造形物を製作できることです。これにより、壊れにくく割れにくい製品が作れます。さらに、ガラスファイバーを混ぜ合わせることで、剛性を高めることも可能です。
もう一つのメリットは、同一形状の造形物を量産する際に、1回の製造(バッチ)で比較的多くの数を生産できる点です。加えて、SLS方式の大きな特徴として、FDM方式や光造形方式で必要となるサポート材が不要である点が挙げられます。
SLS(粉末焼結)方式では、粉末材料を敷き詰めた上からレーザーを照射して必要な部分だけを焼結し、その上に新たな層の粉末を敷いて再び焼結するという工程を繰り返します。この過程で、レーザーが当たっていない部分の粉末材料がそのままサポートの役割を果たすため、特別なサポート構造が不要になります。つまり、SLS方式は実質的にサポートレスで造形が可能な技術だといえます。
SLS(粉末焼結)のデメリット
SLS(粉末焼結)方式の3Dプリンターのデメリットとしては、PA(ナイロン)という素材の特性として吸水性が高いために、水分が多い環境では素材として劣化しやすいということが挙げられます。
またレーザーによる焼結であるため、ワークエリア内も造形物も、非常に高温の状態になります。そのため、造形物が完成してもすぐに取り出すことができず、ゆっくりと造形物の温度を下げる徐冷という工程が不可欠となります。高温状態ですぐに造形物を取り出そうとすると、急激に温度が下がって、それによる収縮や反りなどが発生してしまうことになります。そのために徐冷が必要ですが、一般的に徐冷に要する時間は12~24時間程度といわれています。小物パーツであれば12~24時間、大型や複雑な造形物の場合は24~48時間程度かける事もあります。この長い冷却時間は、生産効率に影響を与える可能性があります。
さらにいえば、粉末材料を扱うので、どうしても当該粉末が装置周辺で飛散してしまい、環境面での懸念があるということもデメリットのひとつといえます。
SLS(粉末焼結)の用途や活用事例
SLS(粉末焼結)方式の用途や活用事例について紹介します。
自動車用センサーカバーの量産
アメリカで人気の高いピックアップトラックでは、フロント部分に後付けでカメラ用のセンサーカバーを取り付けることが一般的です。しかし、ピックアップトラックのオーナーは車両をカスタマイズすることが多く、その結果車高が変わることがあります。これにより、視認性の問題からフロントカメラの位置も調整する必要が生じ、適切なカメラ配置を可能にするために異なる形状のセンサーカバーが必要となります。
この問題に対応するため、車高に合わせて3種類のセンサーカバーが必要となりました。しかし、3種類の金型を製作して量産するアプローチは、時間とコストの面で課題がありました。そこで、SLS(粉末焼結)方式の3Dプリンターを活用することで、必要な強度を持つセンサーカバーの量産が可能となりました。
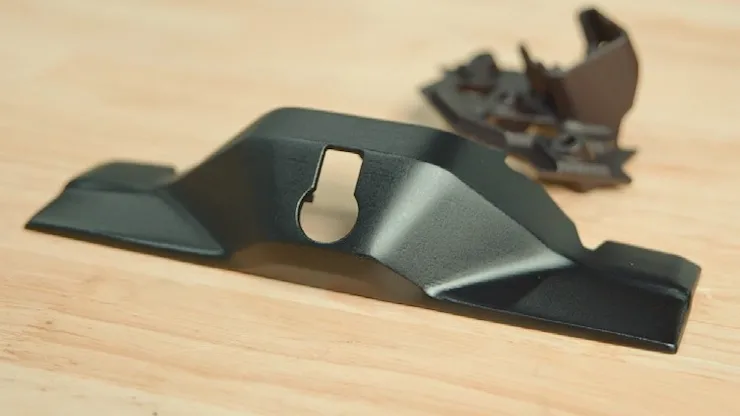
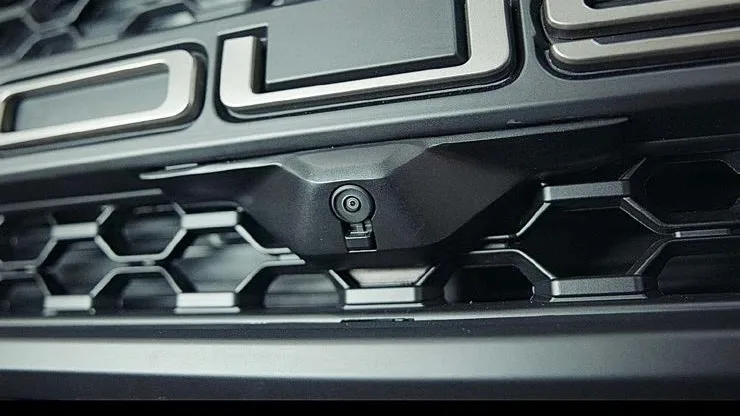
通常、このような部品の生産には射出成型が用いられますが、CADデータの完成から生産開始まで3~4か月を要します。一方、SLS(粉末焼結)方式の3Dプリンター(この事例ではストラタシス社製の「Stratasys H350」(以下、H350)を使用)を活用することで、生産期間をおよそ2か月に短縮し、さらにコストも35%削減することに成功しました。
レーシングカー用ダクトの中量生産
あるレーシングカーのプロジェクトでは、コックピット内の熱問題を解決するために、特殊なダクトの製作が必要となりました。しかし、従来のダクト製造方法では、複雑な形状のダクトを作ることが困難でした。そこで、設計の自由度が高く、目的に合致した精密なダクトの製作が可能なSLS(粉末焼結)方式の3Dプリンターを採用することにしました。
このプロジェクトで使用された3Dプリンターは、ストラタシス社製のH350です。H350で製作されたダクトは、最終部品としてレーシングカーに直接装備され、コックピット内の空気の流れを最適化することに成功しました。
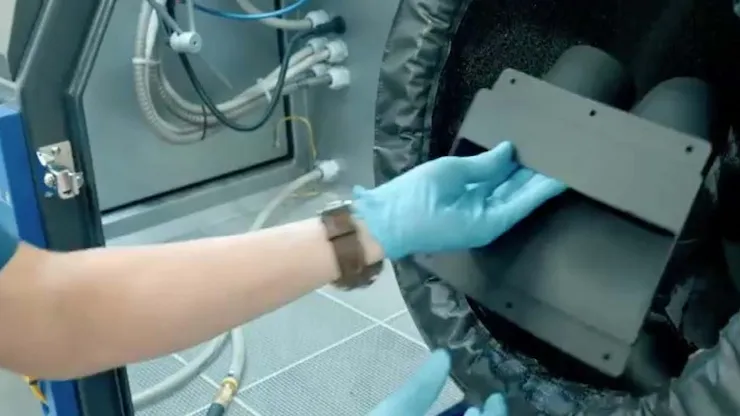
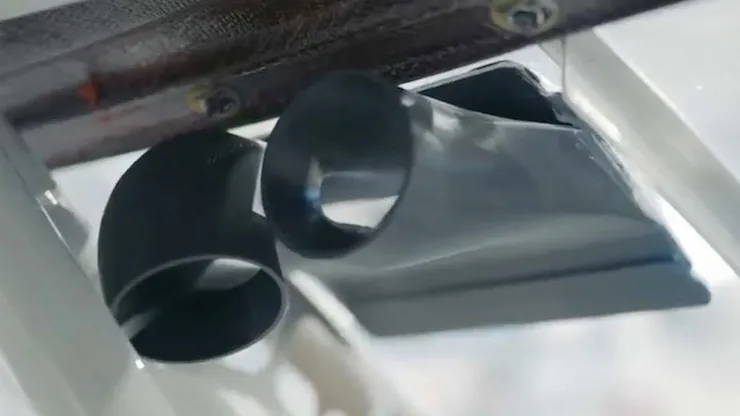
さらに、この事例では一定数量のダクトを生産する必要がありました。手作業での製作では対応できない生産量だったため、高い生産性を持つH350を活用することで、必要な数量のダクトを効率的に生産することができました。この方法により、品質の一貫性を保ちながら、短期間で必要な部品を供給することが可能となりました。
SLS(粉末焼結)方式に類似した3Dプリンター「StratasysH350」の紹介
丸紅情報システムズでは、昨今注目が高まっているSLS(粉末焼結)方式に類似した3Dプリンターとして、ストラタシス社製のH350を取り扱っています。
H350の大きな優位性は、SAF(Selective Absorption Fusion)方式を採用している点にあります。SAF方式では、SLS(粉末焼結)方式と同様に粉末材料をワークエリアに敷き詰めますが、レーザーの代わりに赤外線を使用します。この方式では、まずインクジェットプリンターのようなプリントヘッドから赤外線を吸収する液体を焼結させたい部分に塗布し、その後赤外線を照射します。これにより、液体が塗布された部分のみが焼結します。この工程を層ごとに繰り返して造形物を製作します。
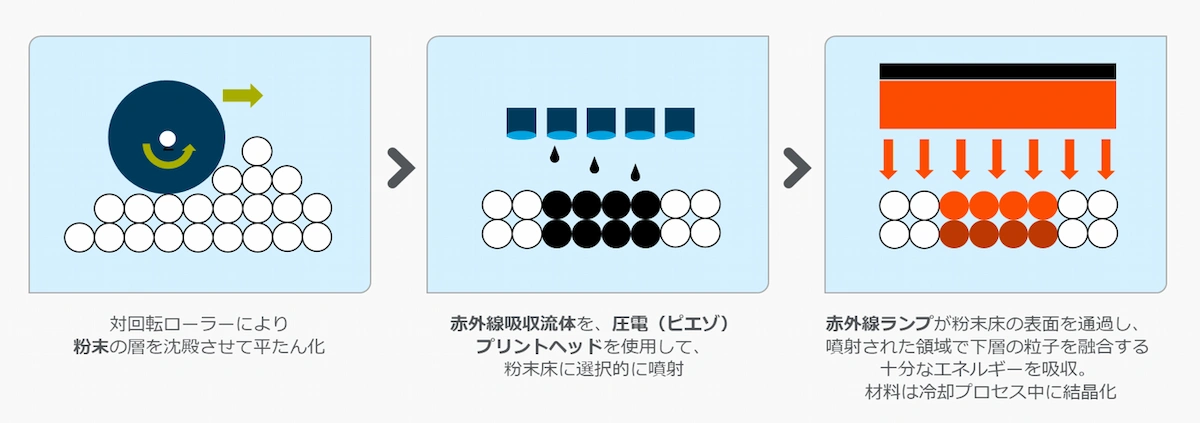
なお、インクジェット方式については以下の記事で詳しく解説しています。
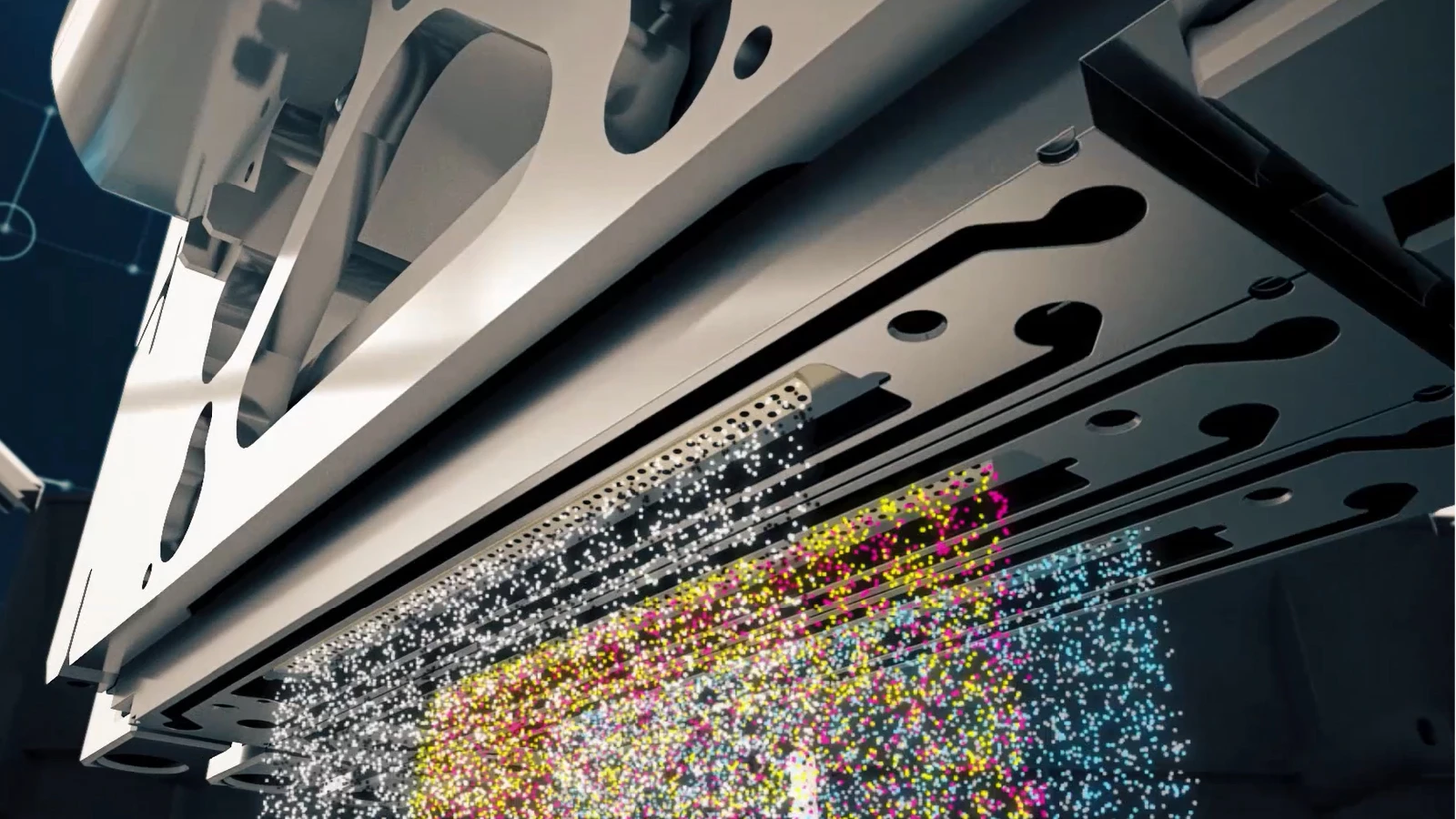
従来のレーザー方式が点で線を描くように焼結するのに対し、SAF方式は液体を面で噴射し、赤外線ランプも面的に照射するため、より高速な製作が可能です。また、ワークエリアに多くのモデルを配置しても造形時間が大幅に増加しないため、量産に適しています。
材料面でも、H350はPA11、PA12に加えてポリプロピレン(PP)も使用可能です。PPは自動車のバンパーなど多くの部品に使用されており、これはH350の大きな強みとなっています。
SLS(粉末焼結)方式の3Dプリンターでは熱管理が非常に重要です。レーザーによる高温焼結は周辺部分にも影響を与えるため、量産時には部品間に一定の隙間(クリアランス)が必要になります。このクリアランスの大きさは1バッチあたりの生産量に直接影響し、その効率はネスティング率で表されます。一般的なSLS方式の3Dプリンターのネスティング率が約8%であるのに対し、SAF方式のH350は12%と、クラス最高のネスティング率を実現しています。
3Dプリンター 資料ダウンロード
3Dプリンターの紹介資料がダウンロードいただけます。